Manage Manufacturing process in Viindoo¶
In addition to reality, in order to plan and manage a production process, businesses will take a lot of time to organize and allocate resources for production, estimate the time of implementation, and calculate the cost of production. Not to mention that such planning can deviate from reality due to being done manually or lacking a basis for accurate calculation. At the same time, if multiple production processes are carried out simultaneously, the calculations will become exponentially complex.
Viindoo Enterprise Management Software provides tools for managing business production processes. These include:
Managing multiple production processes simultaneously;
Organizing and allocating resources for each production stage (work orders) optimally;
Monitoring the execution (operations) of production stages;
Analyzing the time and cost of a production order for planning and costing.
Requirements
This tutorial requires the installation of the following applications/modules:
Let’s take a look at the following example to see how to manage the manufacturing process of Wooden Table:
To manufacture a Wooden table, you need a Bill of Material (BoM):
Table top: 1 Unit;
Wooden table leg: 4 Units;
Paint: 1 liter;
Nail: 10 Units;
Crew: 10 Units.
Going through the stages:
Grind table legs (performed by Grinding Machine);
Assembly (performed by Assembly Team);
Spray paint (erformed by Spray paint).
Work centers involved:
Grinding Machine:
Working Hours: Operating for 8 hours per day. Within that, there is a 1-hour pause for rest and refueling.
Able to grind 420 legs per day.
The total cost for the grinding machine average about 60,000 VND per day.
Assembly Team:
10 people;
Working Hours: 8 hours/day. Working efficiently in 6.4 hours;
Able to assemble 256 tables per day;
The salary of 10 workers in the assembly team is 8,000,000 VND per day.
Spray paint Team:
4 people;
Working Hours: 8 hours/day. Working efficiently in 6.4 hours;
Able to ppray paint 384 tables per day;
The salary of 4 workers in the assembly team is 1,600,000 VND per day.
Configuration¶
To utilize the feature, navigate to Manufacturing ‣ Configuration ‣ Settings, active the Work Orders feature.
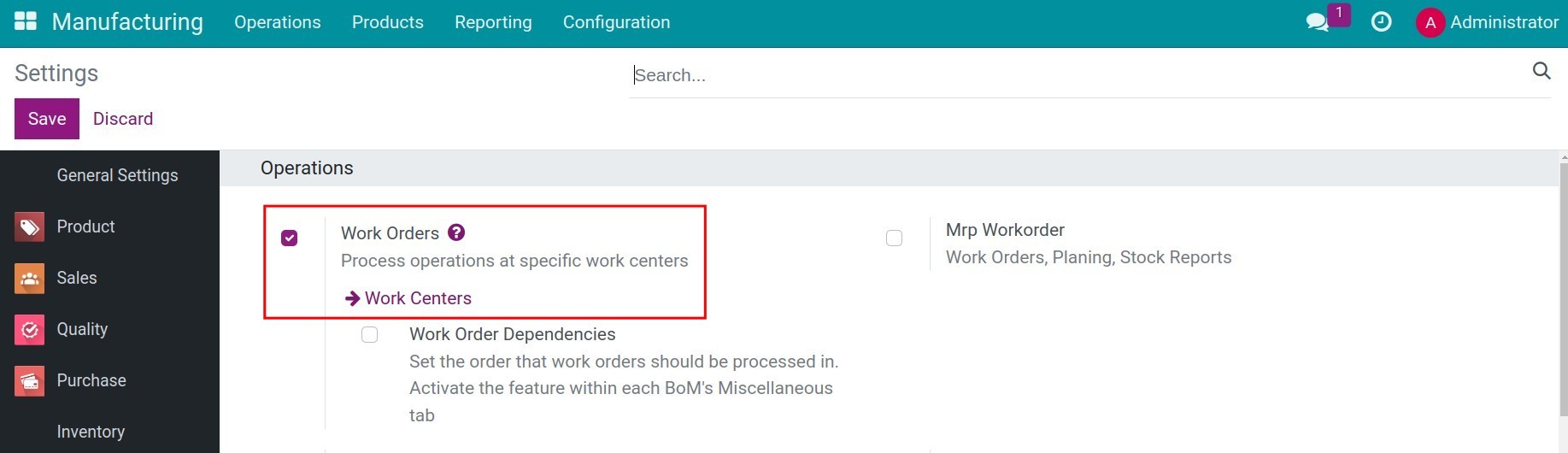
Click on Save to complete the feature activation.
Configure Work Centers¶
