Accounting for Subcontracting Goods Valuation¶
Subcontract is a common activity in manufacturing enterprises. During this process, businesses will need to manage the outgoing raw materials sent to the subcontractors, and control and record data to track related costs. This article will guide you through the settings of accounting accounts that record the entries of Subcontracting activities.
Requirements
This tutorial requires the installation of the following applications/modules:
Configure accounting accounts for the Sub-contracting process¶
During the sub-contracting process, some kinds of expense will be orcured such as the cost of material components that are consumed during the process, the sub-contracting expense that pay to the sub-contractors, etc. Normally, in Viet Nam, we will have the journal entries to be posted on some specific transactions such as:
Whenever delivery of the material components to the sub-contractors (For example: Debit the account of Work in progress and Credit the account of Raw materials or Purchase costs).
When receive the finished products from the sub-contractors (For example: Debit the account of Finished products and Credit the account of Work in progress).
When recording the costs that have to pay to the sub-contractors (For example: Debit the account of Work in progress and Credit the account of Trade payables).
To generate kinds of those journal entries, we need some configuration as follow:
On the Raw materials product categories:
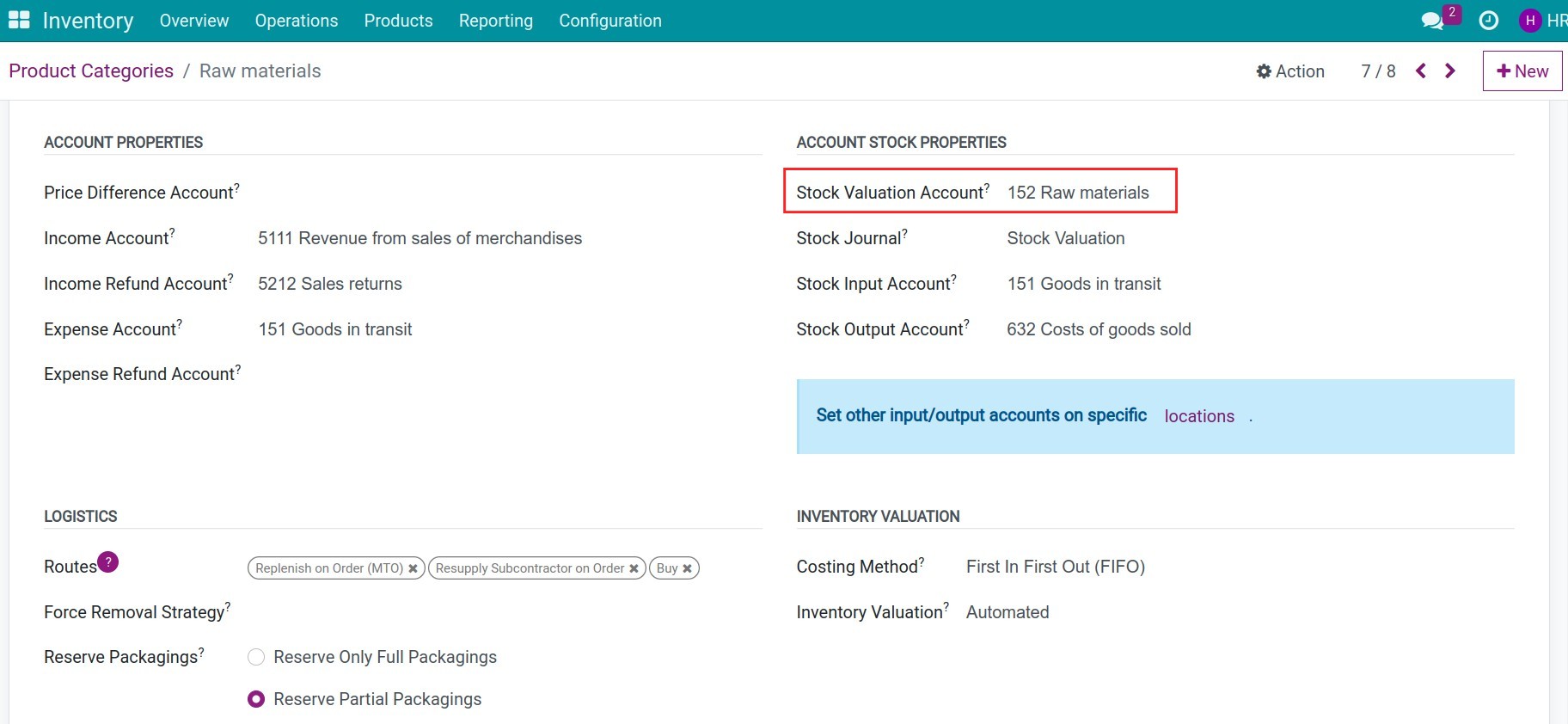
On the Finished product categories:
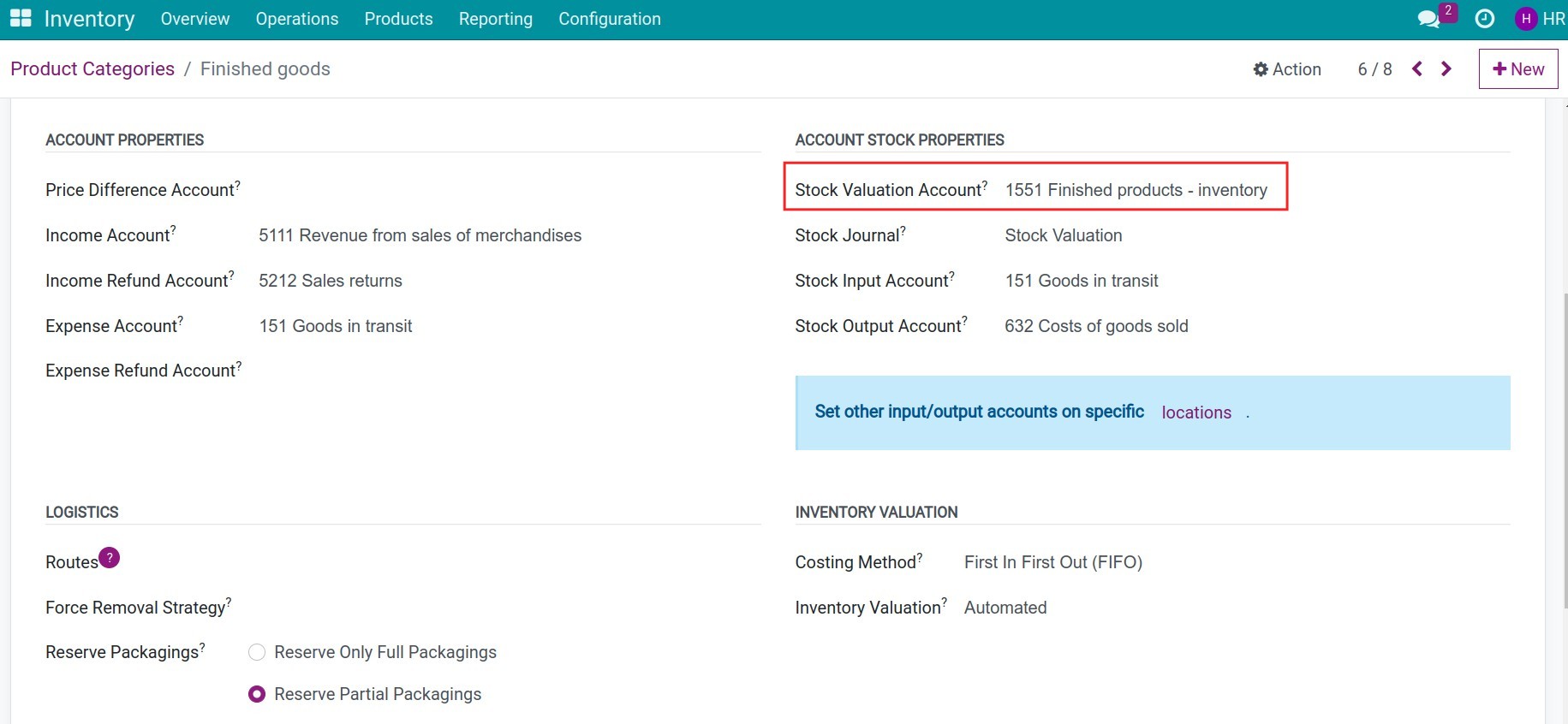
On the sub-contracting expense product categories:
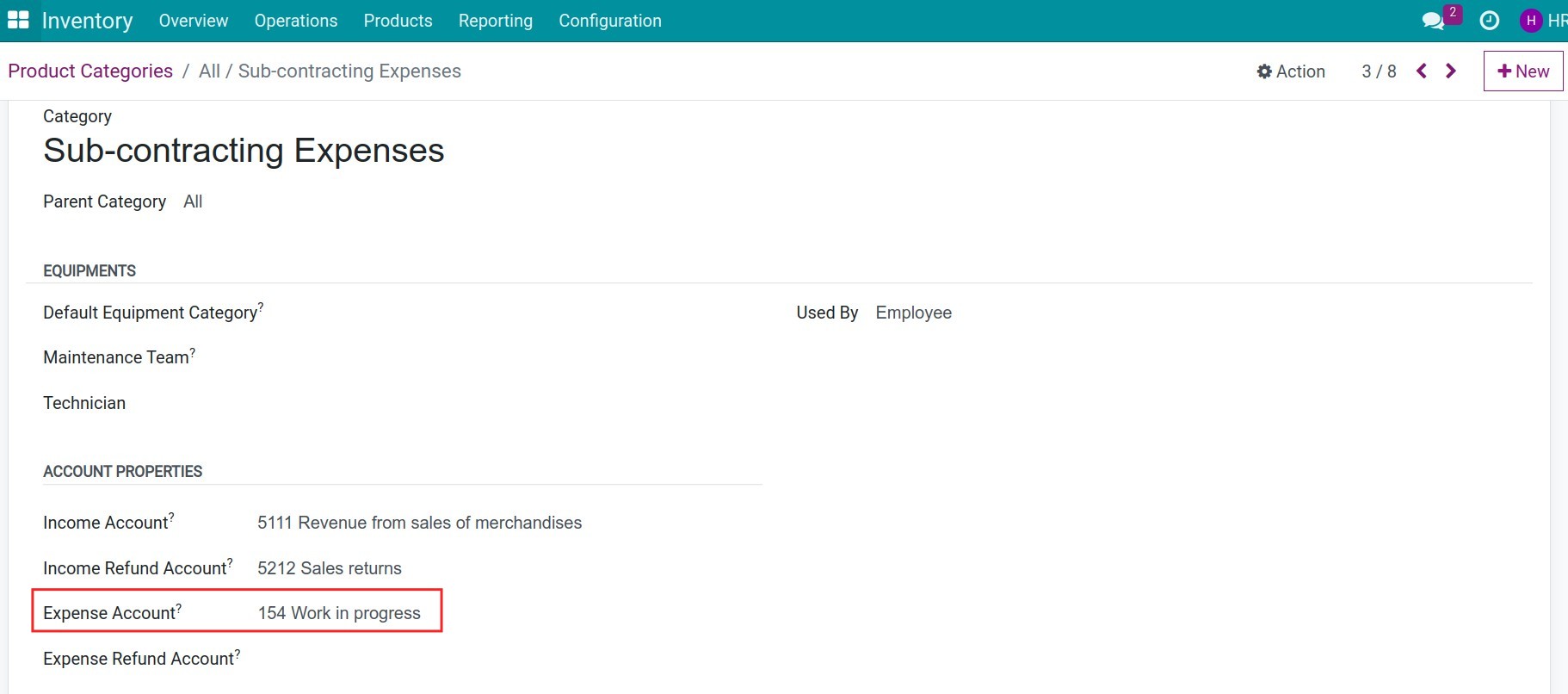
Otherwise, on the sub-contracting location:
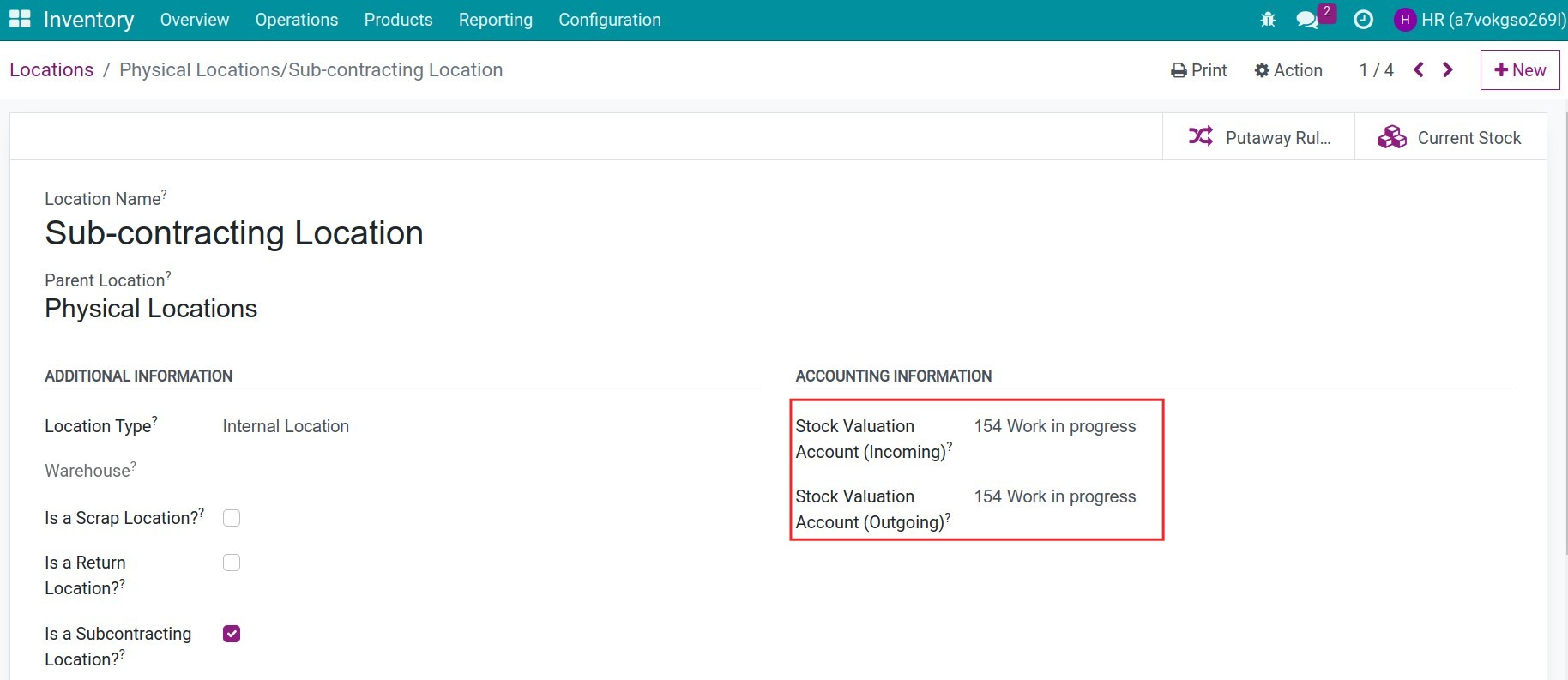
You can refer to the Introduction to Subcontracting in Viindoo article for the details of how to activate the Subcontracting feature.
