Accounting for Subcontracting Goods Valuation¶
Subcontract is a common activity in manufacturing enterprises. During this process, businesses will need to manage the outgoing raw materials sent to the subcontractors, and control and record data to track related costs. This article will guide you through the settings of accounting accounts that record the entries of Subcontracting activities.
Requirements
This tutorial requires the installation of the following applications/modules:
Configure accounting accounts for a processed product category¶
Example: A business manufactures office desks. The business hires a subcontractor for the painting process of table legs, the semi-finished products received from this subcontracting process are painted table legs, which will be used in the next stage of the manufacturing operation.
You can refer to the Introduction to Subcontracting in Viindoo article for the details of how to activate the Subcontracting feature, configure the bills of materials (BoM) for each stage related to finished products, semi-finished products, raw materials for the subcontracting work.
The configuration for accounting accounts of the semi-finished products category is shown below:
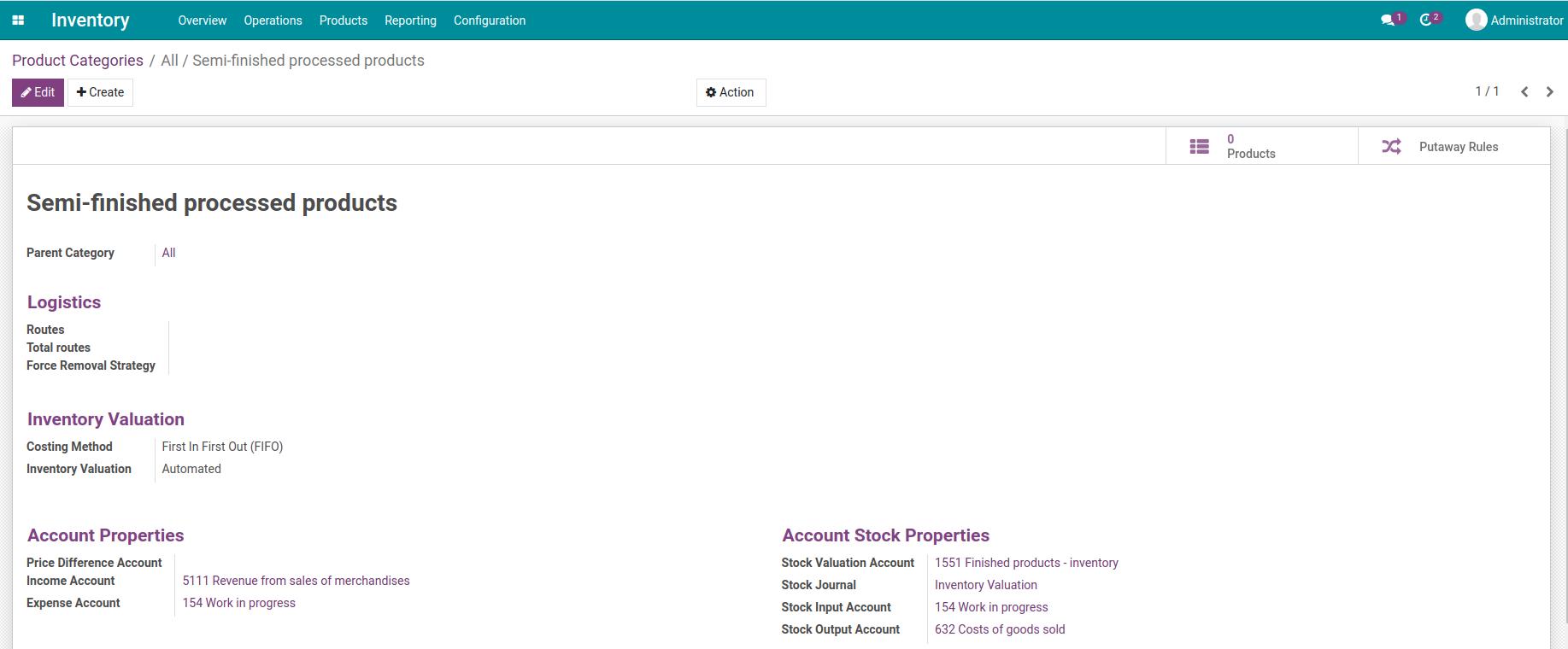
Expense Account: 154 Work in process expense.
Stock Valuation Account: 1551 Finished products - inventory.
Stock Input Account: 154 Work in process expense.
Stock Output Account: 632 Costs of goods sold.