To create 2 work centers Assembly Team and Spray paint Team, navigate to Manufacturing ‣ Configuration ‣ Work Centers, click on New button to create a new work center:
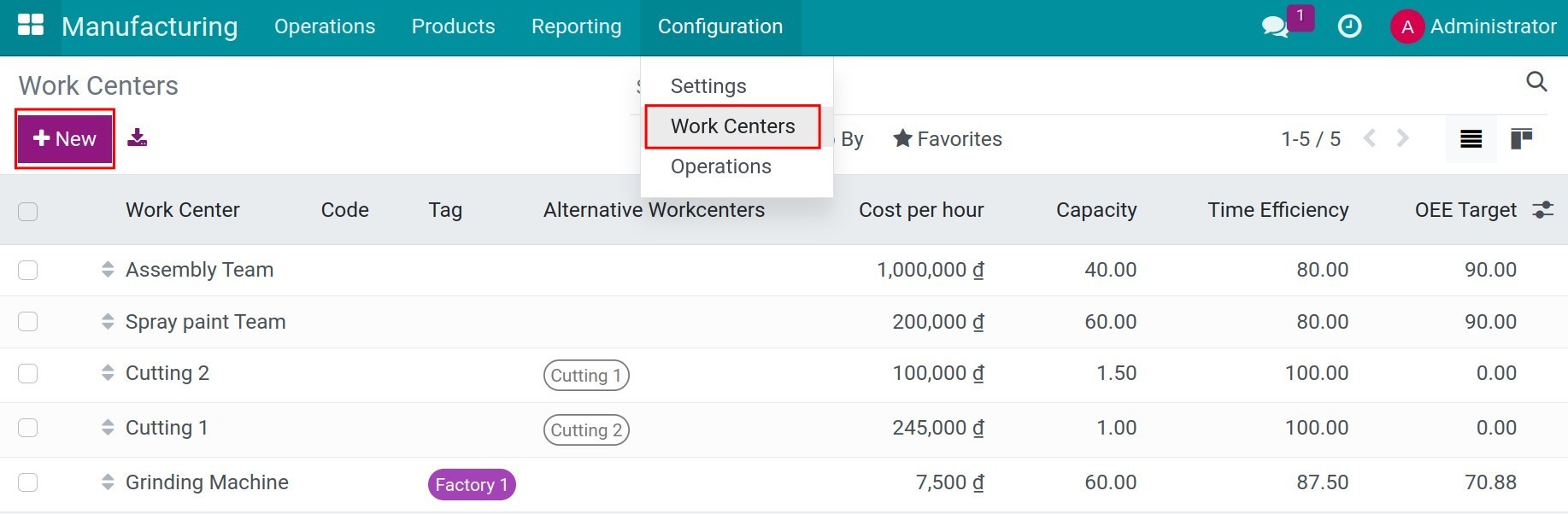
Then, fulfill the information below:
Work Center Name: Name of the work center;
Tag: Using tags to mark, classify, and manage different groups of;
Alternative Workcenters: Choose the work center replacing this work center in case it is used to execute other work orders;
Code: Fulfill the code for the above work center;
Working Hours: Select working hours for the work center. The working hours are the foundation to make work orders for the work centers;
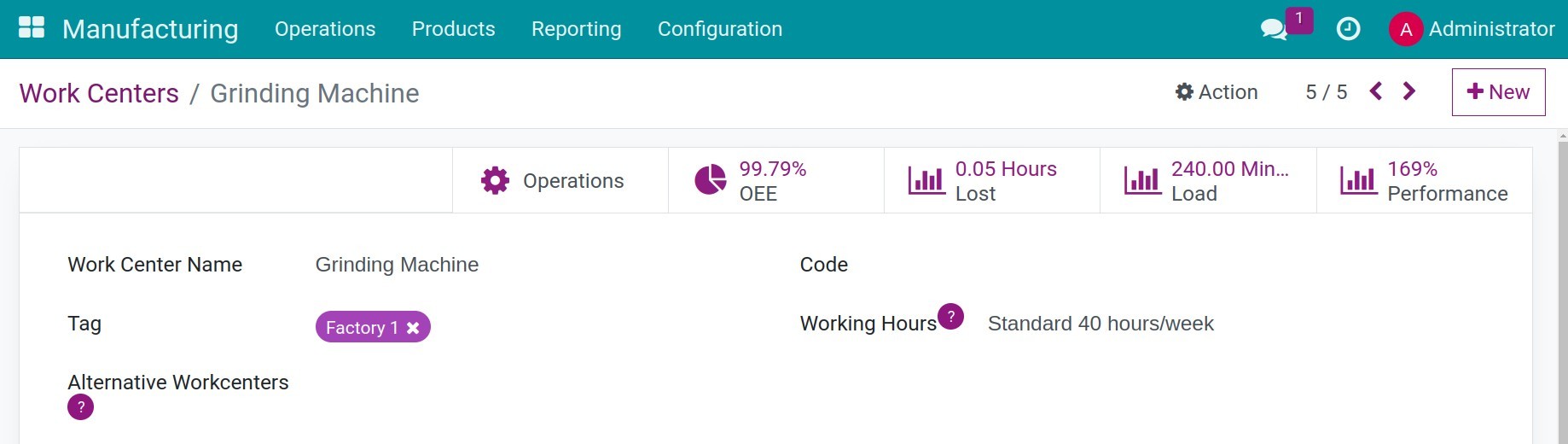
General Information Tab:
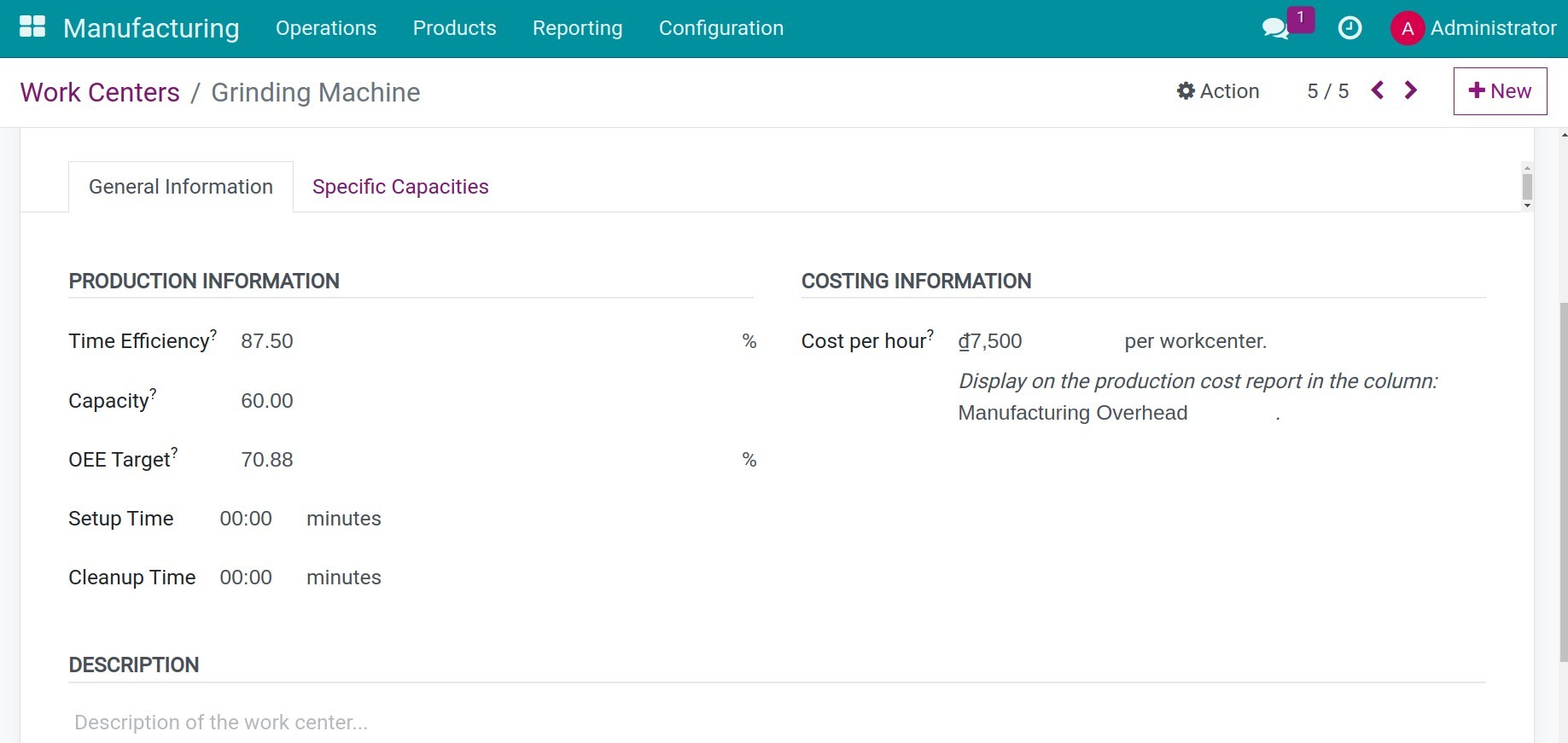
Production Information:
Time Efficiency:
Calculated as the actual operating time (effective operating time) divided by the total theoretical operating time, expressed as a percentage (%).
Typically, the time efficiency of a production capacity ranges from 0% to 100%.
Capacity:
It represents the ability to produce products within a unit of time for this production capacity (in this case, Viindoo software calculates it per hour). It is calculated based on the quantity of products that this production capacity can produce within a unit of time.
Capacity also reflects the time it takes for the production capacity to produce one product: the higher the capacity, the shorter the time to produce one product.
OEE Target:
OEE - Overall Equipment Efficiency of a manufacturing capacity is calculated by multiplying Time Efficiency (A) x Capacity Efficiency (P) x the Quality Product Yield (Q).
Setup Time: The total time calculated from the start of a production order until the actual production capacities start operating. Businesses need to input this information to plan production based on actual time and monitor the time wasted during the pre-production phase.
Cleanup Time: The total time calculated from when the production capacities stop operating until the production is completed and ready for the next production orders. The significance of this information is similar to the Setup Time mentioned above.
Costing Information:
Cost per hour: Cost of the work center per hour.
Description: Fulfill with the detailed description of the work center.
Specific Capacities Tab: Declare the Capacity of this production capacity for specific products (if applicable).
