How to Integrate Quality Control with Transfers¶
The integration of Quality and Inventory apps helps you to create quality control points in-stock operations such as the receipt, delivery, and transfer of goods in purchasing, selling, and rotation activities or during storage time.
Requirements
This tutorial requires the installation of the following applications/modules:
To use this feature, go to Apps, remove Apps filter, search and install Stock Quality Control module:
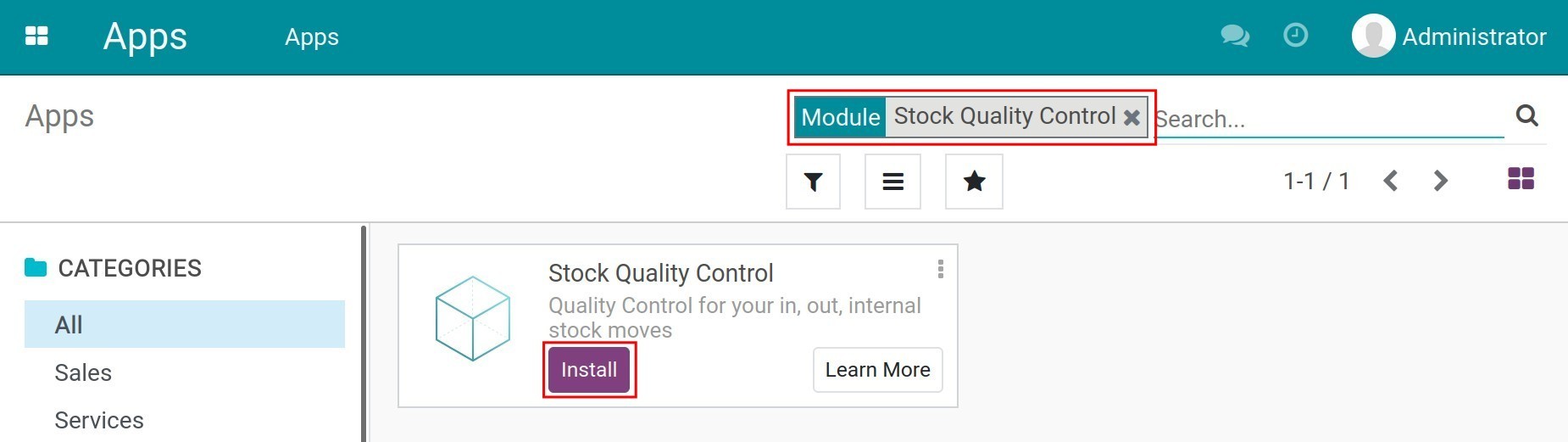
Create quality control points for inventory operations¶
Navigate to
and click on Create to provide criteria for the control.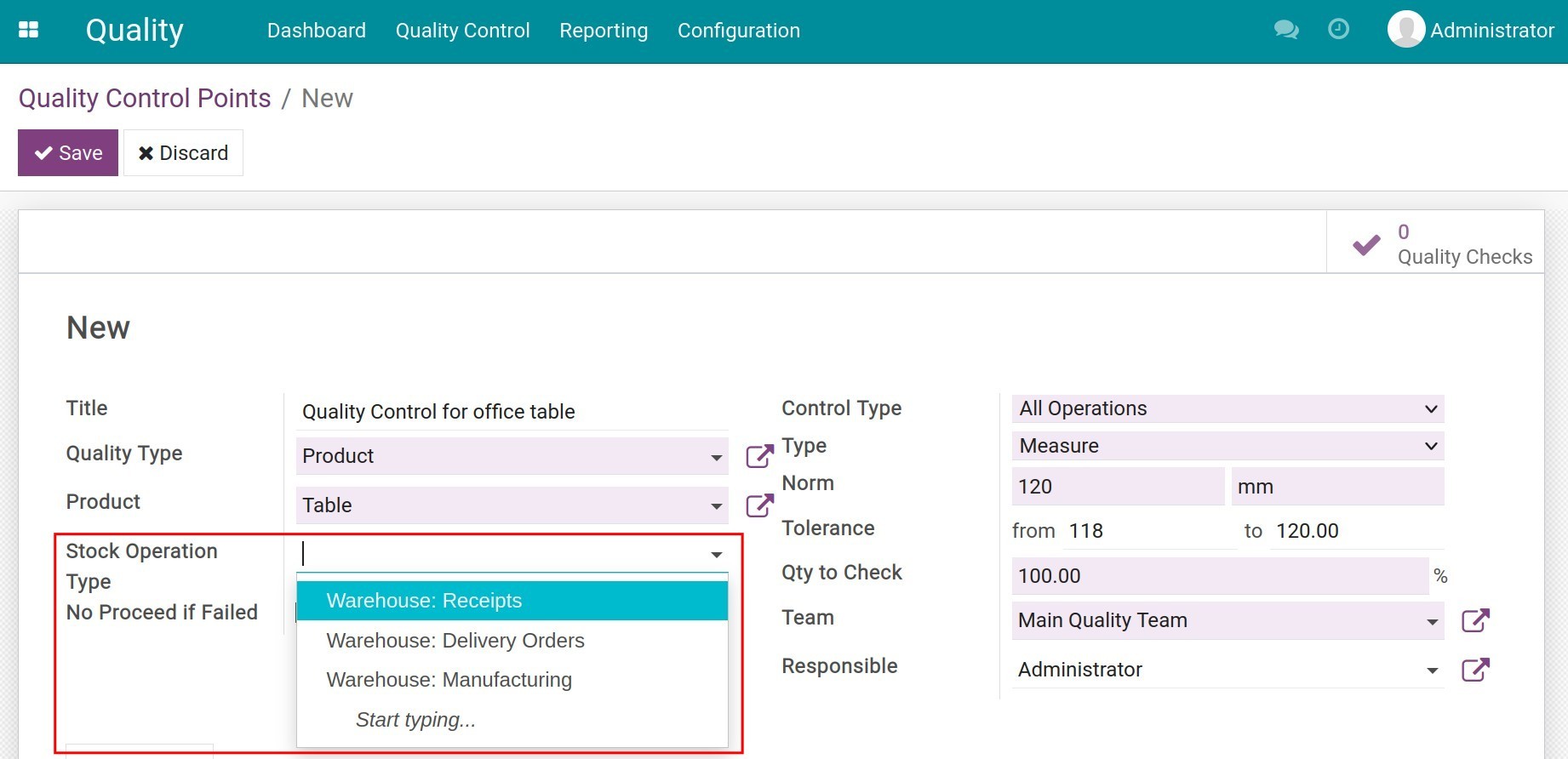
You can define product quality control points depending on the needs of stock operations in the following fields:
Title: Name the quality control point.
Quality Type: Choose Product.
Product: Select the product that needs to be checked.
Stock Operation Type:
Receipts: Used for product quality control activities when goods are received from vendors.
Delivery: Used for product quality control activities before goods are delivered to customers.
Internal Transfer: Used for product quality control activities when goods are transferred between locations in your company. This option only shows when you activate Storage Locations.
No Proceed If Failed: If you check this box, the goods will be blocked when they fail the quality control point.
Control Type:
All Operations: 100% of the products at the selected stock operation must be quality checked.
Randomly: Quality checks randomly according to the percentage of goods. The goods will pass this quality control point if they meet the specified control frequency.
Periodically: Can be used for inventory control activities to ensure the quality of goods with a long inventory age.
Type:
Pass - Fail: The quality experts evaluate the goods as pass or fail.
Measure: Used for measurable criteria such as size, length, width, volume…allowing a certain tolerance ratio.
Team: The quality control team.
Responsible: The user in charge of the quality control point.
Click Save to save information.
The practical example¶
Your company buys 10 desks with measurements of 120mm, before stocking, they must be quality and size checked properly.
Following these steps below:
Step 1: Create the quality control point. In that quality control point, you need to note the following fields:
Stock Operation Type: Receipts;
Type: Measure;
Norm: 120 mm;
Tolerance: 118 - 120 mm.
Based on this control point, you can allow the product to be stocked or not.