See also
Sub-contracting accounting in Viindoo¶
When you create a quotation for the subcontracting order and confirm it, a resupply order is automatically generated to supply the raw materials to the sub-contractor and the receipt to receive the finished products from the sub-contractor. To run the sub-contracting process, you can refer to the article Manage subcontracts in the manufacturing process. By the way, in the sub-contracting order, you can add more the sub-contracting expenses as follow:
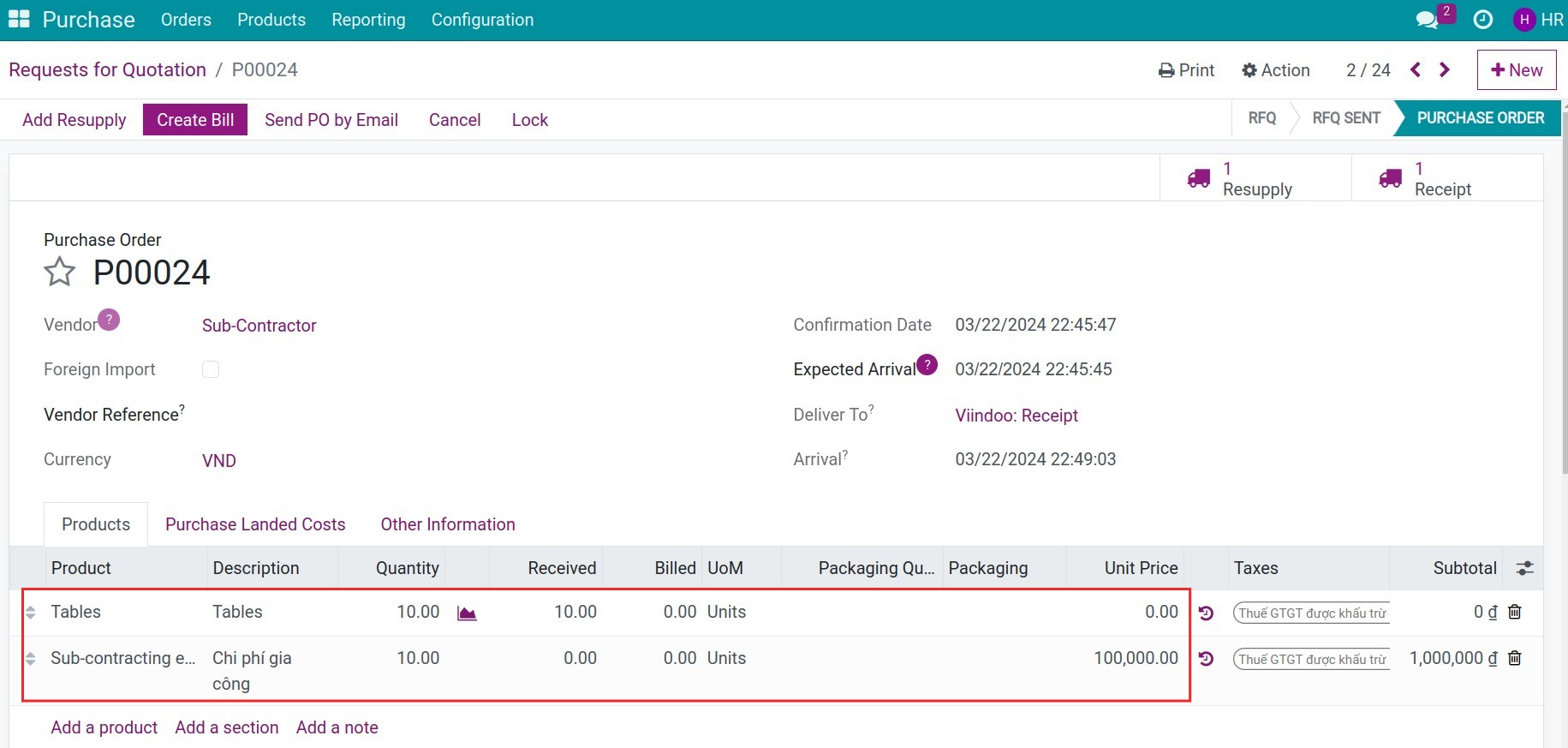
Delivery of the material components to the sub-contractors¶
Navigate to Purchase > Orders > Purchase Orders, use the filter to find the sub-contracting order. Then press to the Resupply button:
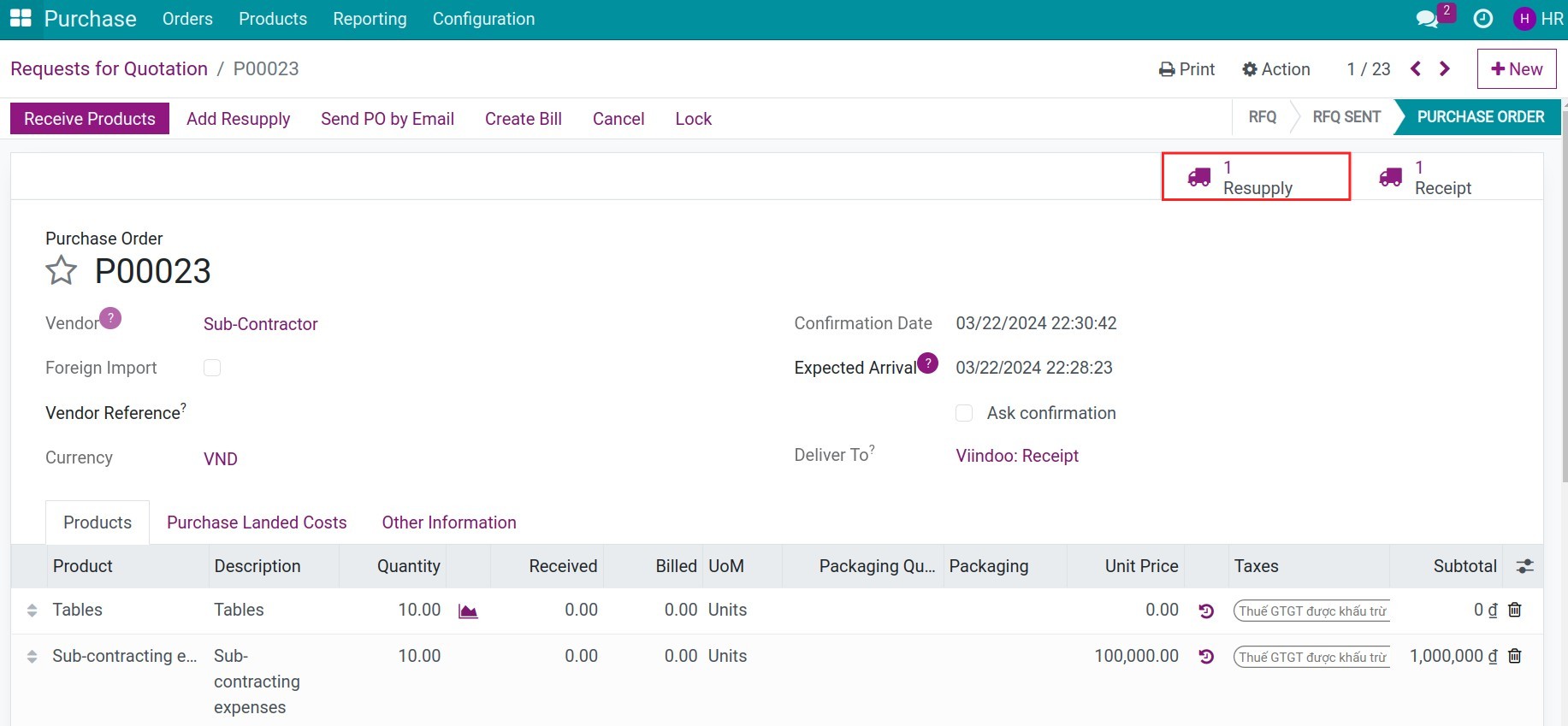
Once the resupply slip is confirmed, you can see the journal entries related to sending materials to sub-contractors.