See also
Automatically created journal items in subcontracting activities¶
To understand how the system automatically records journal items, let’s have a look at an example of the manufacture of semi-finished products and transferring them to the subcontractor, which includes the two following steps:
Step 1: Produce semi-products including table legs and tabletops;
Step 2: Subcontracted painting of table leg to have a painted table leg.
Step 1: Produce semi-finished products¶
Please refer to Step 1: Manufacturing the semi-finished product article for more details about semi-finished products production.
After completing the production, navigate to Accounting > Accounting > Journal Entries and use the Reference contains + reference of the manufacturing order filter. See more details: Filter, Groups and Search use cases.
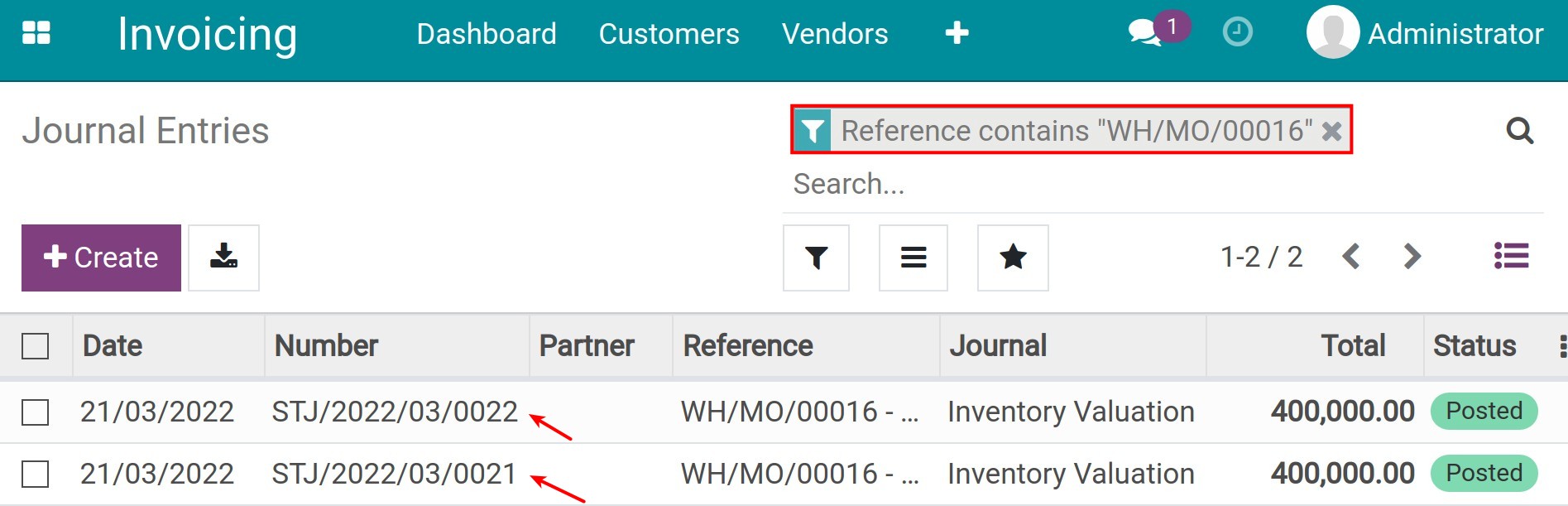
Journal entries related to a manufacturing order include:
Sending materials to production.
