Apply Make to Stock for Production on Order in Viindoo¶
In Viindoo, the Make to Order (MTO) strategy allows production or purchase orders to be generated as soon as a sales order is confirmed. However, a major limitation of MTO is that it ignores existing stock levels, the system will always create a manufacturing or purchase order for the full quantity required, even if part of it is already in stock. To address this issue, you can apply the Make to Stock (MTS) strategy with a special configuration of reordering rule follow this article’s guidance.
This is a hybird approach, ideal for production enviroments where manufacturing orders are demand-driven but partial inventory often exists.
Requirements
This tutorial requires the installation of the following applications/modules:
Initial configuration¶
The special rules is 0/0/1 rule for reordering rule. To create a new reordering rule, navigate to Inventory ‣ Configuration ‣ Reordering Rules, then click New, and fill out the following fields for the new reordering rule line item:
Min: Enter 0. When forecasted stock falls below 0, a replenishment order for the product is created.
Max: Enter 0.
Multiple Quantity: Enter 1.
The 0/0/1 reordering rule is a specialized configuration used to replenish a product not typically in stock. When a sales order (SO) is confirmed, this rule is trigger to generate procurement only for the shortfall between the ordered quantity and the available stock. In the other words, the system prioritizes using the on-hand first, and only creates a replenishment for the exact quantity needed to fulfill the remaining demand.
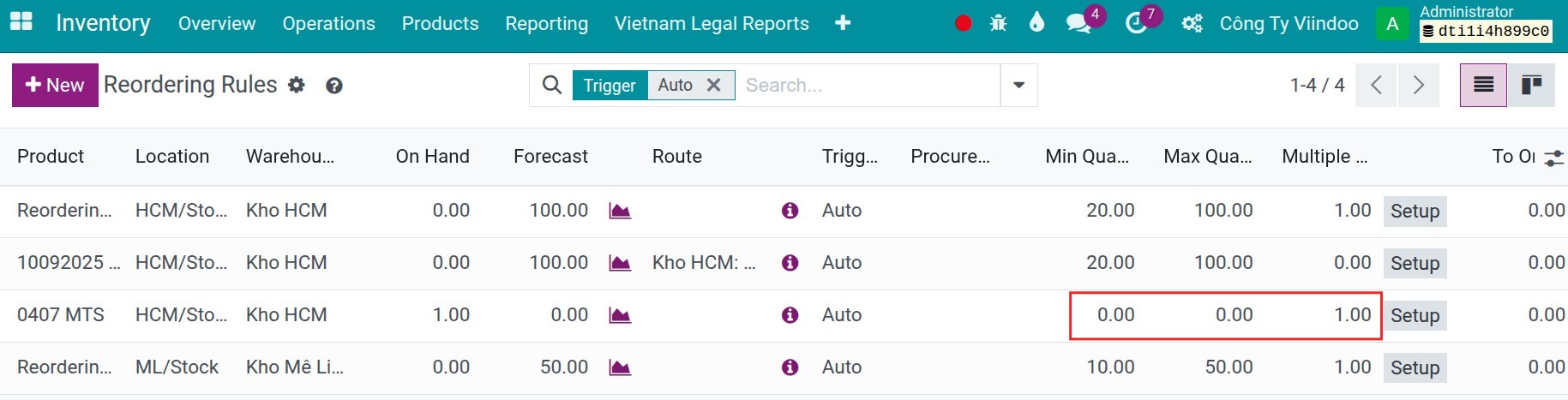
One key configuration in the reordering rule is the Procurement Group. By default, the Procurement Group field on the reordering rule is left empty. As a result, when multiple Sales Orders (SOs) are confirmed, the system will consolidate the demand into a single Manufacturing Order (MO) (The MO is not in Done status). This approach is particularly useful for products that can be produced in batches, allowing you to optimize production costs.
However, if you want to maintain traceability between SOs and MOs, or when different orders require separate handling, you need to assign a specific Procurement Group in the reordering rule. So that, each Sales Order will trigger a separate and corresponding Manufacturing Order. You can do this by entering a name directly into the Procurement Group field and selecting Create to generate a new group.
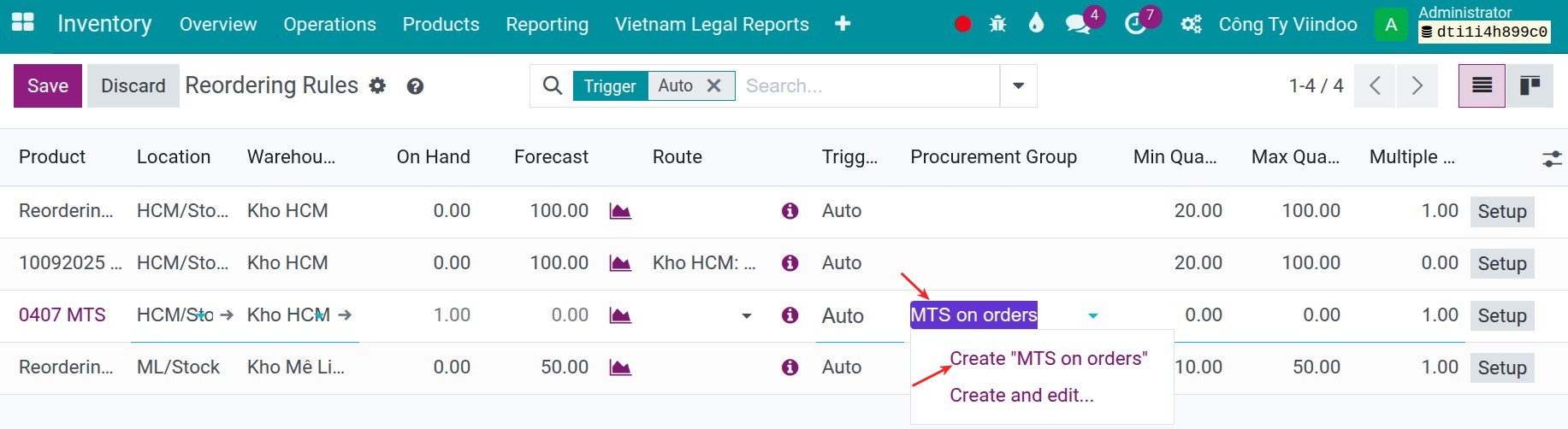
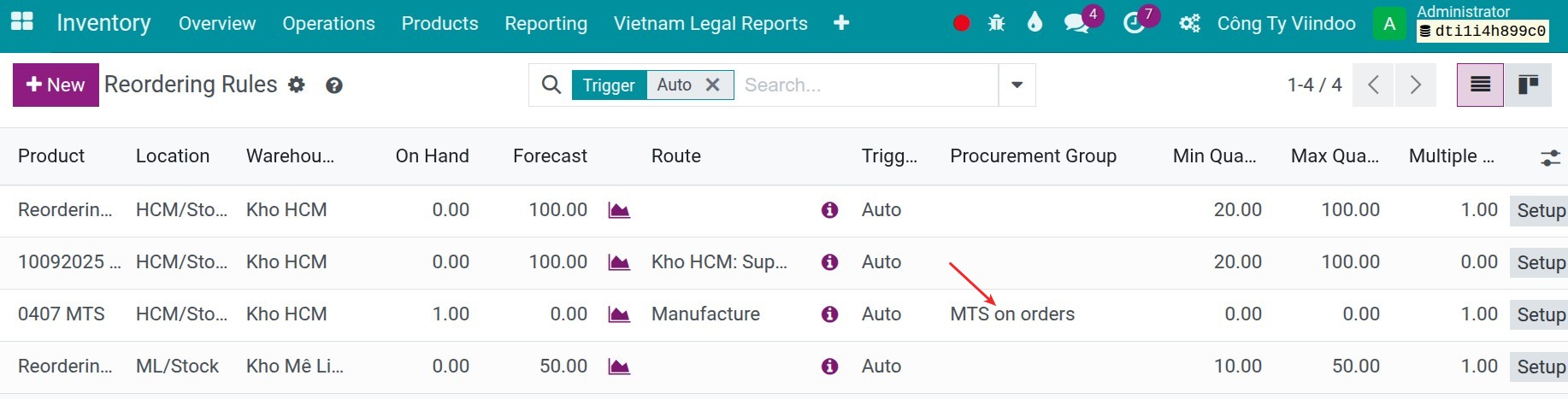
Replenishment performance¶
Warning
Both the 0/0/1 reordering rule and the Replenish on Order (MTO) route are designed to trigger procurement or production immediately upon Sales Order (SO) confirmation.