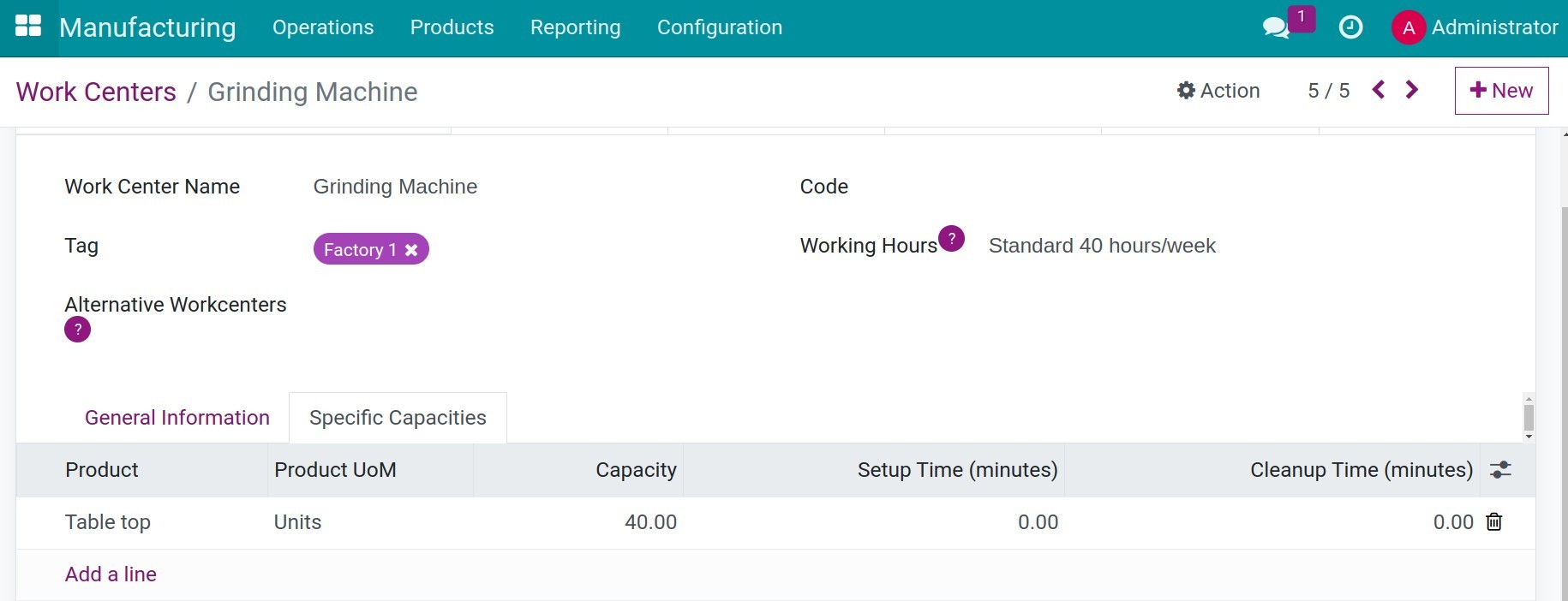
For the given example, we can estimate the following for each Work order:
Grinding Machine:
Time Efficiency: 87.5% (=7/8 x 100)
Capacity: 60 (=420/6.4)
OEE Target: 70.88% (Assuming the Grinding Machine operates efficiently for 7 hours, the standard capacity is 467 pieces per hour, and 90% of the products are of quality)
Cost per hour: 7,500 VND
Assembly Team:
Time Efficiency: 80% (=6.4/8 x 100)
Capacity: 40
OEE Target: 64% (Assuming Assembly Team operates efficiently for 6.4 hours, the standard capacity for a team of 10 workers is to assemble 50 pieces per hour, with 100% of the assembled tables being free of defects)
Cost per hour: 1,000,000 VMD
Spray paint Team:
Time Efficiency: 80% (=6.4/8 x 100)
Capacity: 60
OEE Target: 64% (Assuming Spray paint Team operates efficiently for 6.4 hours, the standard capacity for a team of 4 workers is to paint 75 pieces per hour, with 100% of the painted tables being free of defects)
Cost per hour: 200,000 VND
At each work center, you can see the statistical reports as follows:
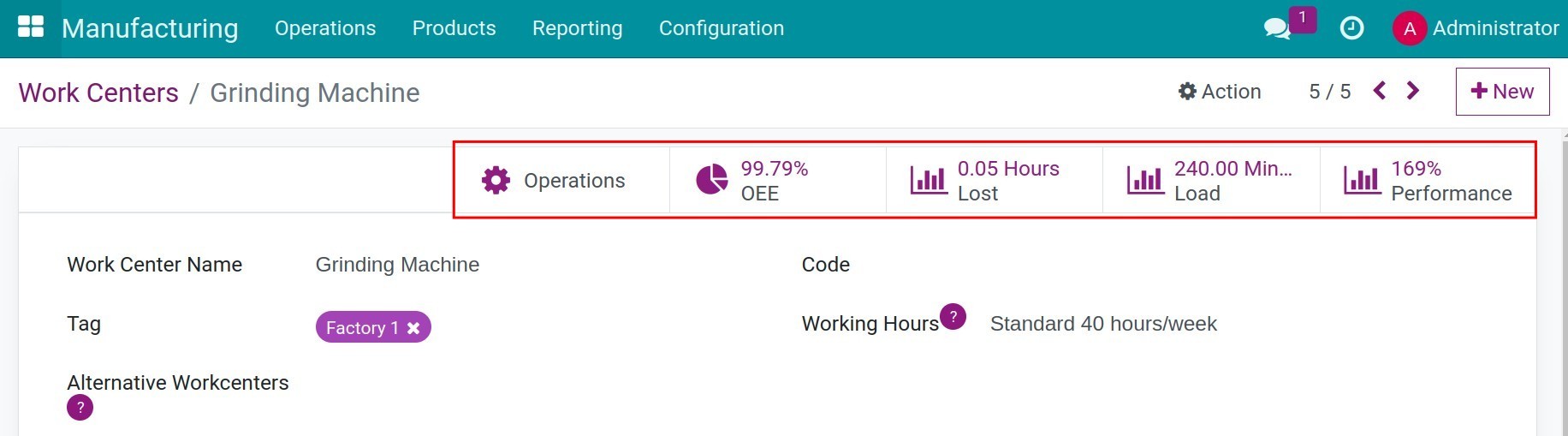
Operation: All Operation this work center perform;
OEE: OEE report of the work center;
Lost: Report of the duration of the performance loss and the reasons for the performance loss during manufacturing execution.
Load: Report of the executed duration of the work center;
Performance: Report about the performance of the work center.
See also
Configure Operations¶