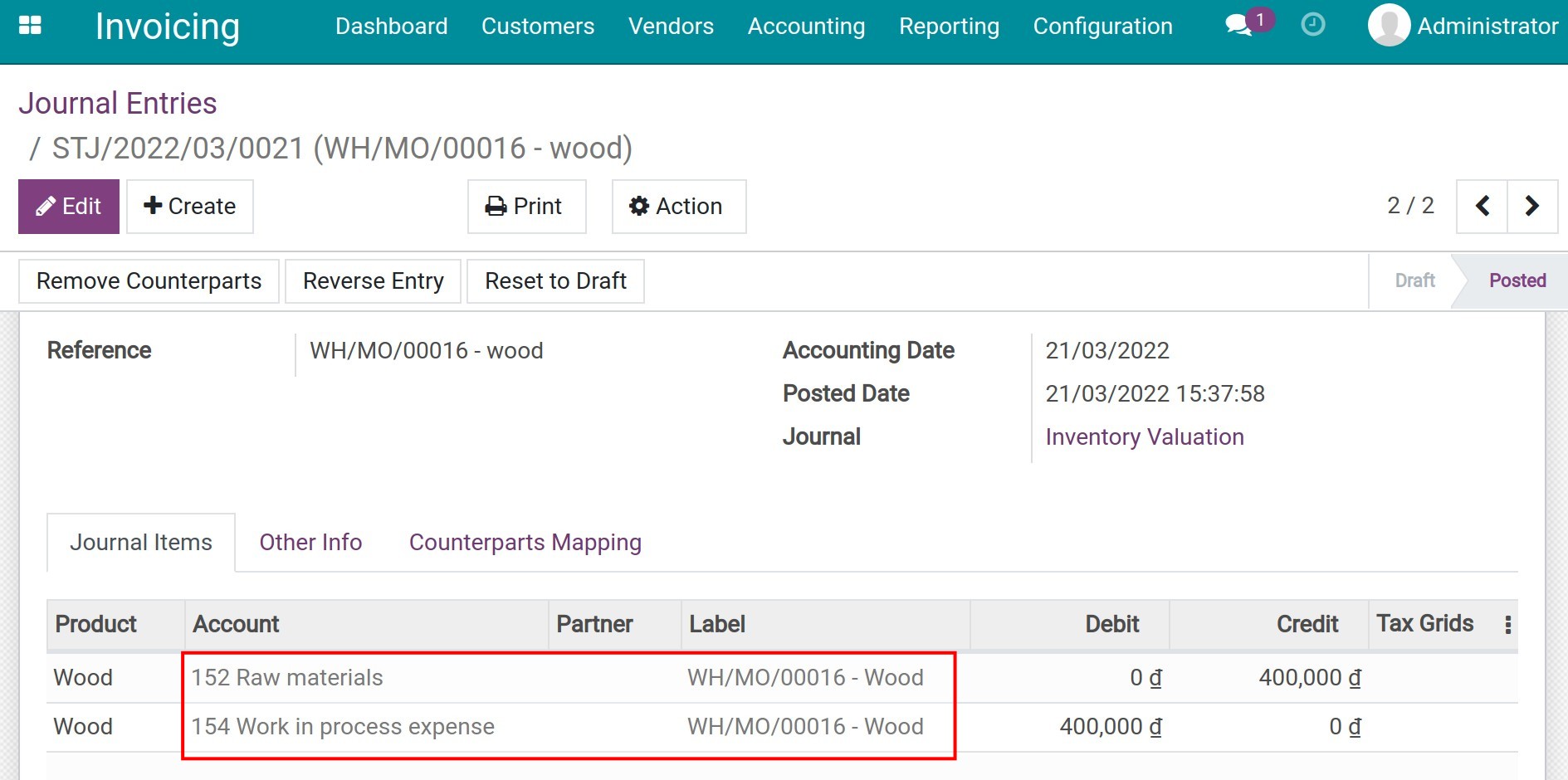
Receiving semi-finished products in the warehouse.
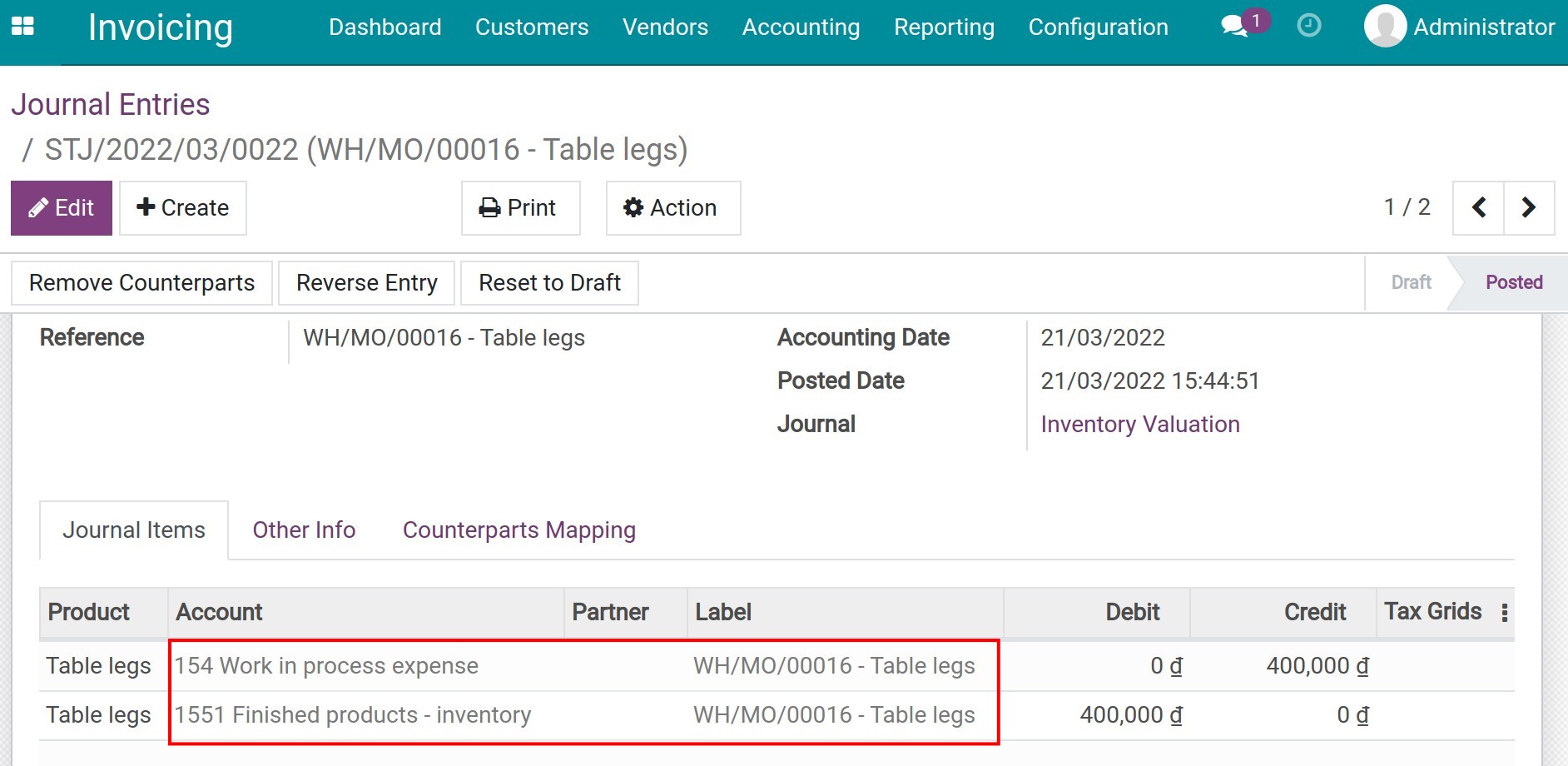
Step 2: Subcontracting¶
When you create a quotation for the subcontracting order and confirm it, a delivery order is automatically generated to supply the raw materials to the subcontractor. When the inventory of raw material to be delivered is sufficient, the delivery order status will be changed from Waiting to Ready and you can select Validate to confirm the completion of this delivery. Journal entries are not created because the processing location is internal.
For more information, please refer to Step 2: Subcontracting article.