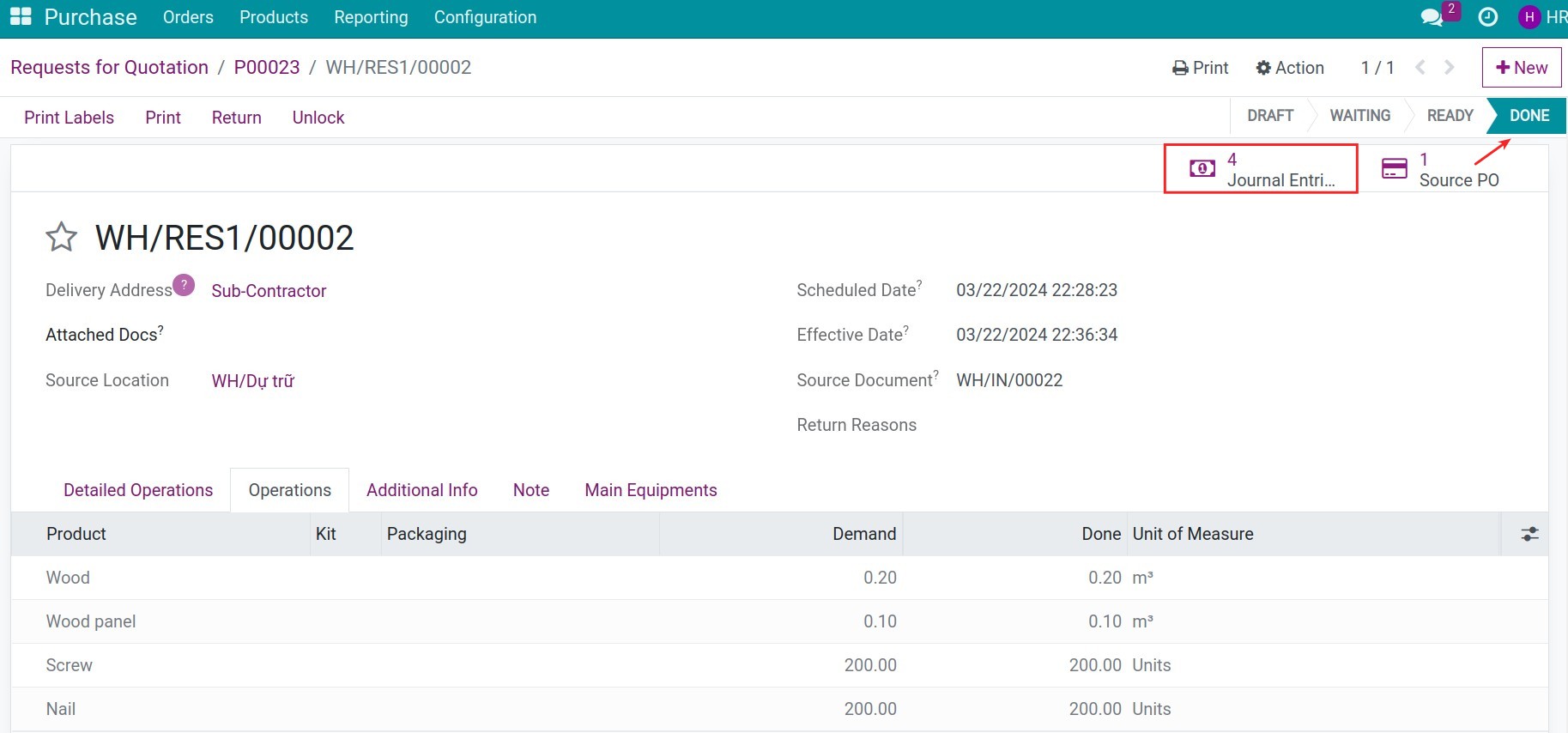
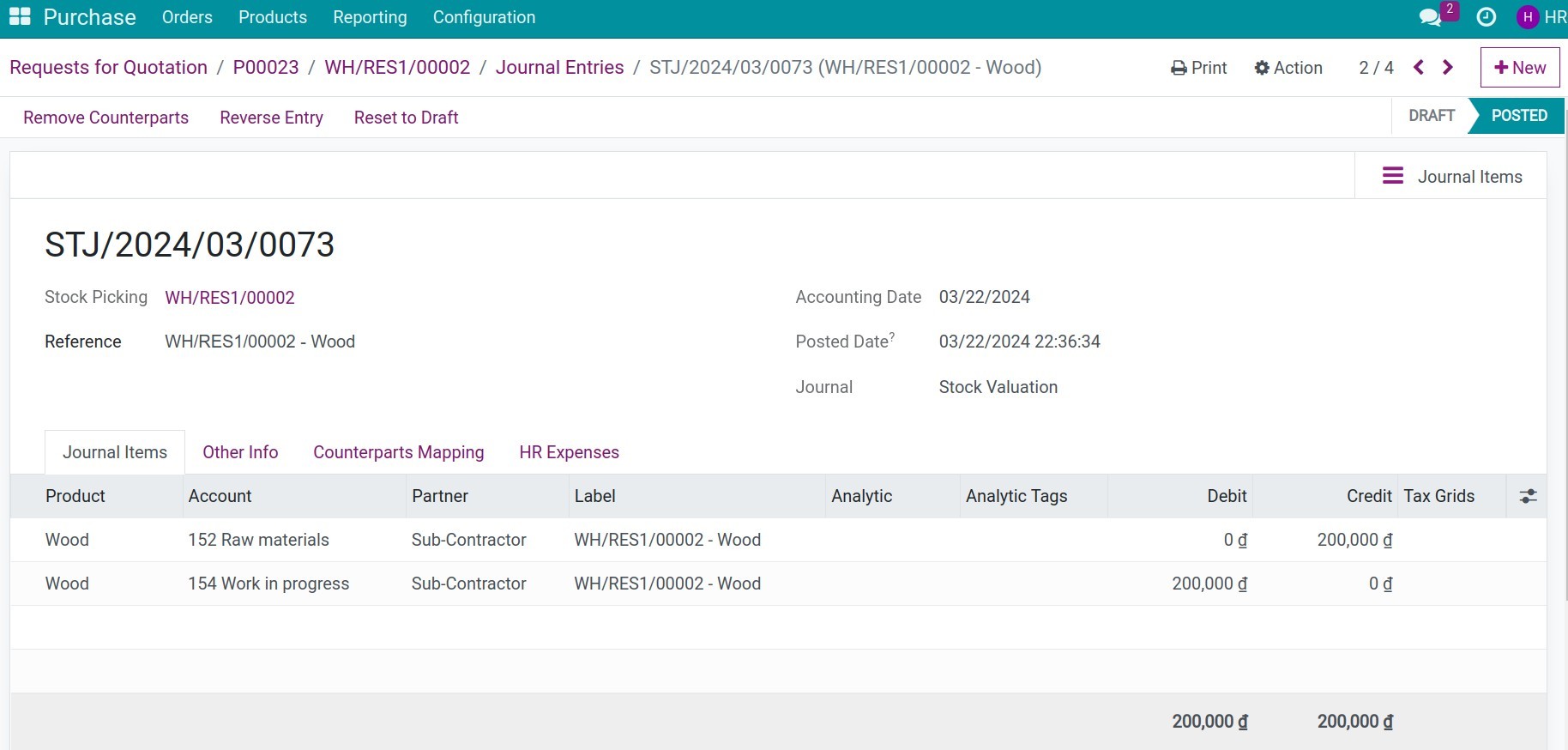
Receive the finished products from the sub-contractors¶
Once the processing is completed, navigate to Purchase > Orders > Purchase Orders, select the related purchase order then press to the Receipt button.
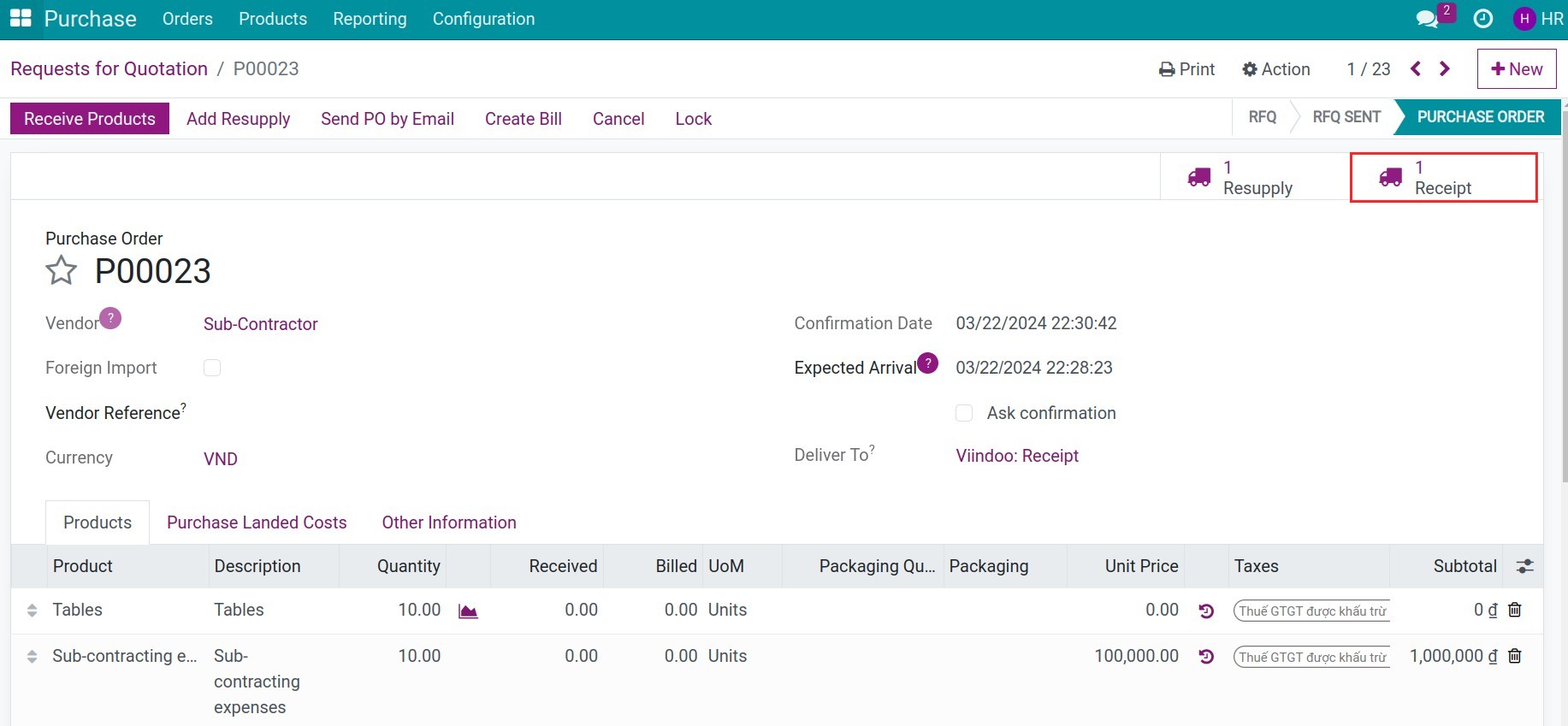
You need to record the consumption of components by pressing the Record components button and input the quantity of finished products that received. At that moment, the system will auto-calculate the corresponding quantities of components based on the bill of materials.