With 2 manufacturing operations as Assembly and Spray paint, you navigate to Manufacturing ‣ Configuration ‣ Operations, click on New to create an operation.
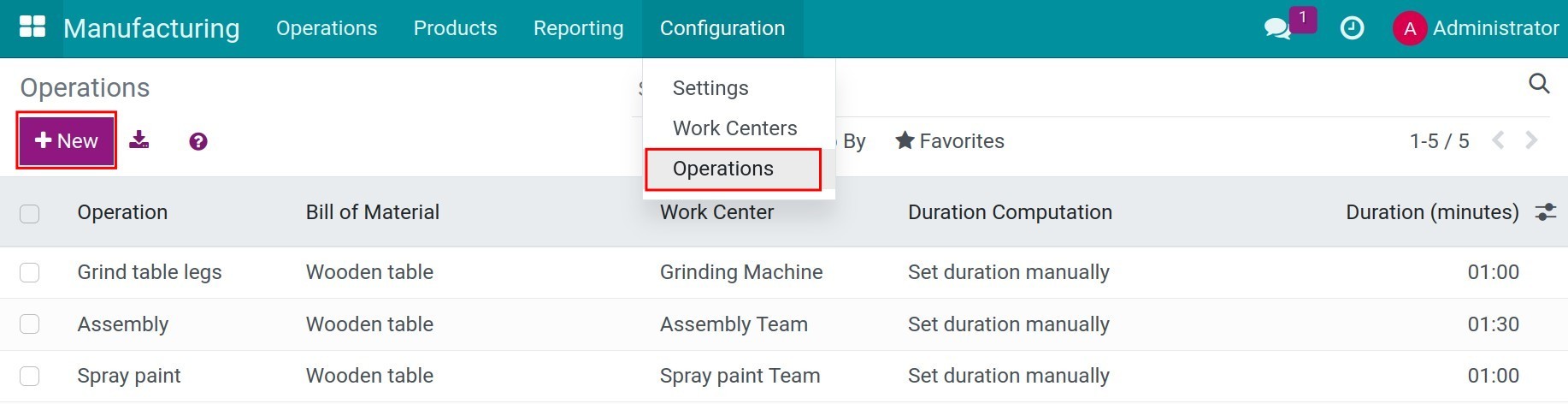
Then, fulfill the information below:
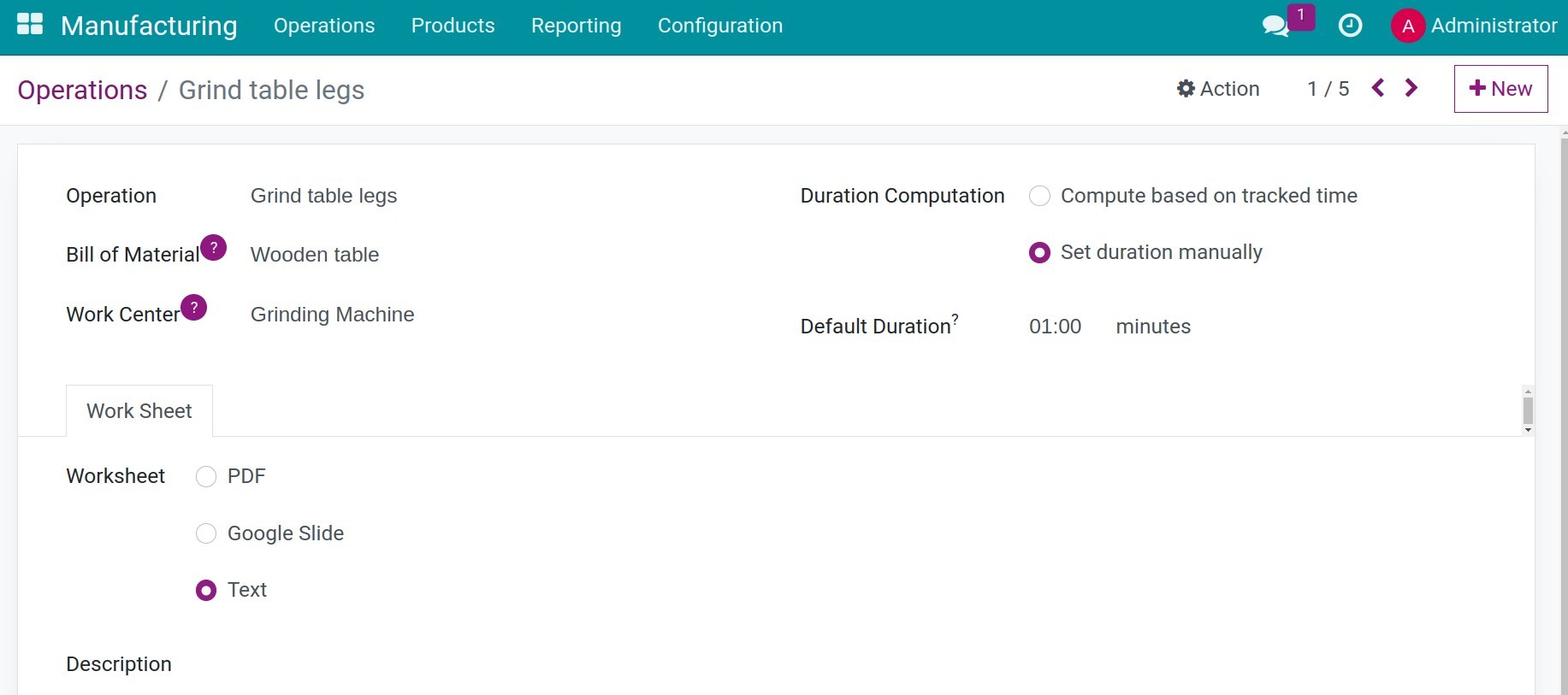
Operation: Name of the manufacturing operation;
Work Center: Select the work centers that execute the manufacturing operation;
Bill of Material: Select the bill of the material linked to the operation;
Duration Computation:
Compute based on tracked time: Compute based on tracked time: If checked, the system will automatically calculate based on the actual time data of the declared number of work orders. For example: You can choose to compute based on the 5 nearest finished worker orders;
Set duration manually: If checked, you will be allowed to set the estimated duration manually for the operation.
Default Duration: It is the default time required to produce one unit of the product when using this Operation;
Work Sheet: Select the format of the drawing/instruction file uploaded for the operation;
Description: Fulfill with the detailed description of this operation.
Apply Work Centers, Operations on Bills of Materials¶
After configuring as above, navigate to Manufacturing ‣ Products ‣ Bills of Materials, open the BoM of the Wooden Table. On the Components tab, for each component line, you can add the operation that each material will be consumed.
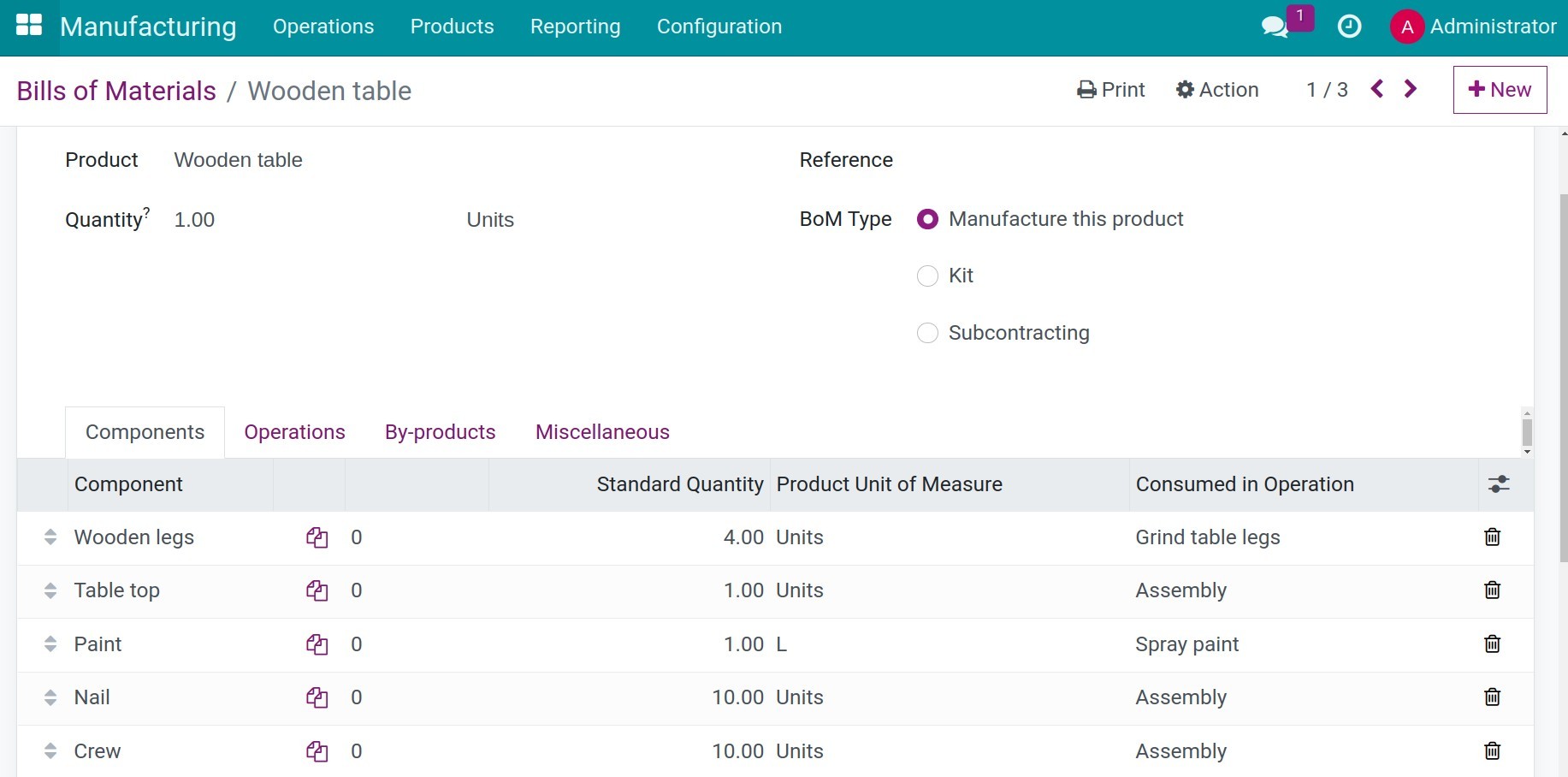
In addition, on the Operations tab, you can see all the manufacturing operations will occur, and work orders will carry them out.