Once the processing is completed, navigate to Purchase > Orders > Purchase Orders, select the related purchase order then check the receipt created after the purchase confirmation. Press Validate to confirm the receipt of painted table legs from the subcontractor. Navigate to Accounting > Accounting > Journal Entries by using the Reference contains + reference of the manufacturing order filter.
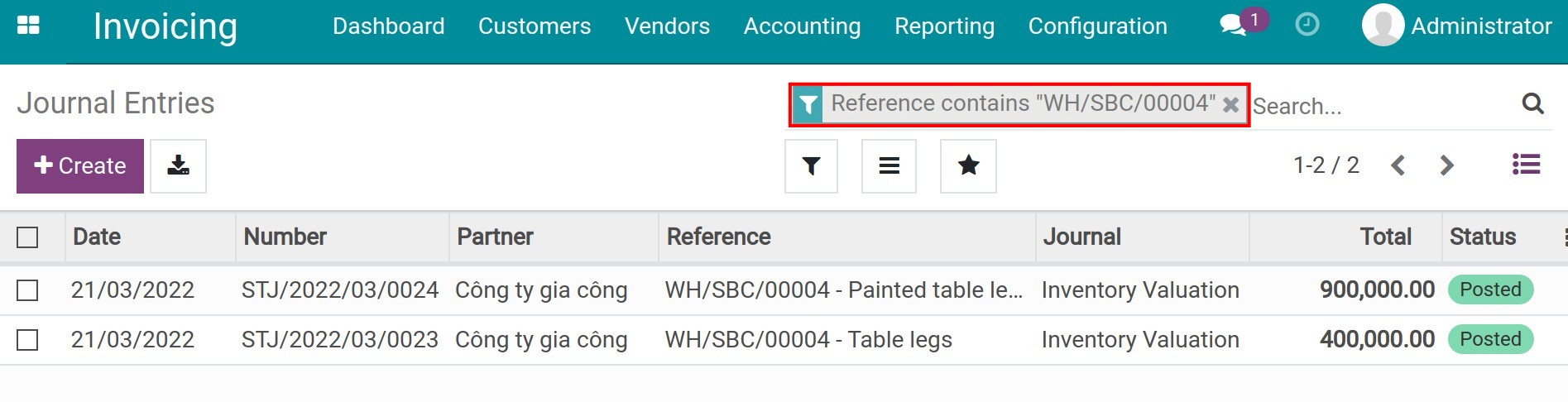
Journal entries related to sending semi-finished products to the subcontractor and receiving processed semi-finished products are:
Sending semi-finished products to the subcontractor.