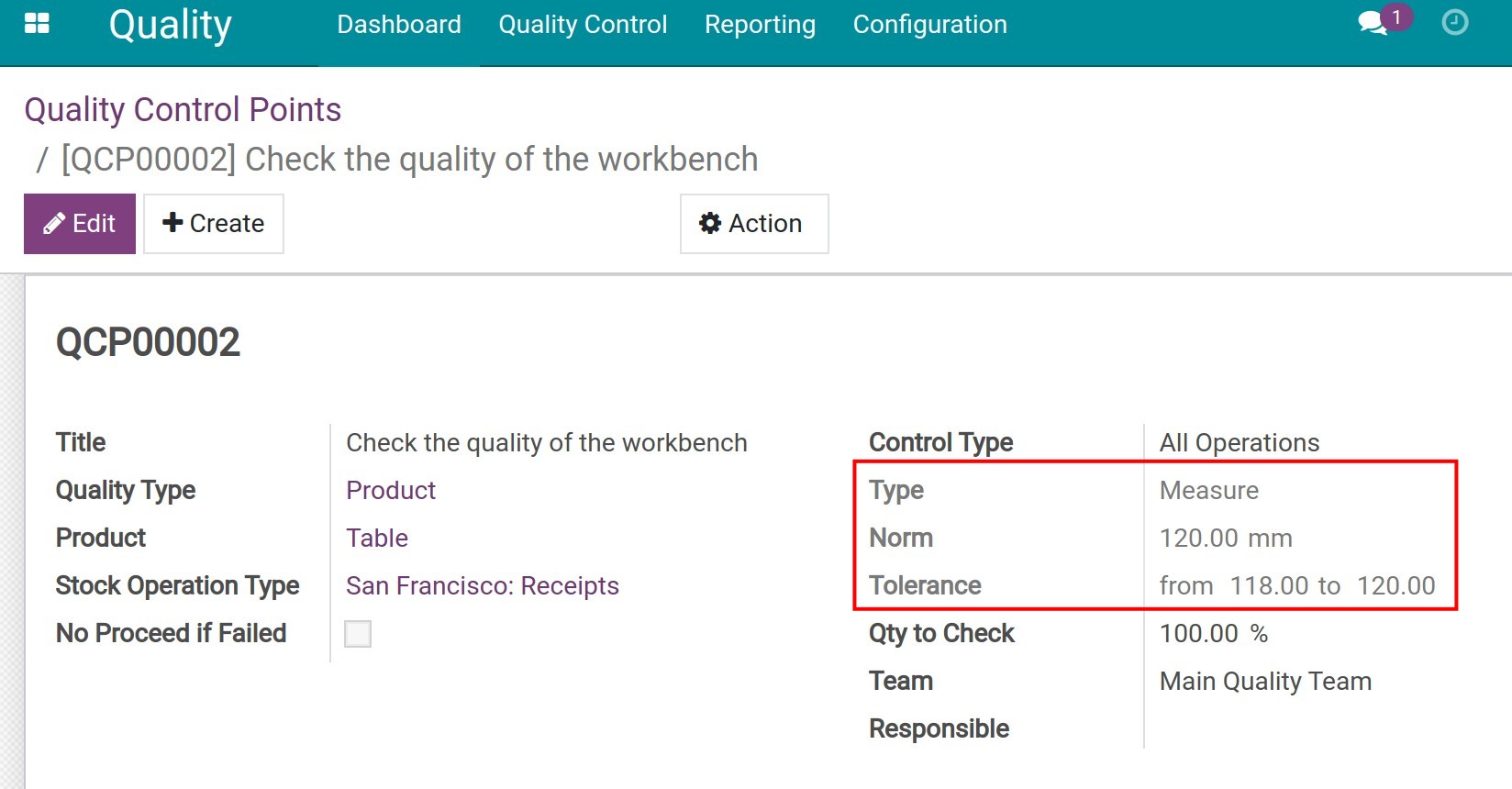
Step 2: Create a purchase order, check the quality and stock the desks.
After creating and confirming the Purchase Order, click on Receive Products.