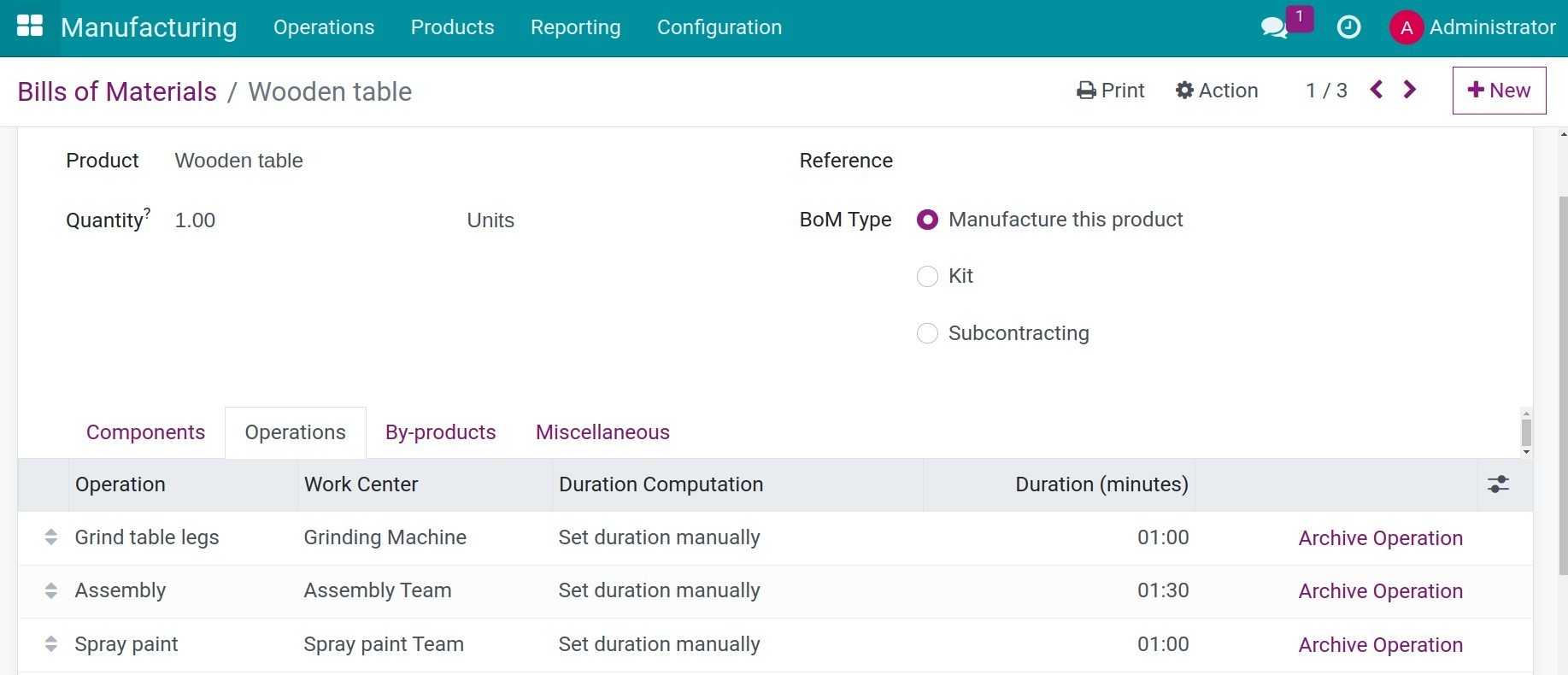
Implement Manufacturing process¶
Create the Manufacturing Orders¶
You can navigate to Manufacturing ‣ Operations ‣ Manufacturing Orders to create a new manufacturing order for Wooden table:
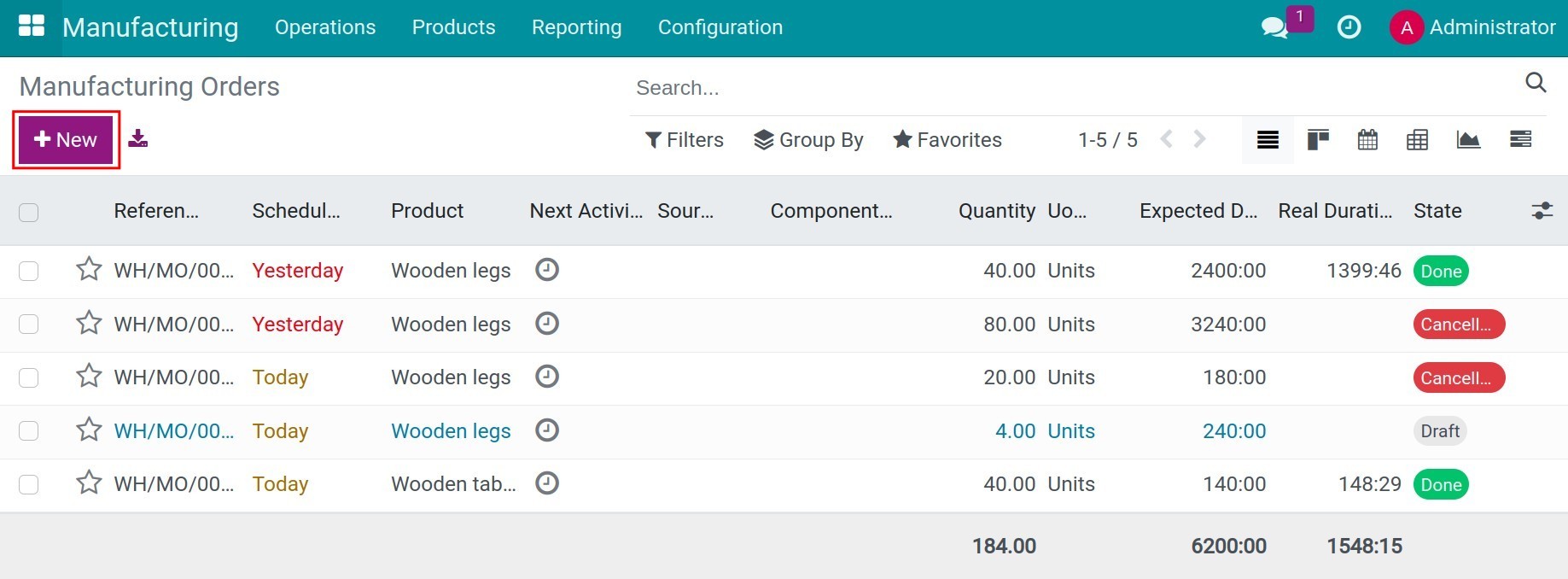
The information to set up the manufacturing order includes:
Product: Choose the product as Wooden table;
Quantity: Fulfill the number of product;
Bill of Material: Select the Bills of materials for the product. When selected, the information of components of bills of materials will be automatically suggested in the Components tab;
Scheduled Date: Scheduled date at which you plan to start the manufacturing operation.
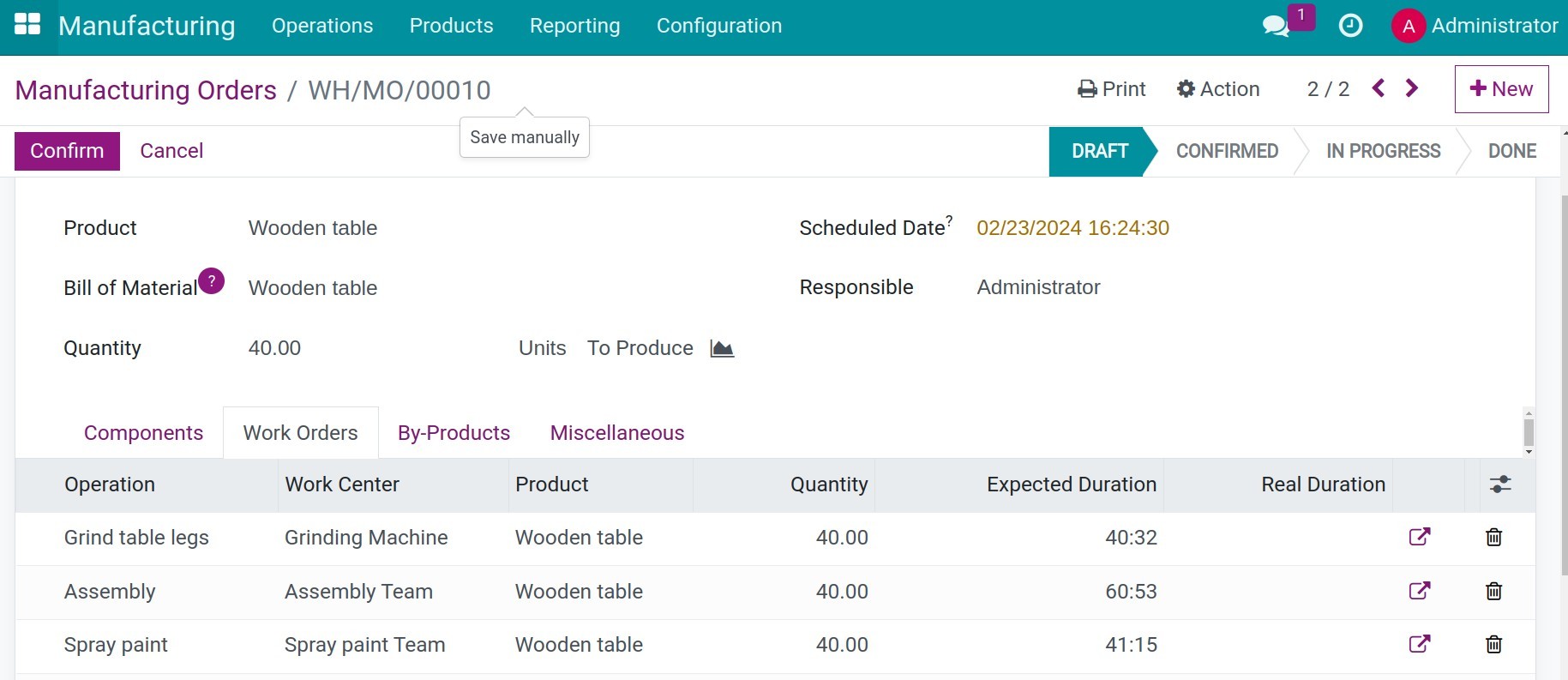
Click on Confirm and Plan for the manufacturing order.