However, the two approaches behave differently in terms of stock reservation and order traceability:
Stock Reservation: The MTO route automatically reserves the replenished product specifically for the SO that triggered it. This ensures that the item cannot be allocated to any other order. In contrast, the 0/0/1 reordering rule does not apply such a reservation. Products produced or purchased through this rule are added to general stock and can be used to fulfill any SO.
Sales Order Traceability: When using MTO, each replenishment order is directly linked to the originating SO. You’ll see a smart button on the SO form that lets you trace back to the related Manufacturing or Purchase Order. On the other hand, with the 0/0/1 rule, no such linkage is created. The system still triggers a replenishment order, but it won’t automatically show any reference back to the SO that caused it.
Replenishment without procurement group configuration¶
Example behavior:
Product has reordering rule 0/0/1.
A Sales Order 1 is confirmed for 100 units.
A Sales Order 2 is confirmed for 200 units.
There are 30 units available in stock.
Expect: The system will generate a procurement for 270 units only.
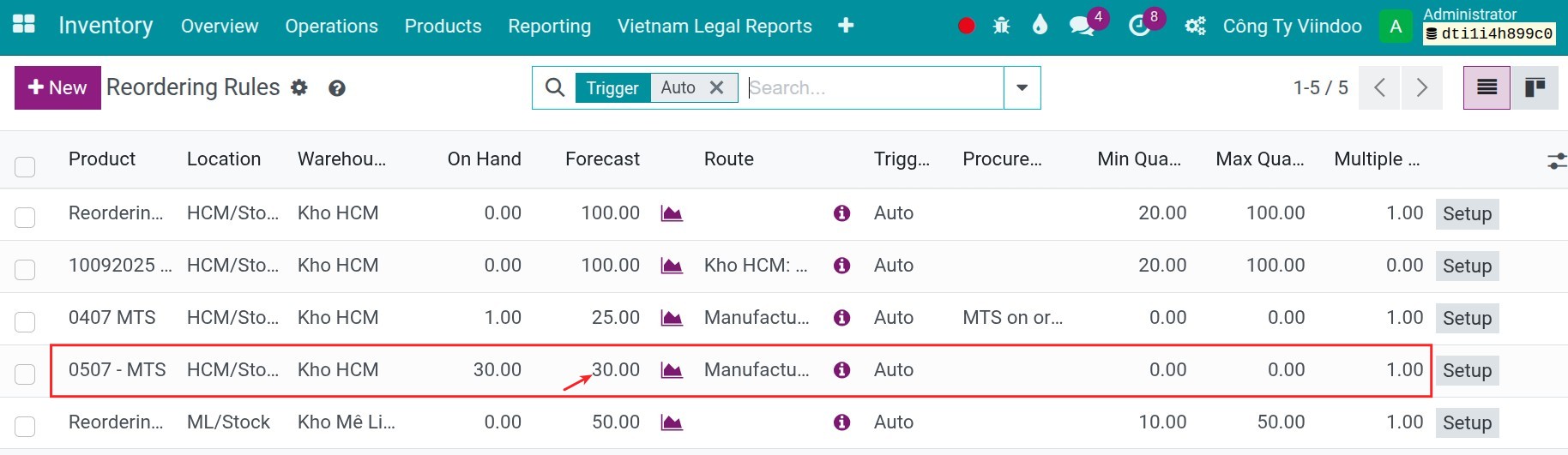
When sale order is confirmed:
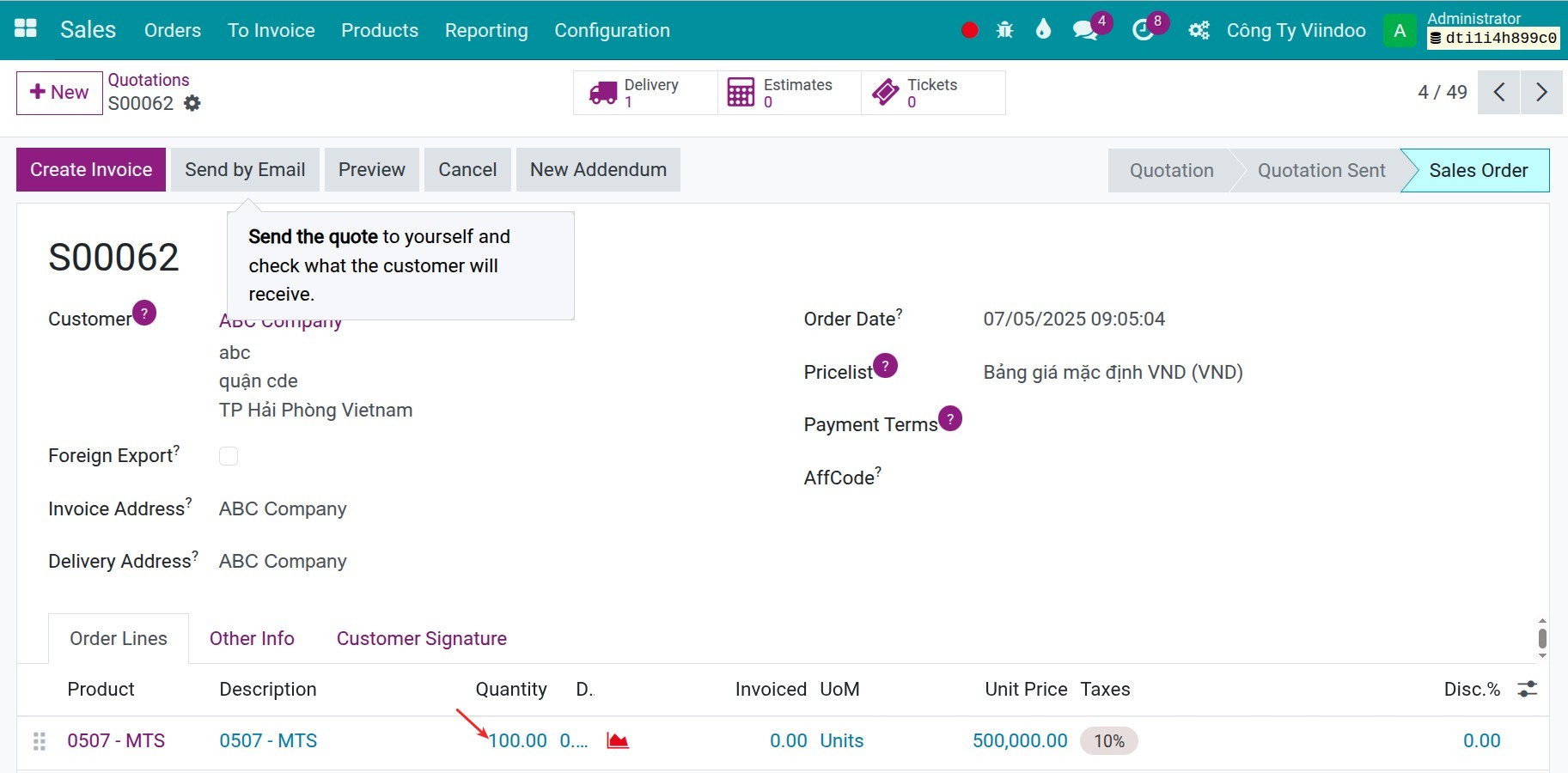
A new manufacturing order is generated with 70 units:
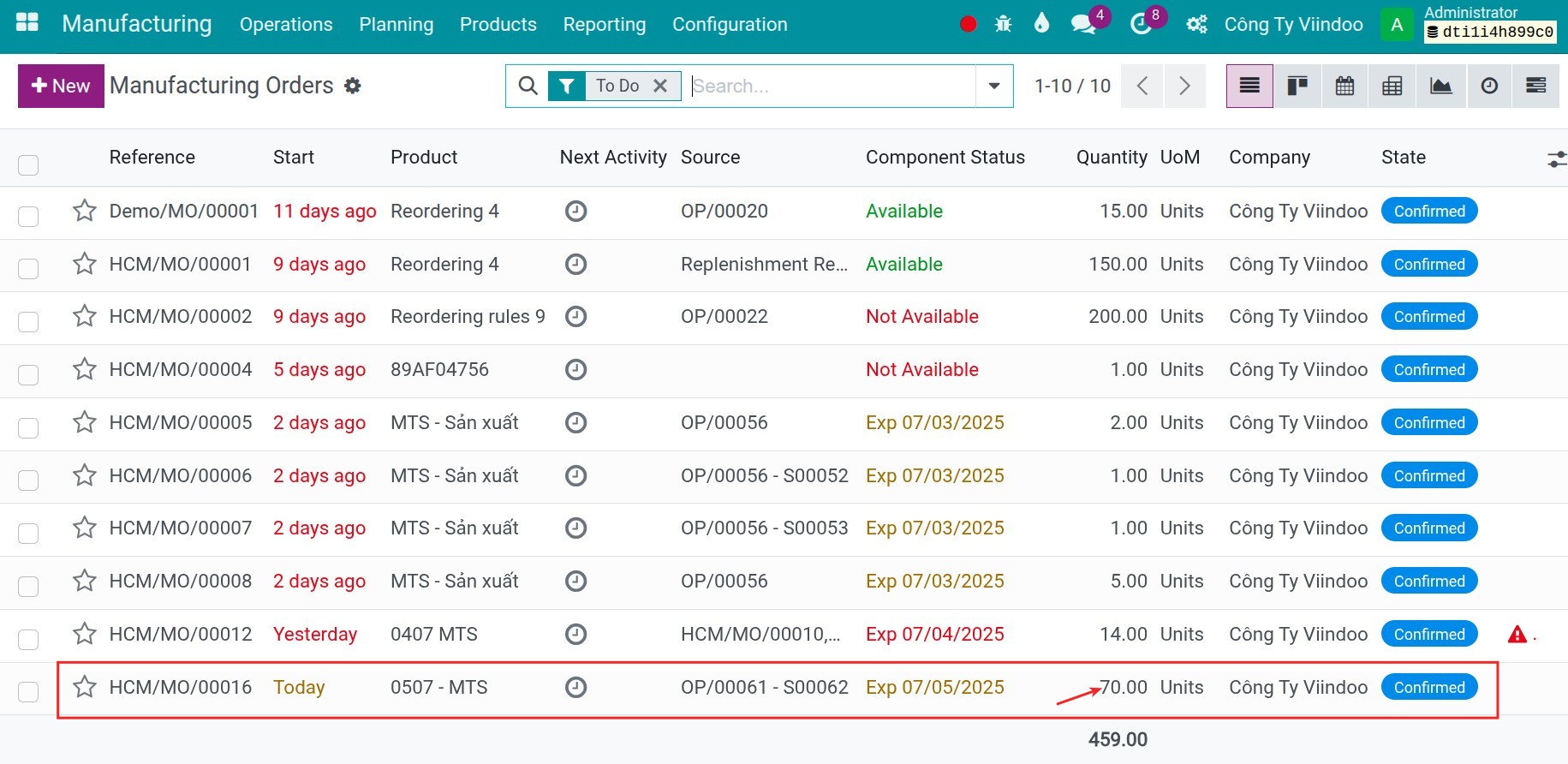
Note
Ensure that the product is configured with a valid Bill of Materials to enable manufacturing order generation.
The available quantity used by the reordering rule is based on the Forecasted Quantity displayed in the rule’s configuration.