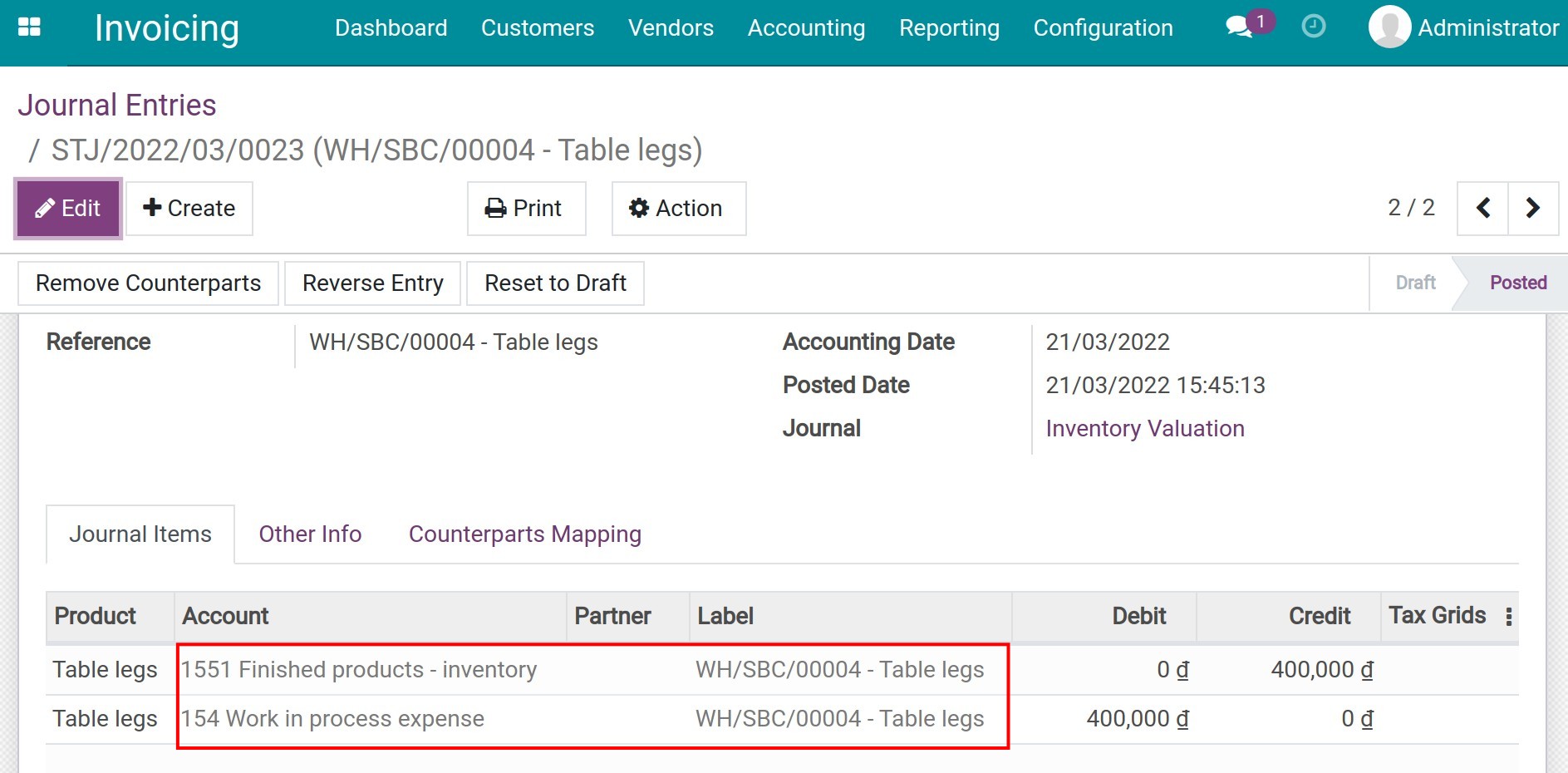
Receiving semi-finished products in the warehouse.