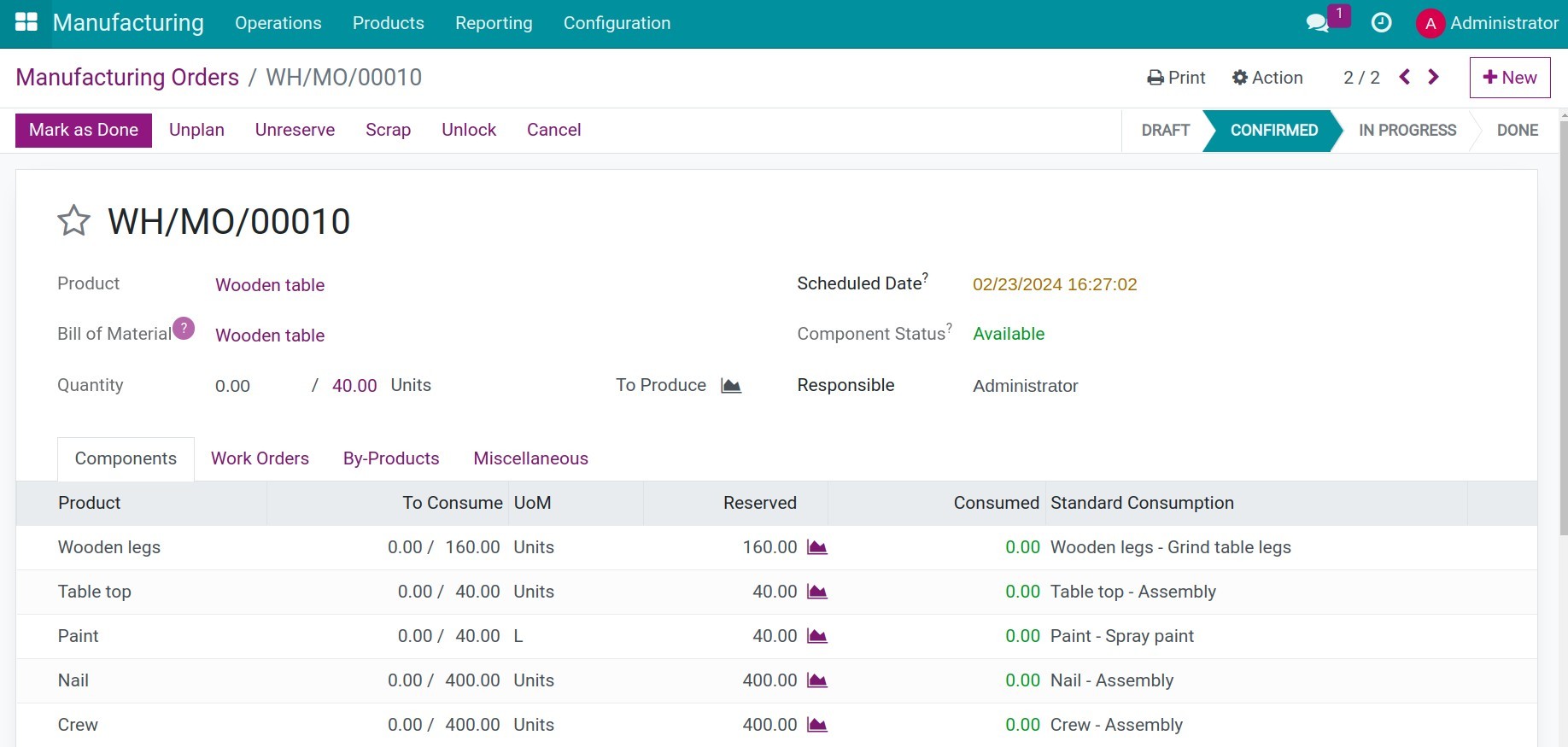
Implementing the manufacturing orders¶
You will then be able to track the status, scheduled start date, expected duration and real duration for each manufacturing operation in the Work Orders tab.
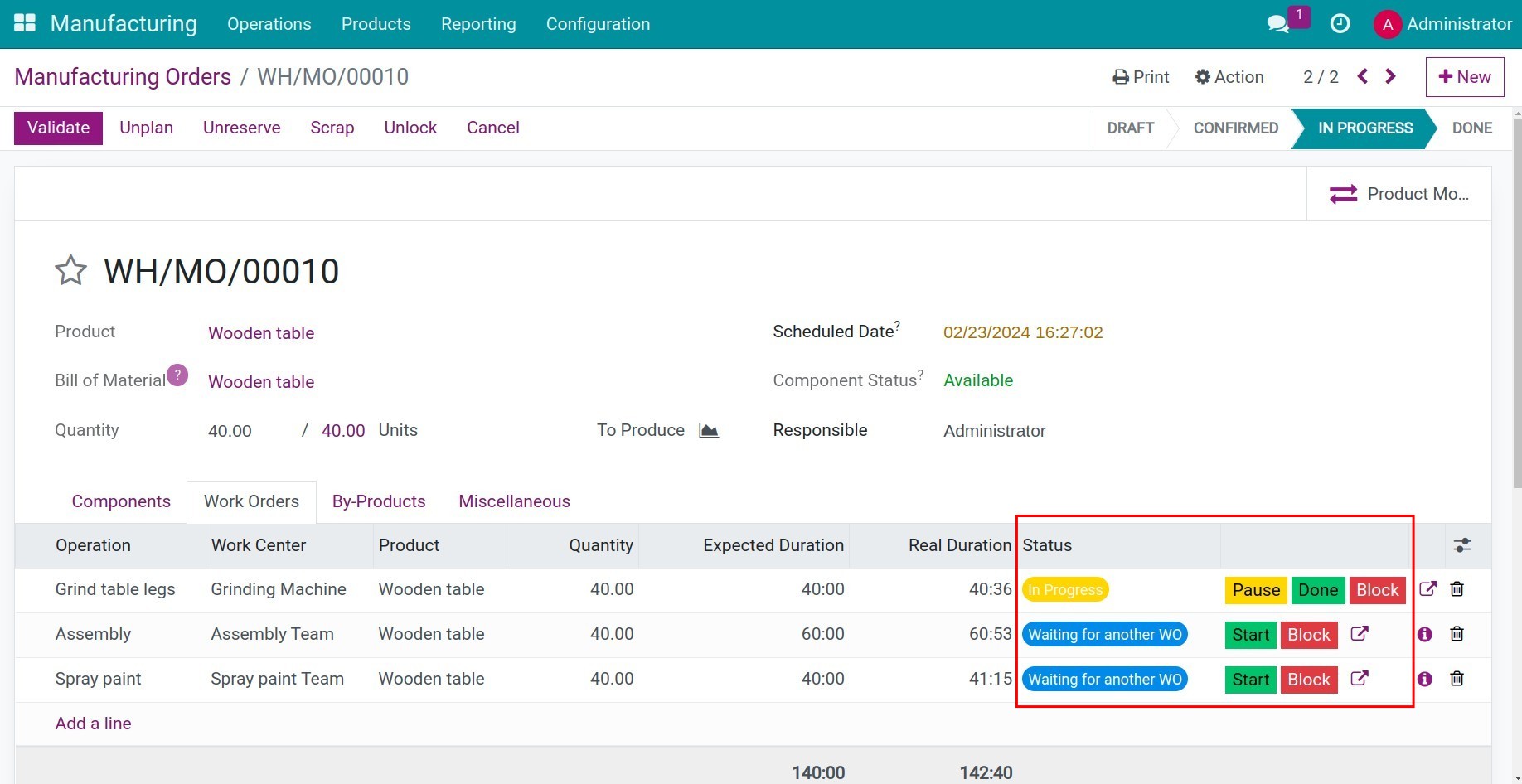
In there:
Click on Start to start the operation;
Click on Pause to pause the operation;
Click on Block if you want to block the operation.