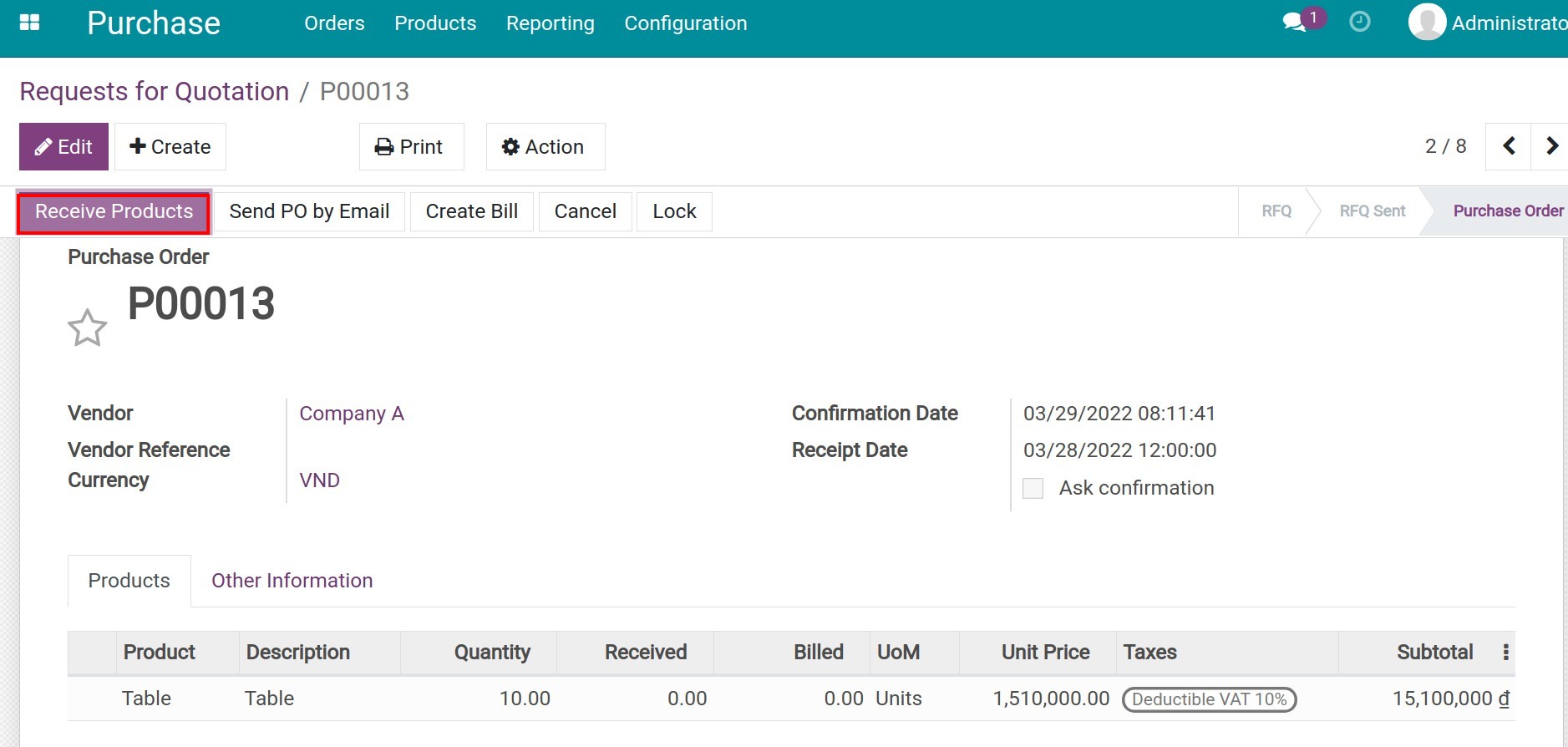
The system will move to the warehouse receipt order interface. This receipt order will be in Ready state. You click on Quality Checks to control input quality before acceptance.