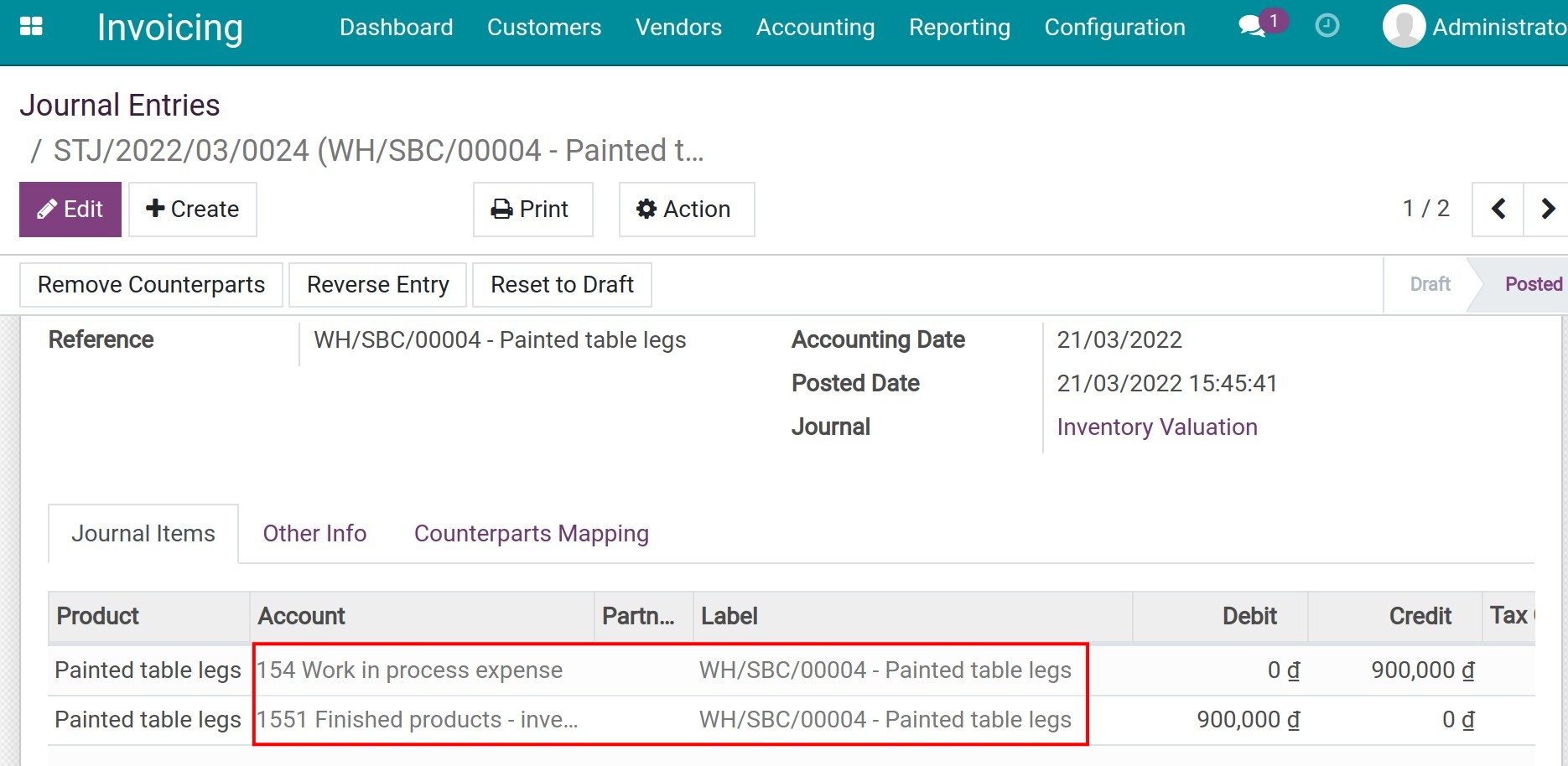
The system records journal entries generated from the subcontracting process. You can read further about the subcontracting process in other articles.
See also
Related article
Optional module