Another sale order of this product is confirmed, the quantity will be merged to the exists manufacturing order:
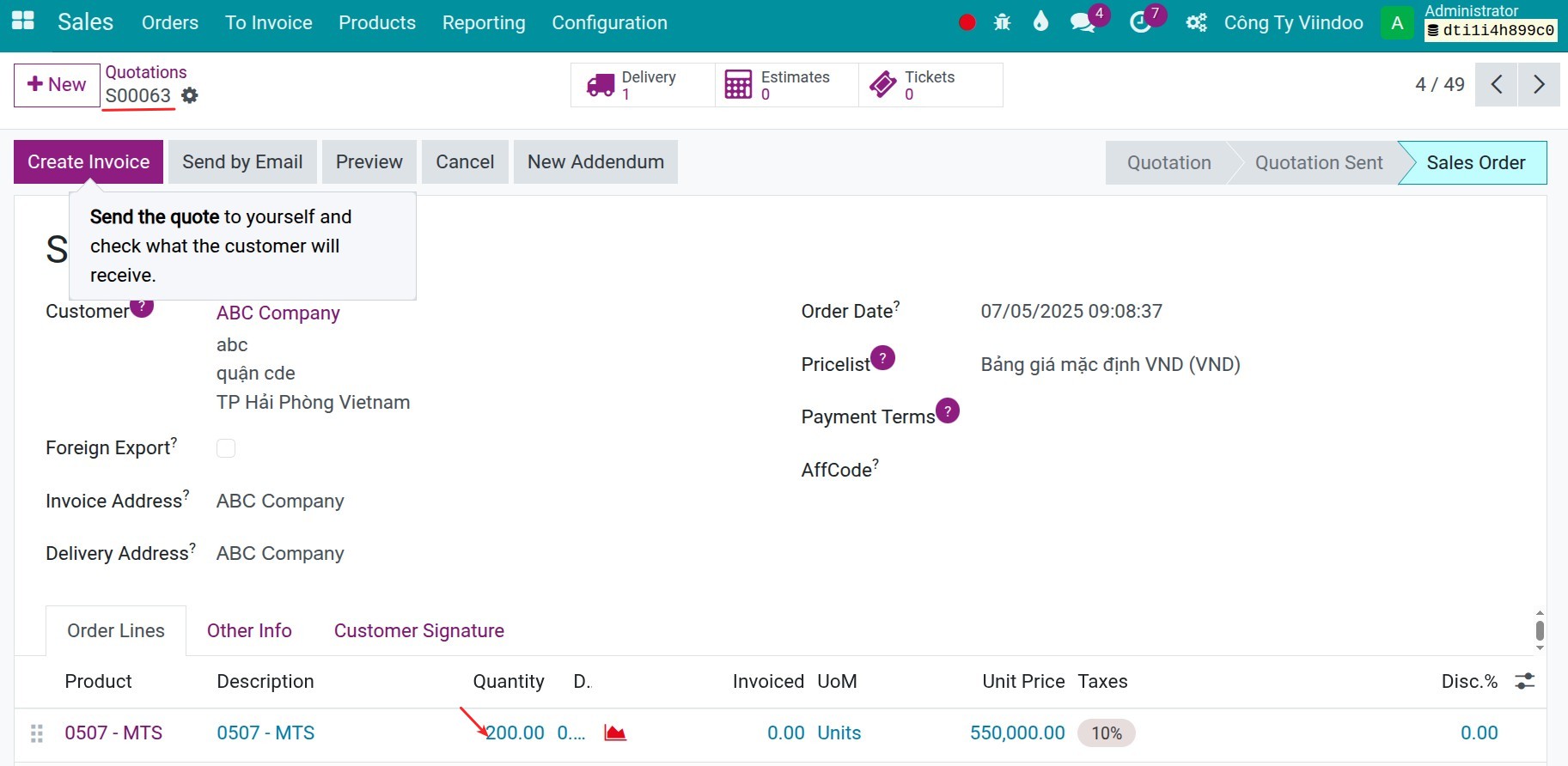
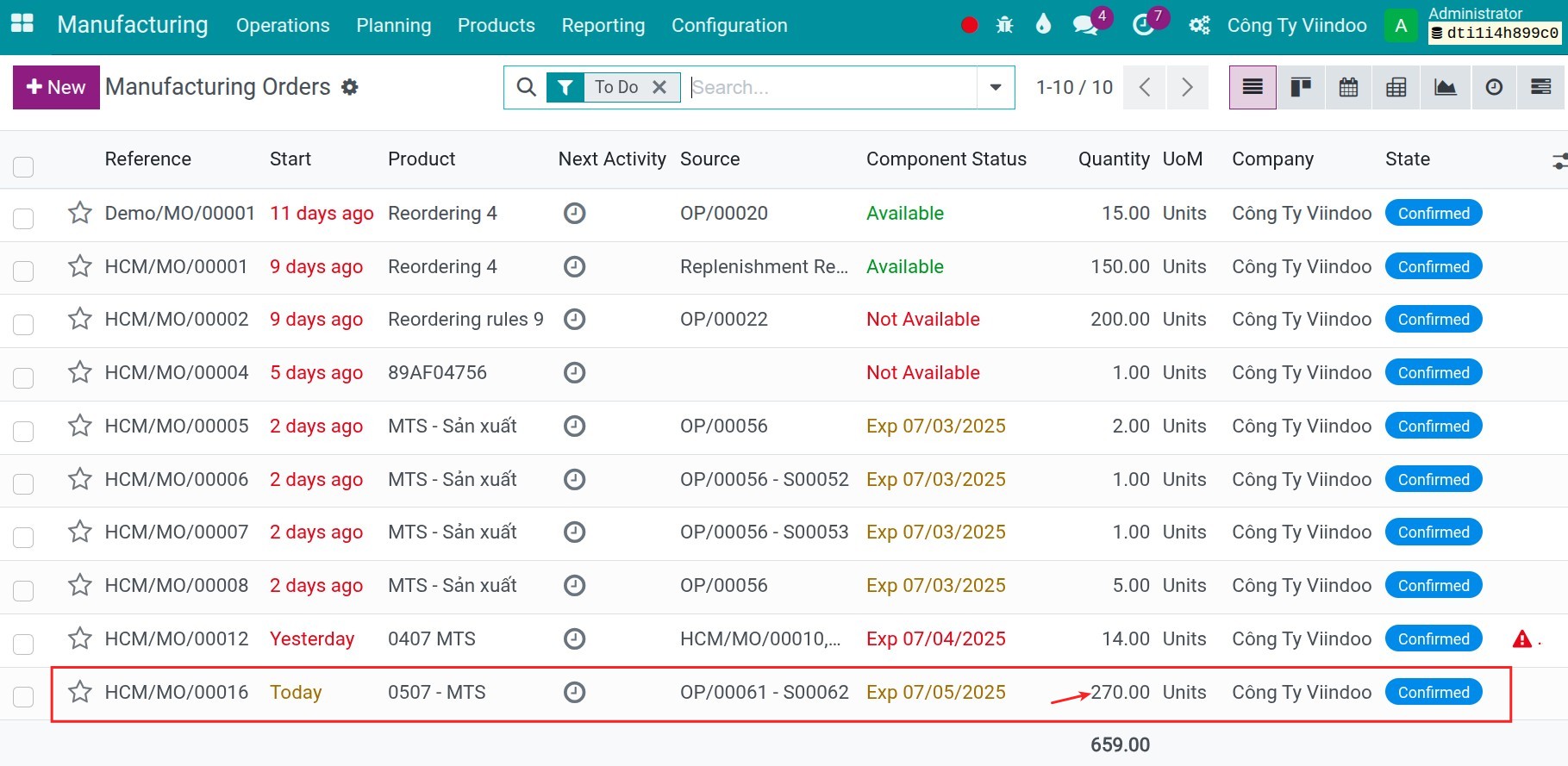
On the manufacturing order, you can see all the respectived sale orders by pressing on Allocation:
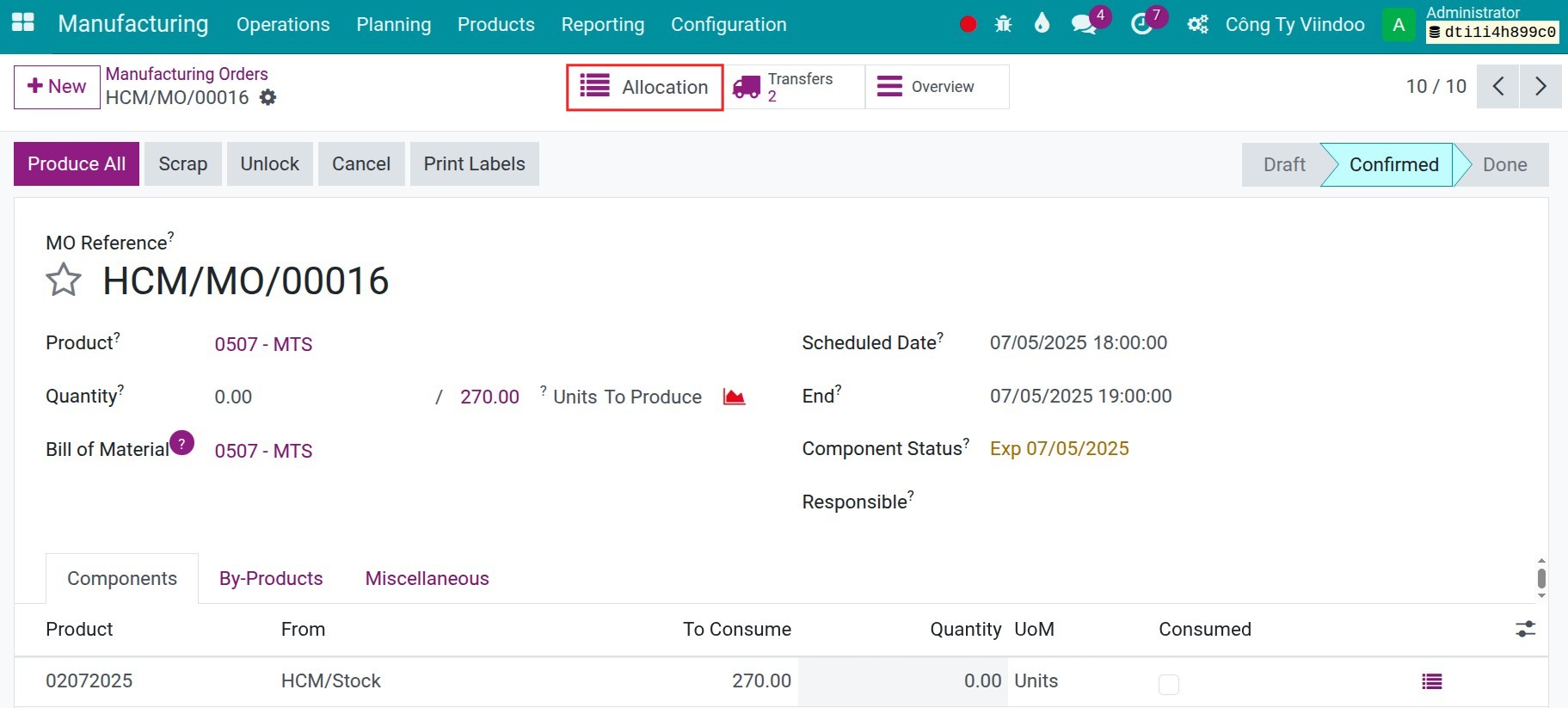
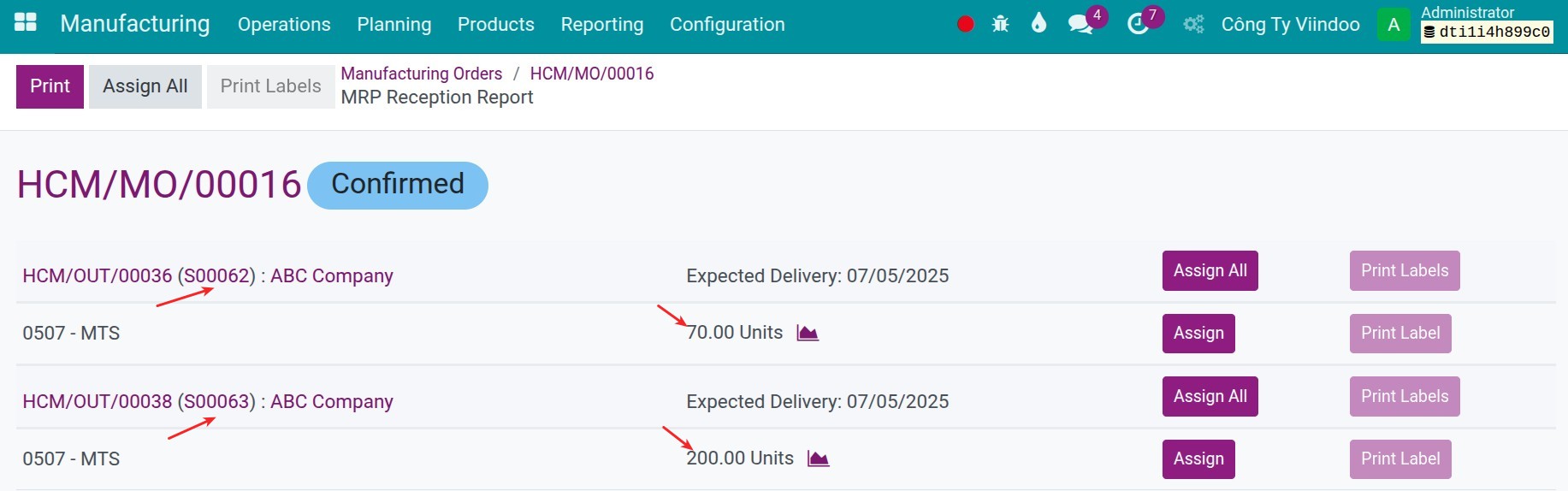
By pressing Assign on each corresponding delivery of sale order, you can link this sale order to the manufacturing order:
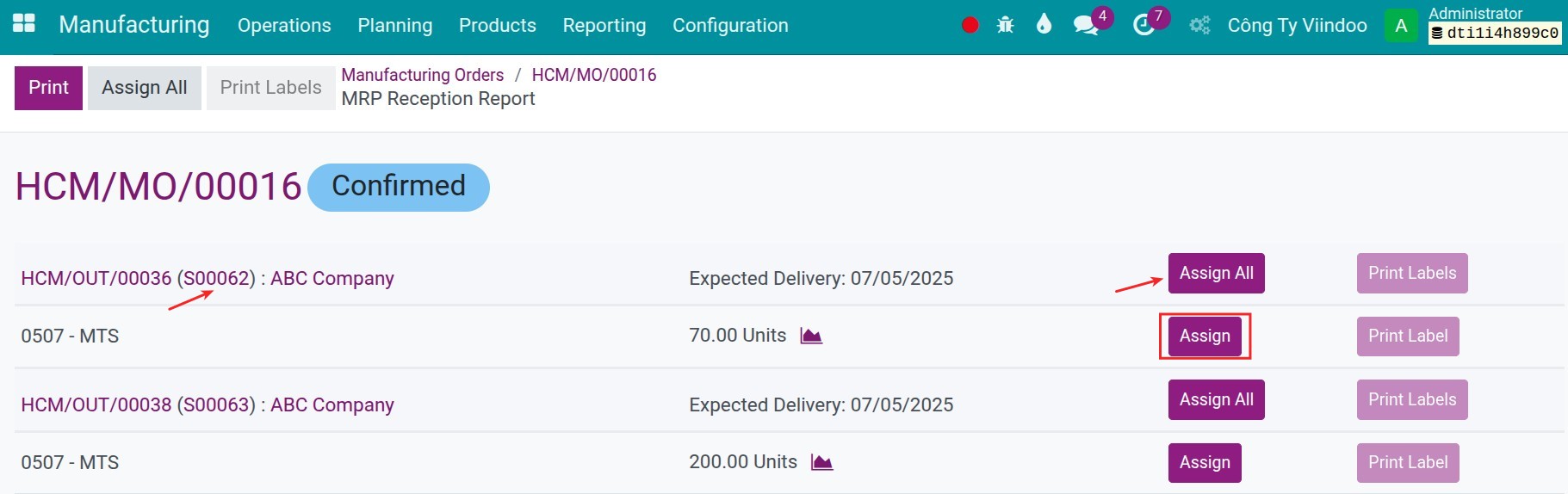
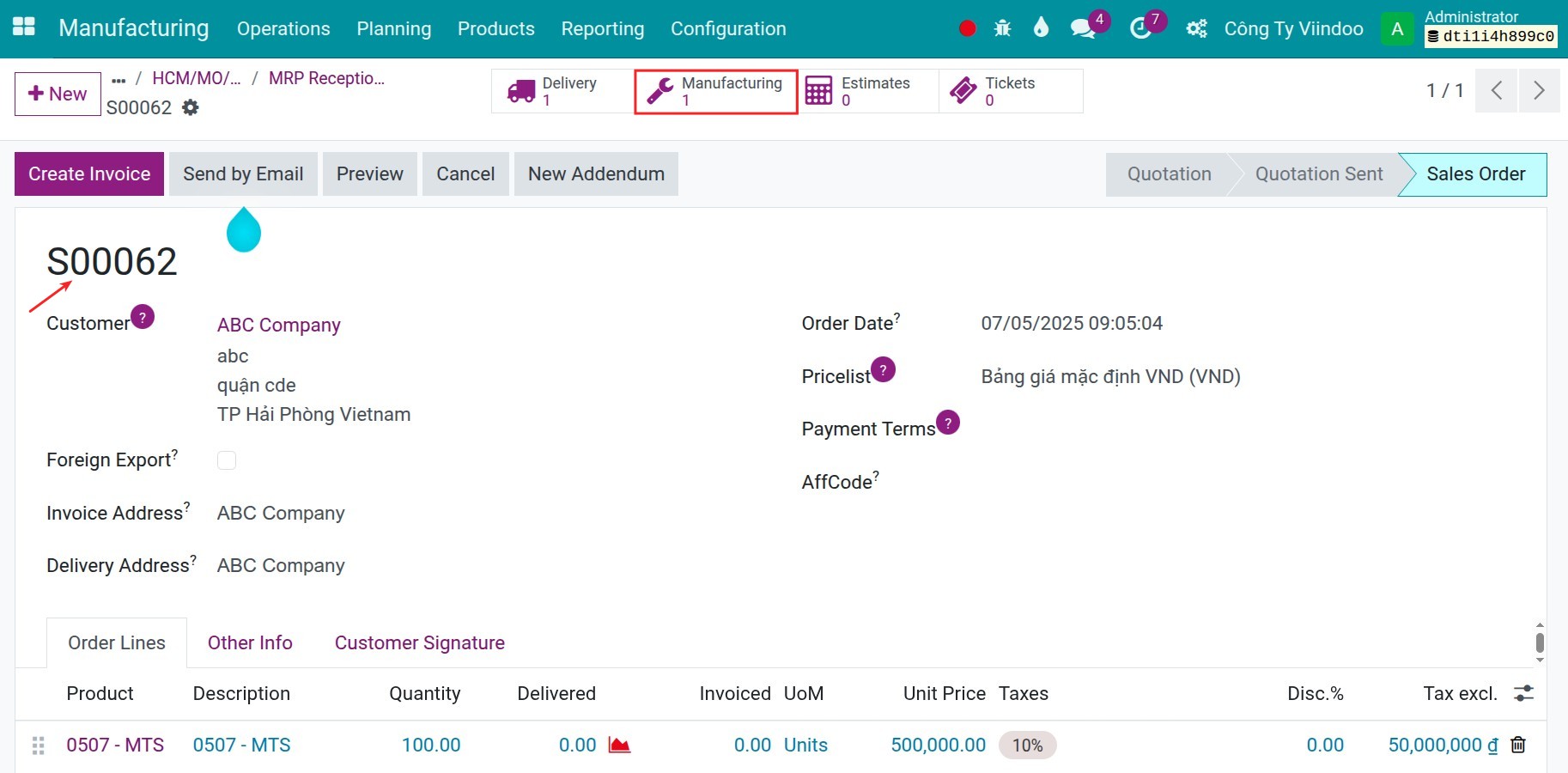
Replenishment with procurement group configuration¶
Example behavior:
Product has reordering rule 0/0/1.
A Sales Order 1 is confirmed for 100 units.
A Sales Order 2 is confirmed for 200 units.
There are 30 units available in stock.
Expect: The system will generate MO 1 with 70 units for SO 1 and MO 2 with 200 units for SO 2.