Record the actual consumptions of the materials¶
In fact, after implementing the manufacturing orders, in the end of the process, you will calculate the actual consumptions of the materials. They could be different with the standard quantities that setup on BoM. So, you need to record the actual consumptions of the materials on the manufacturing order by putting on the number on the Consumed column.
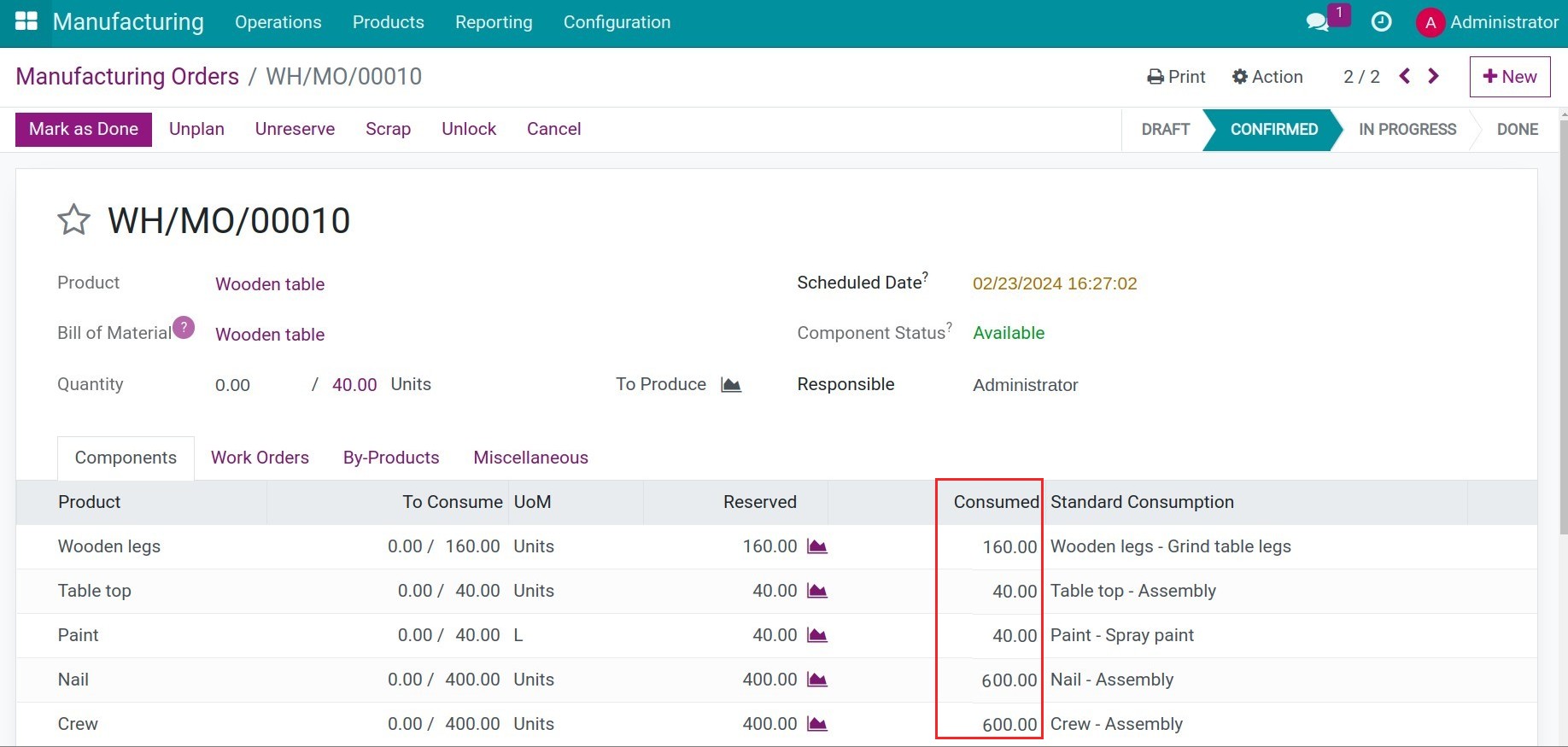
Record the actual quantity of finished products entered into the warehouse¶
Similar with the actual quantity of consumption materials, you input the actual quantity of finished products that were completed and ready to enter into the warehouse.
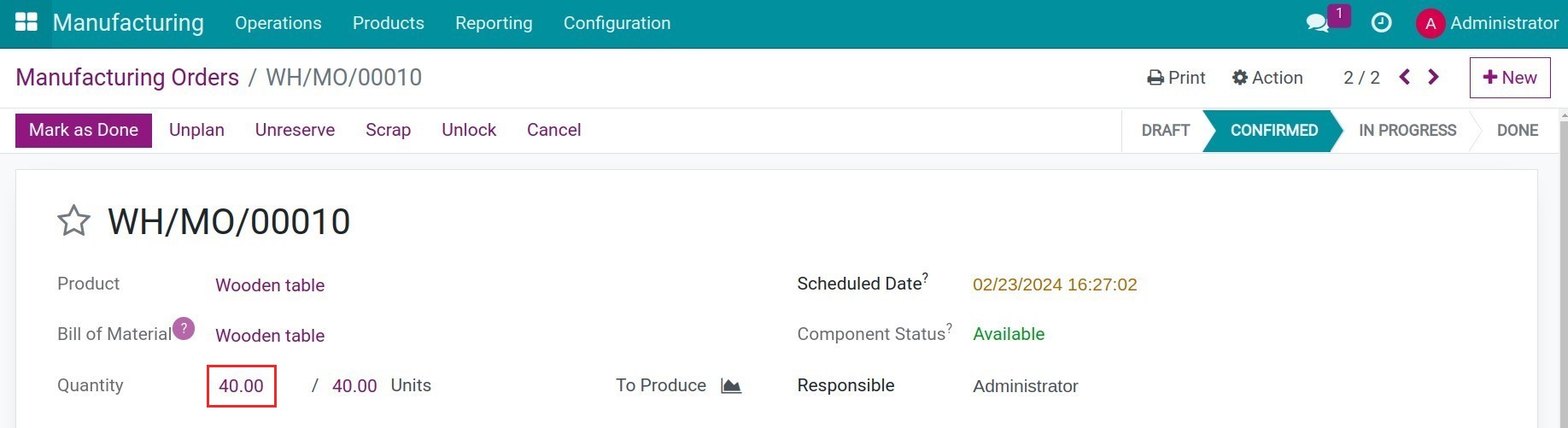
After all, press Mark as Done after completing the manufacturing operations. Then, on Manufacturing Orders, you can view manufacturing reports such as Loss Components Analysis, Valuation and Cost Analysis.