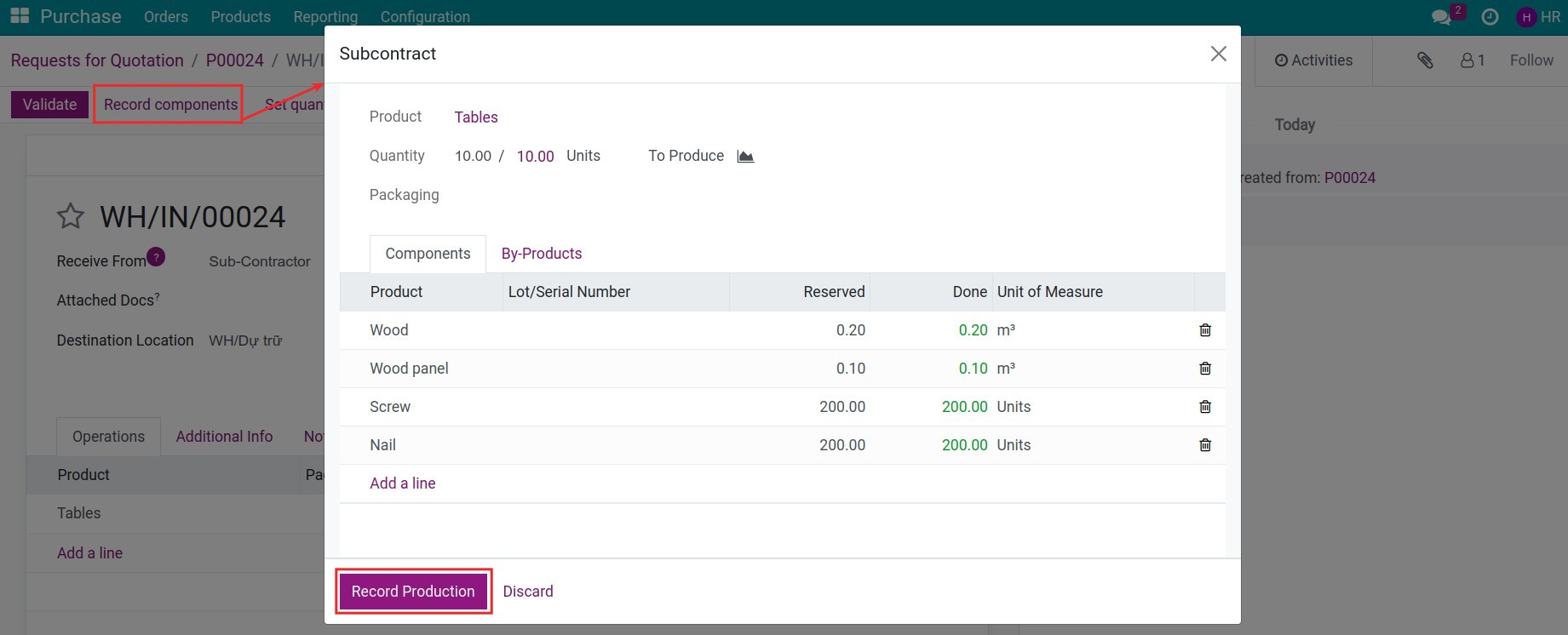
Once the receipt is validated, you can see the posted journal entry:
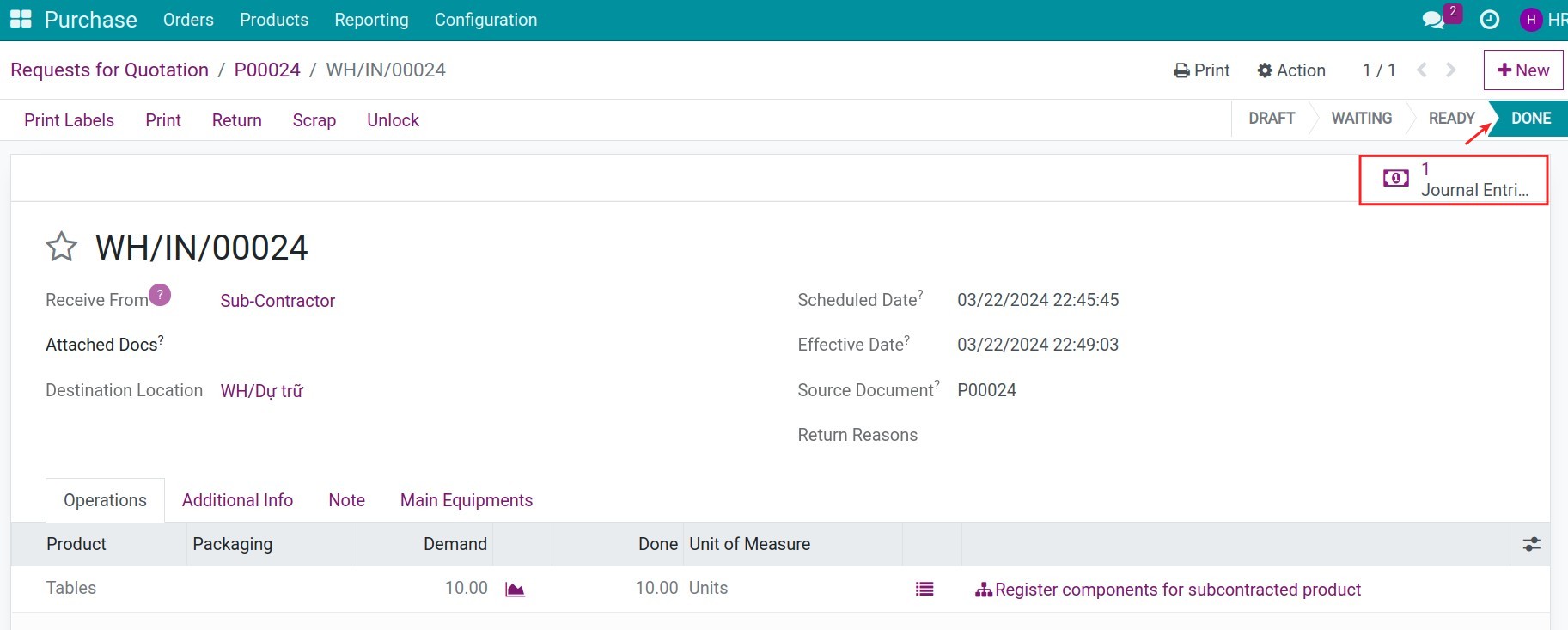
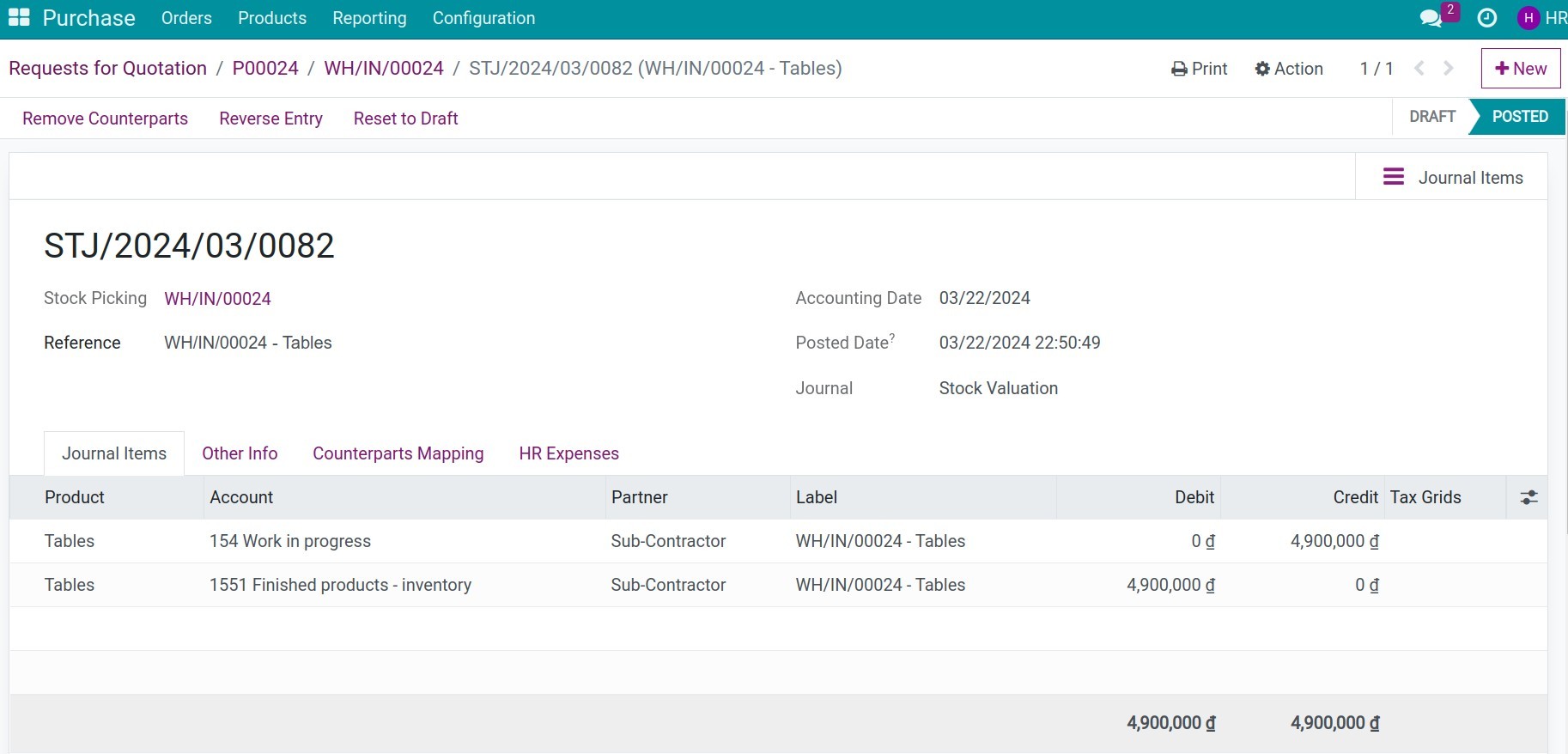
Recording the sub-contracting expenses¶