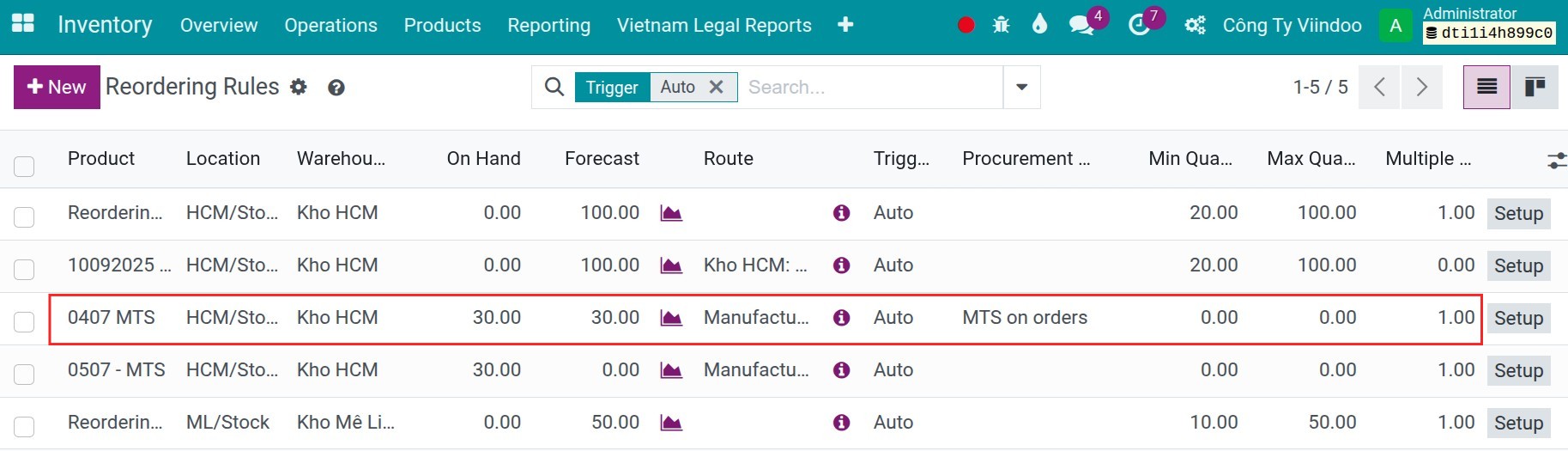
When SO 1 and SO 2 are both confirmed:
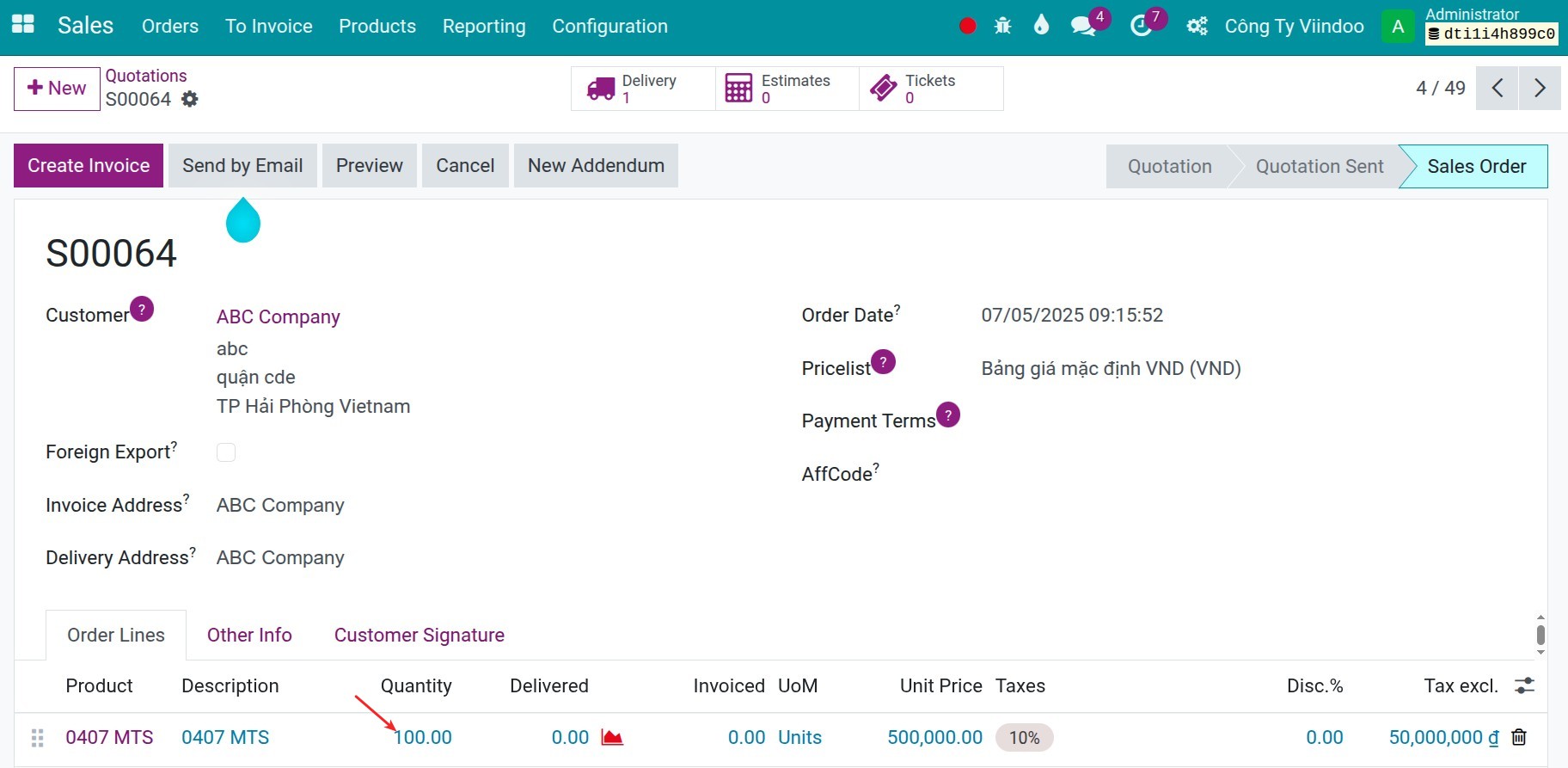
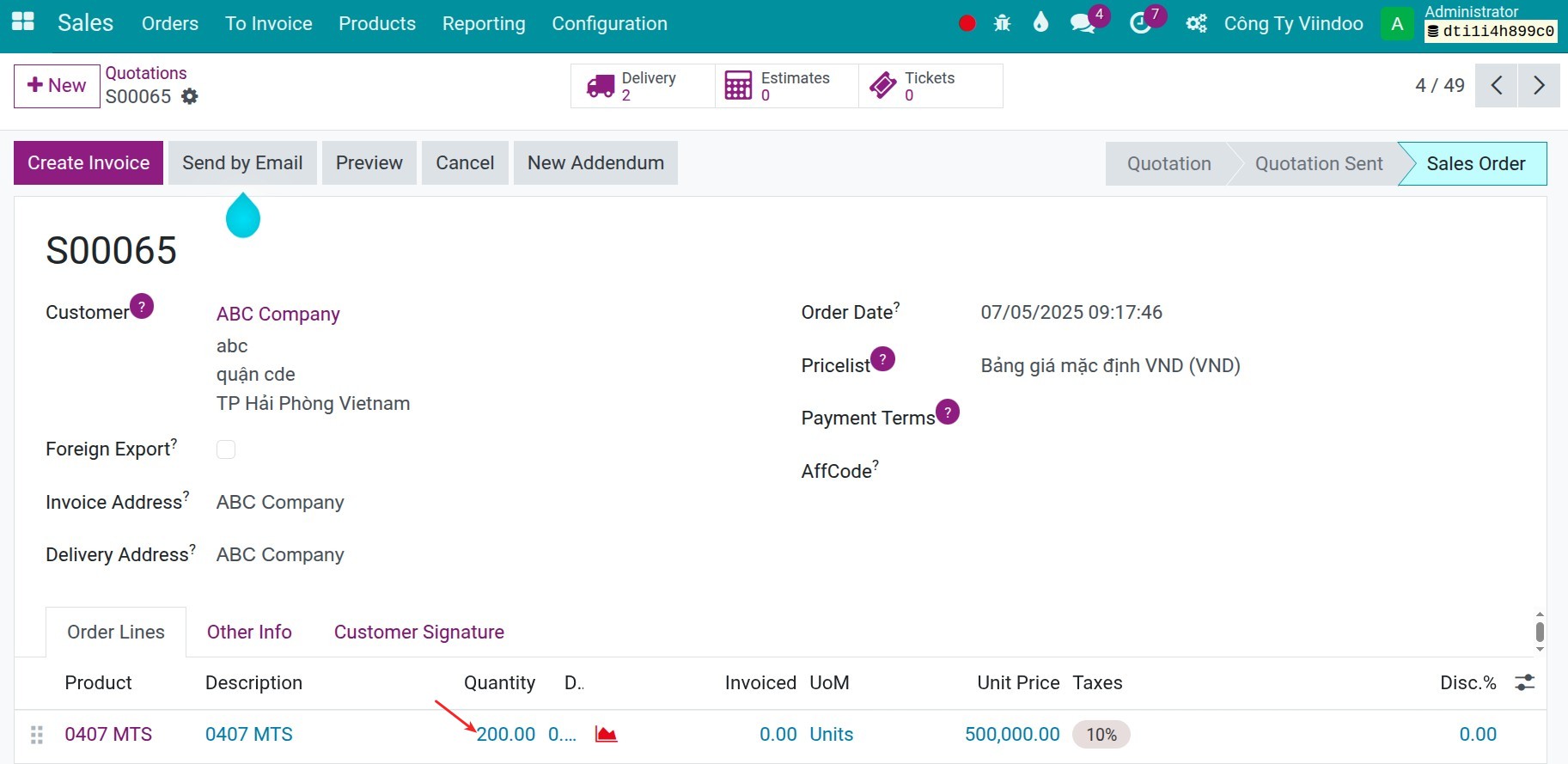