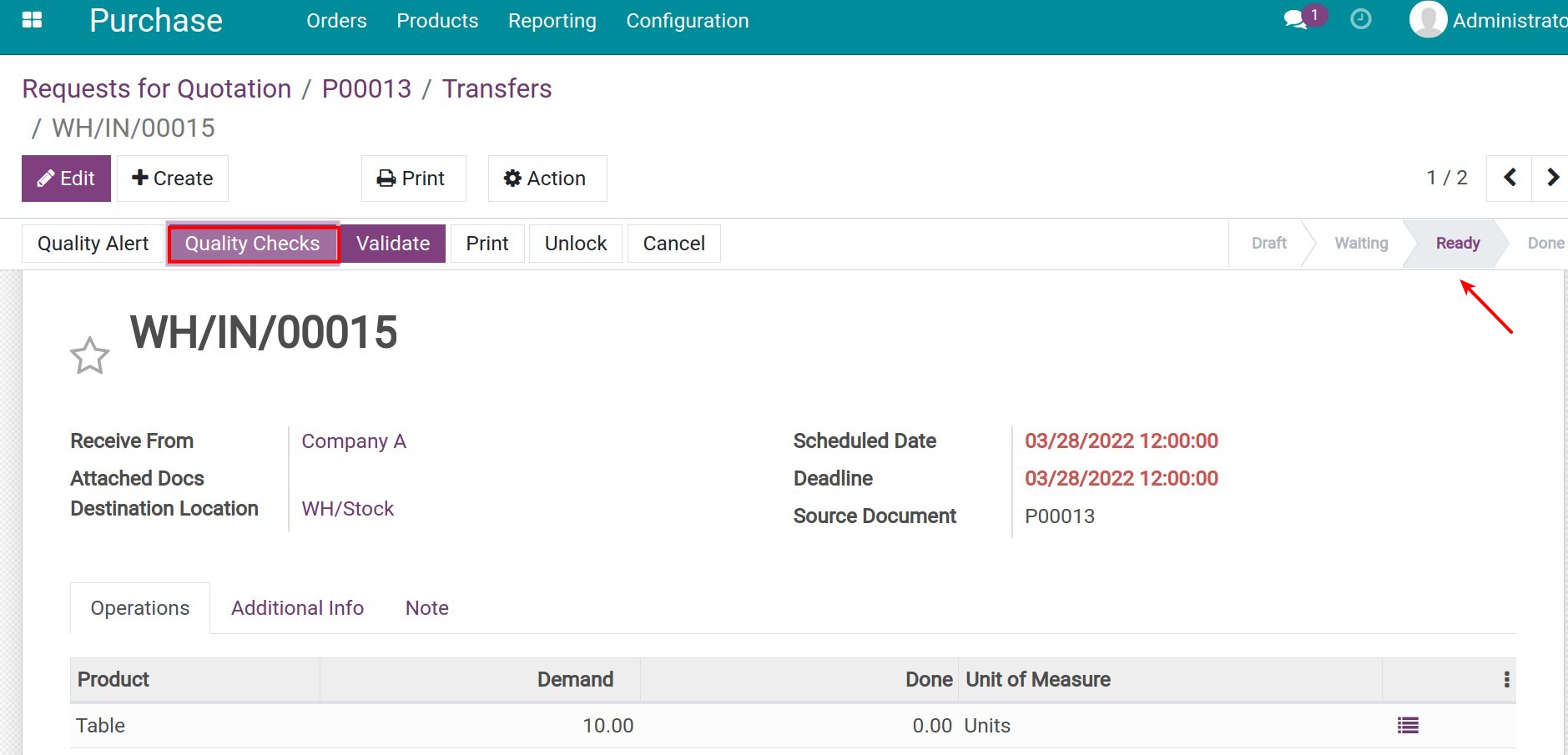
The quality check view will be displayed, you manually enter the product’s measurement in Measure field in millimeters. Here are two situations that may occur:
Situation 1: The measurement is out of the allowable tolerance range.
By clicking on Validate, the system will display a warning panel Quality Check Failed, you can choose Correct Measure to update new data or click Confirm Measure to mark a failure for the quality check in here.
In this case, you need to create the quality alert.
Situation 2: The measurement is in the allowable tolerance range.
The operation is similar to the above situation. After confirming, select Quality Checks, and you will see the status of the quality checks as Passed.![]()
See also
Related articles
Optional modules