Back to the sub-contracting orders, you can create the bills to record the sub-contracting expenses and do the payment process. Press Create Bill.
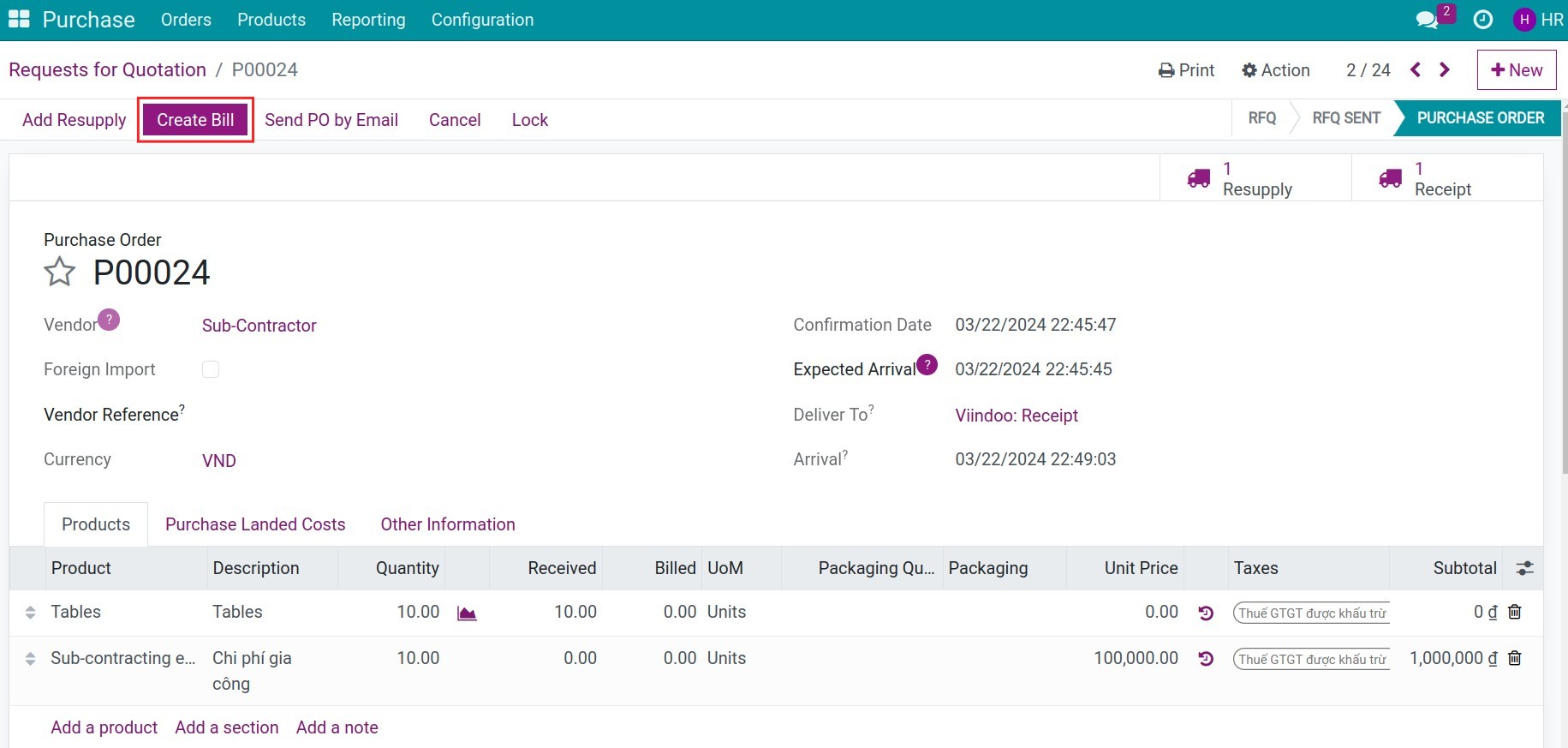
Once the bill is posted, you can see the journal entry of sub-contracting expenses.