Two new manufacturing orders are generated:
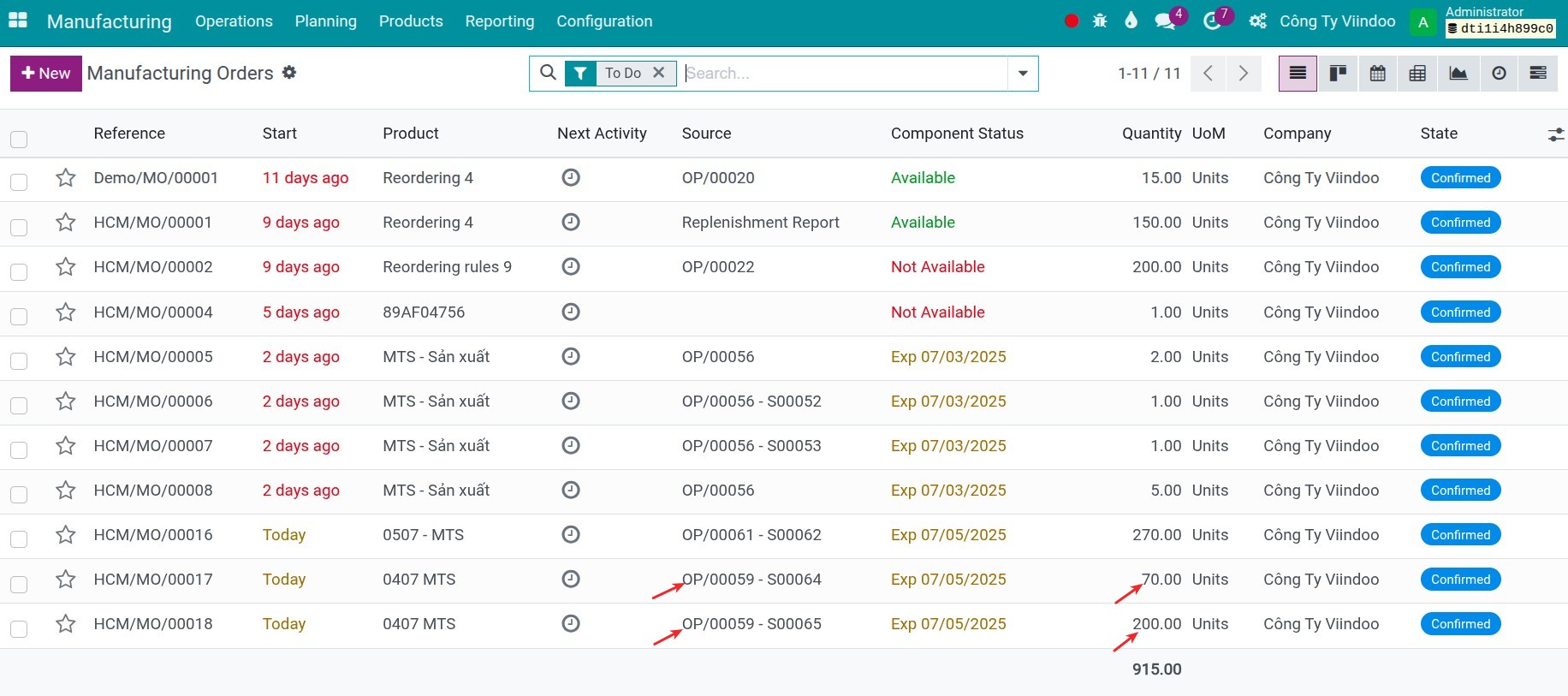
See also
Related article
Optional module