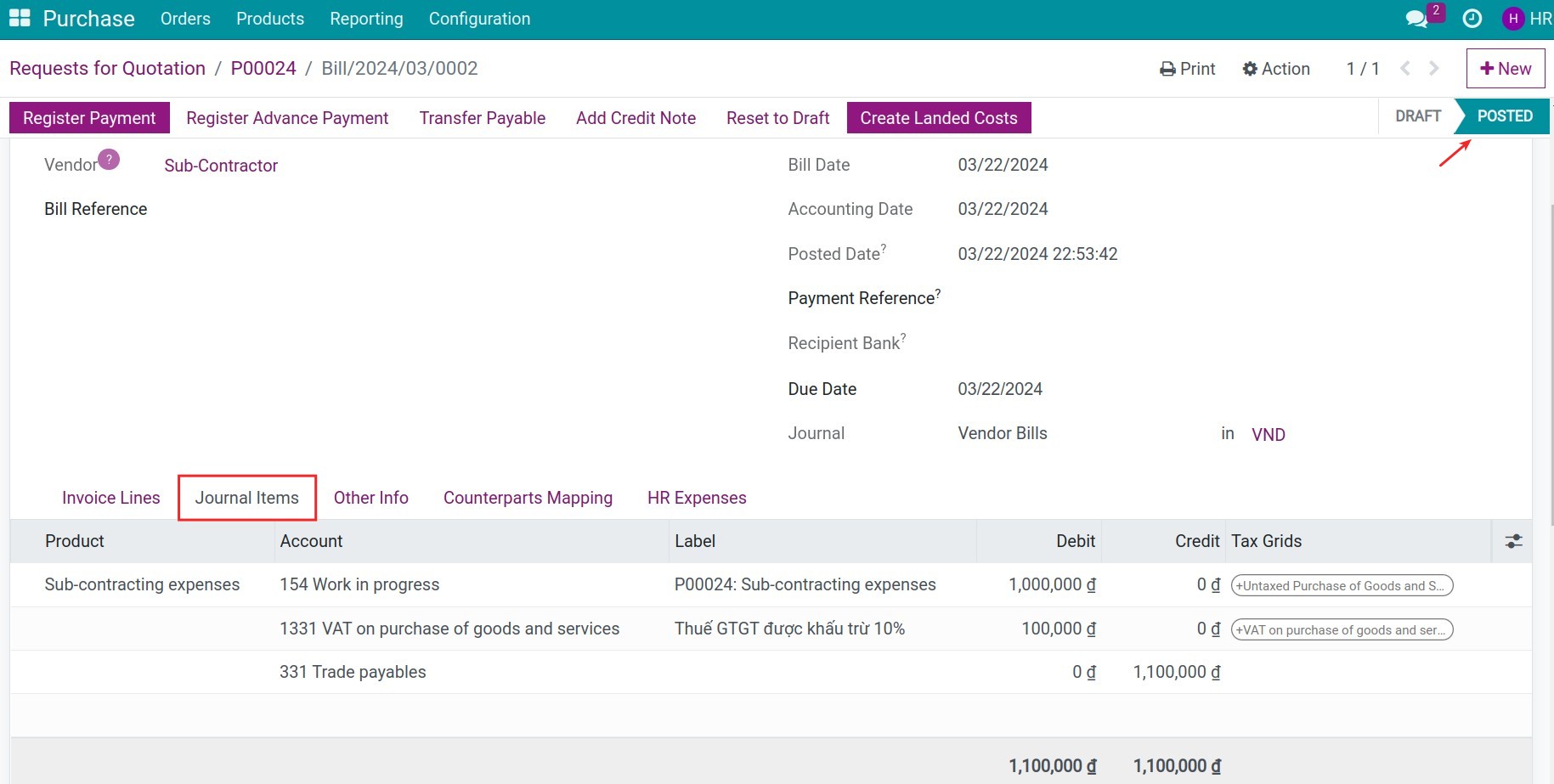
Allocating the sub-contracting expenses¶
To allocate the sub-contracting expenses to the sub-contracting orders, press Create Landed Costs on the bill interface.
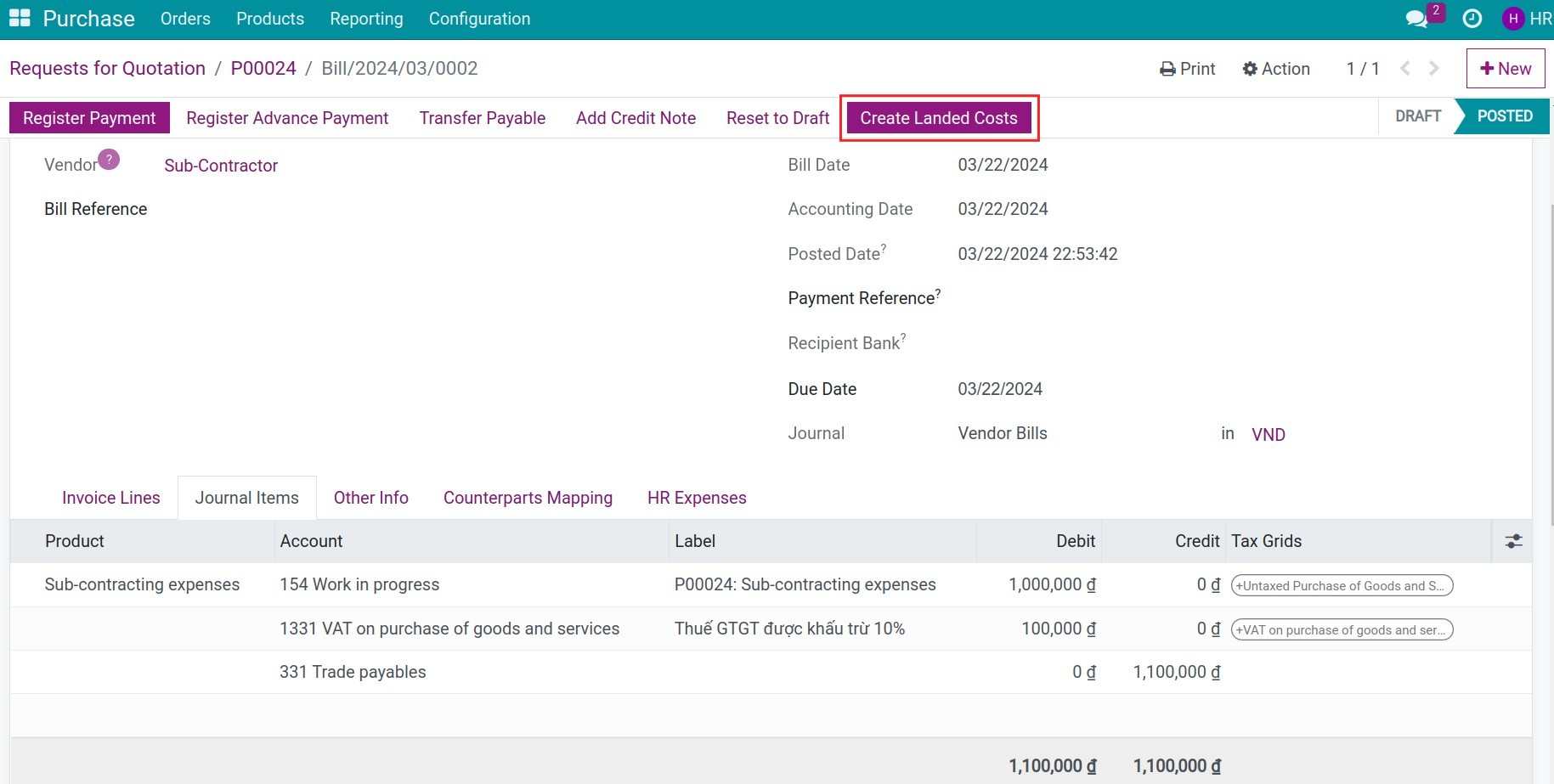
Validate this landed costs transaction, you can see the related journal entry:
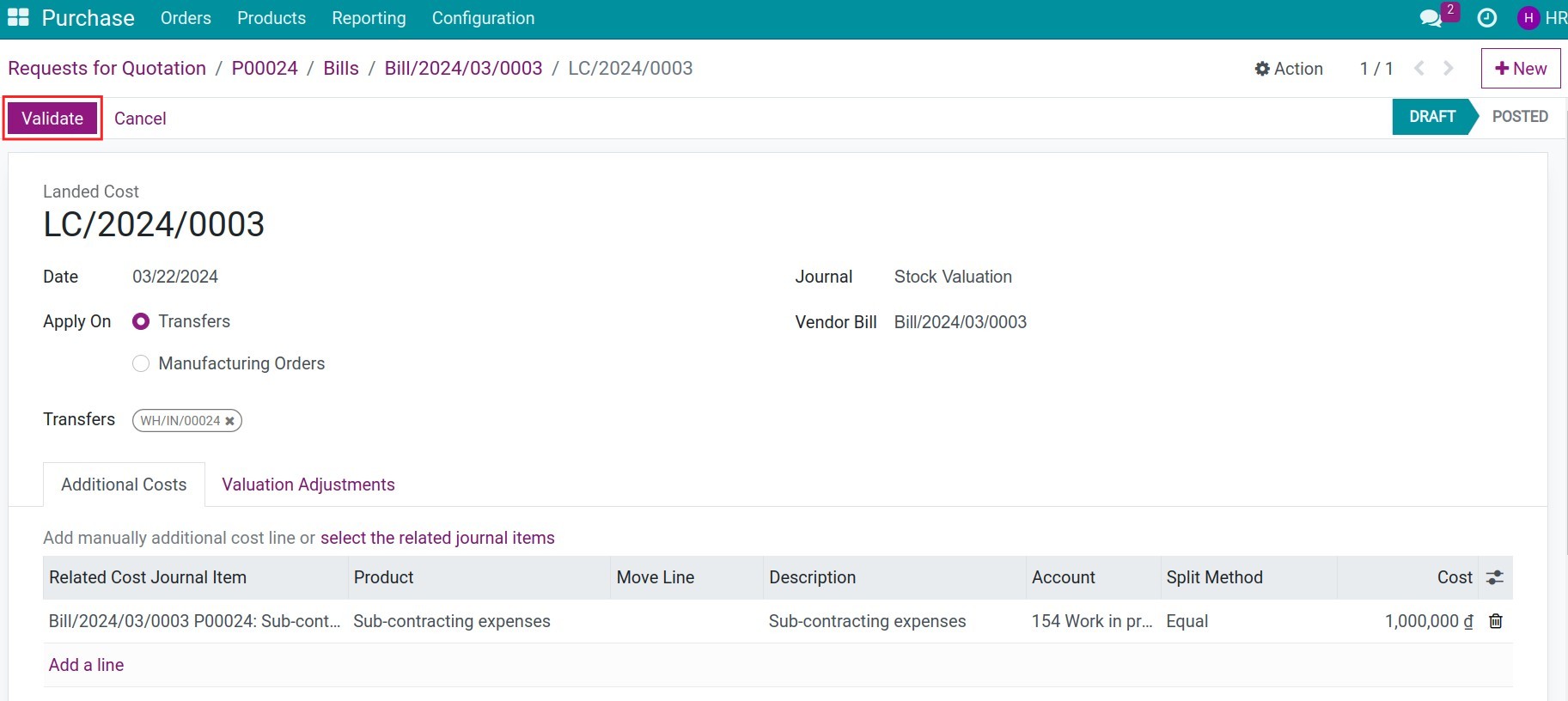
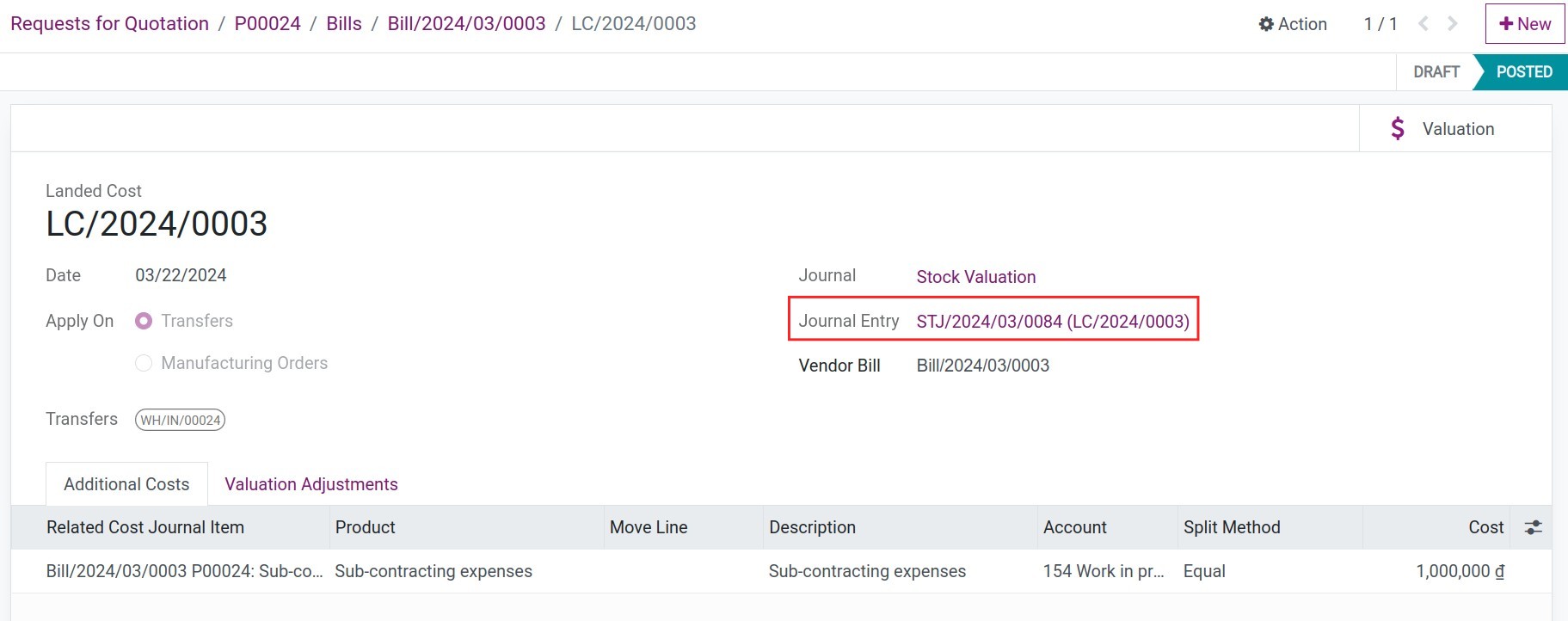
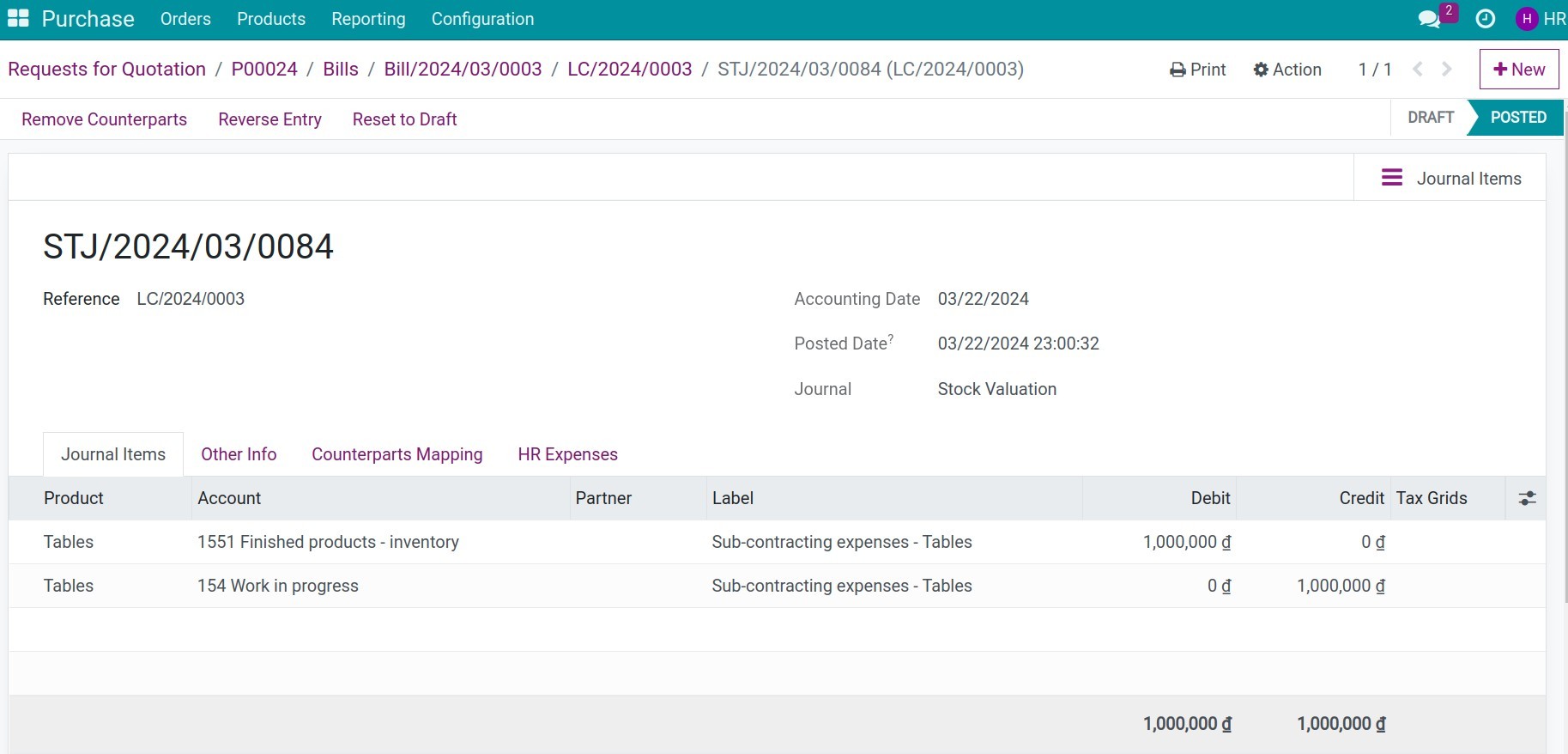
See also
Related article
Optional module