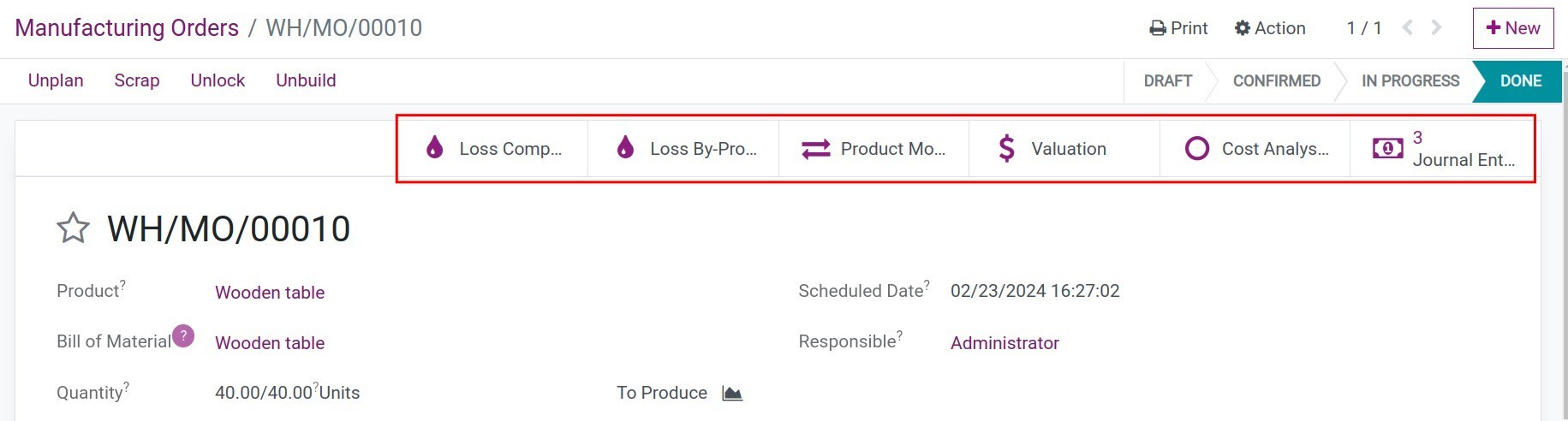
Loss Components Analysis: Record the actual amount of consumed materials during manufacturing compared to the quantity specified in the BOM to calculate the material wastage for this manufacturing order.
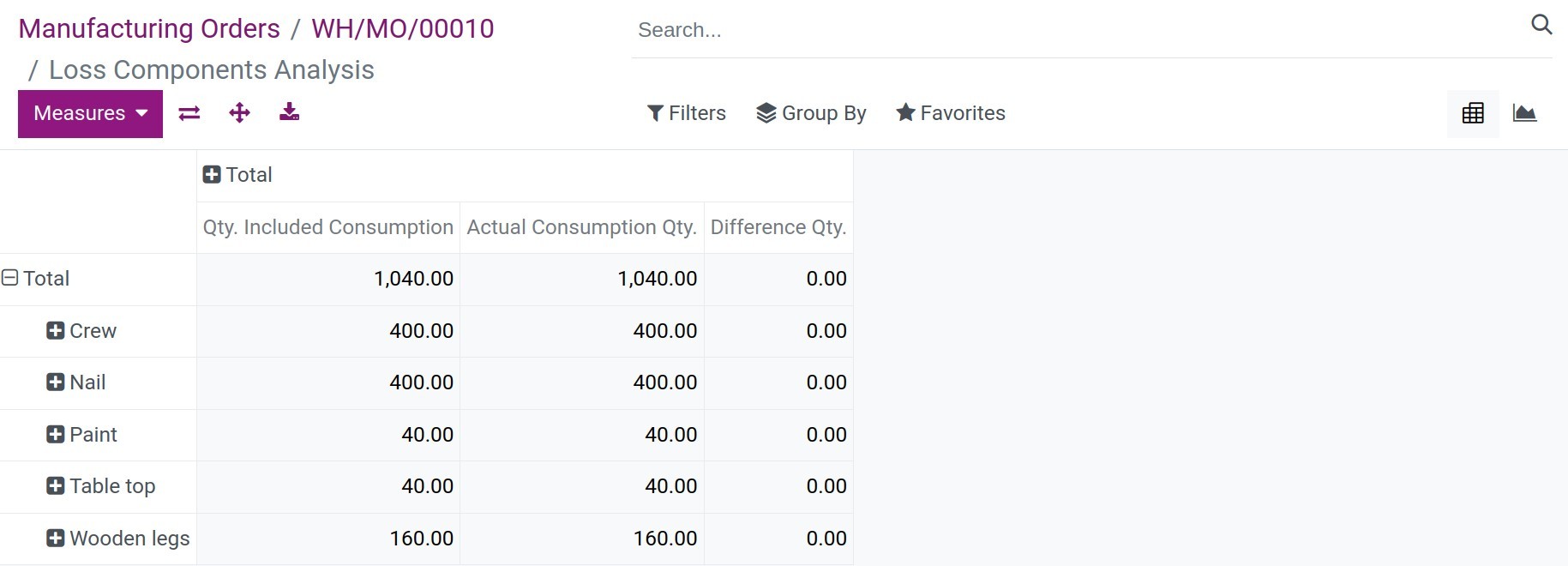
Valuation: Record the quantity and value of components and finished product of manufacturing order.
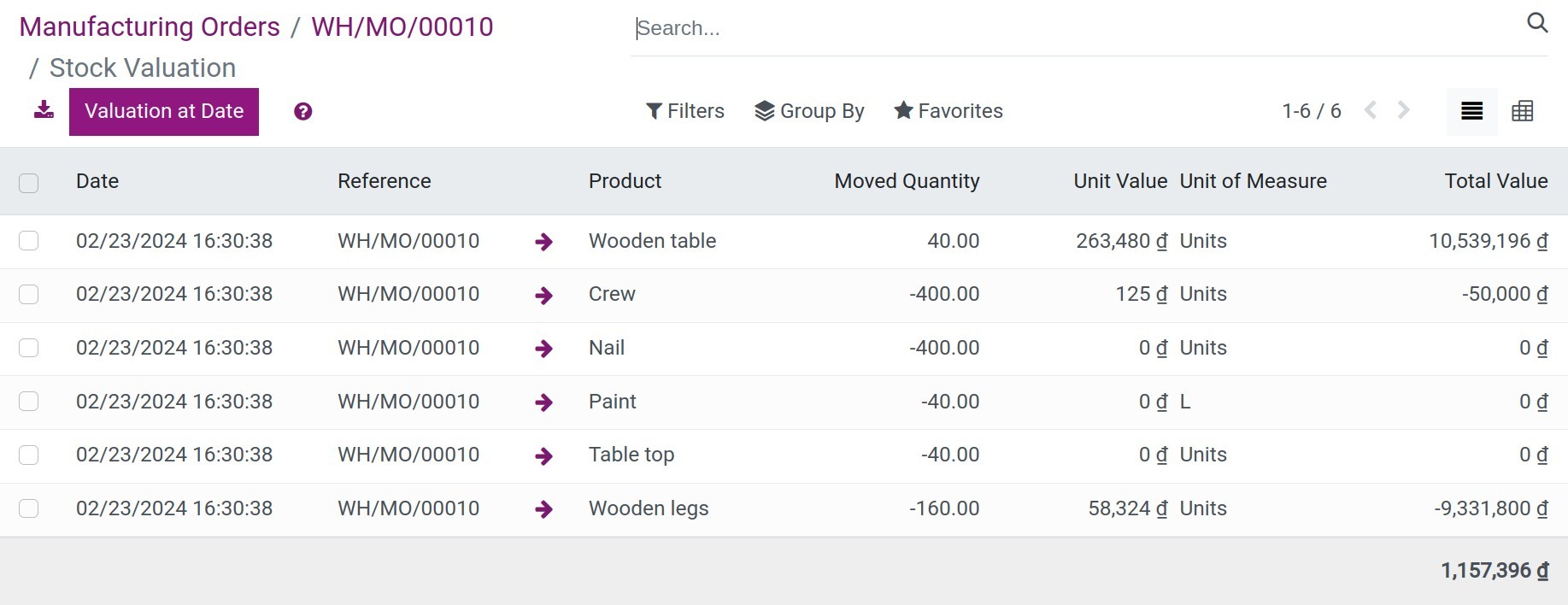
Cost Analysis: Record the manufacturing cost of this manufacturing order.
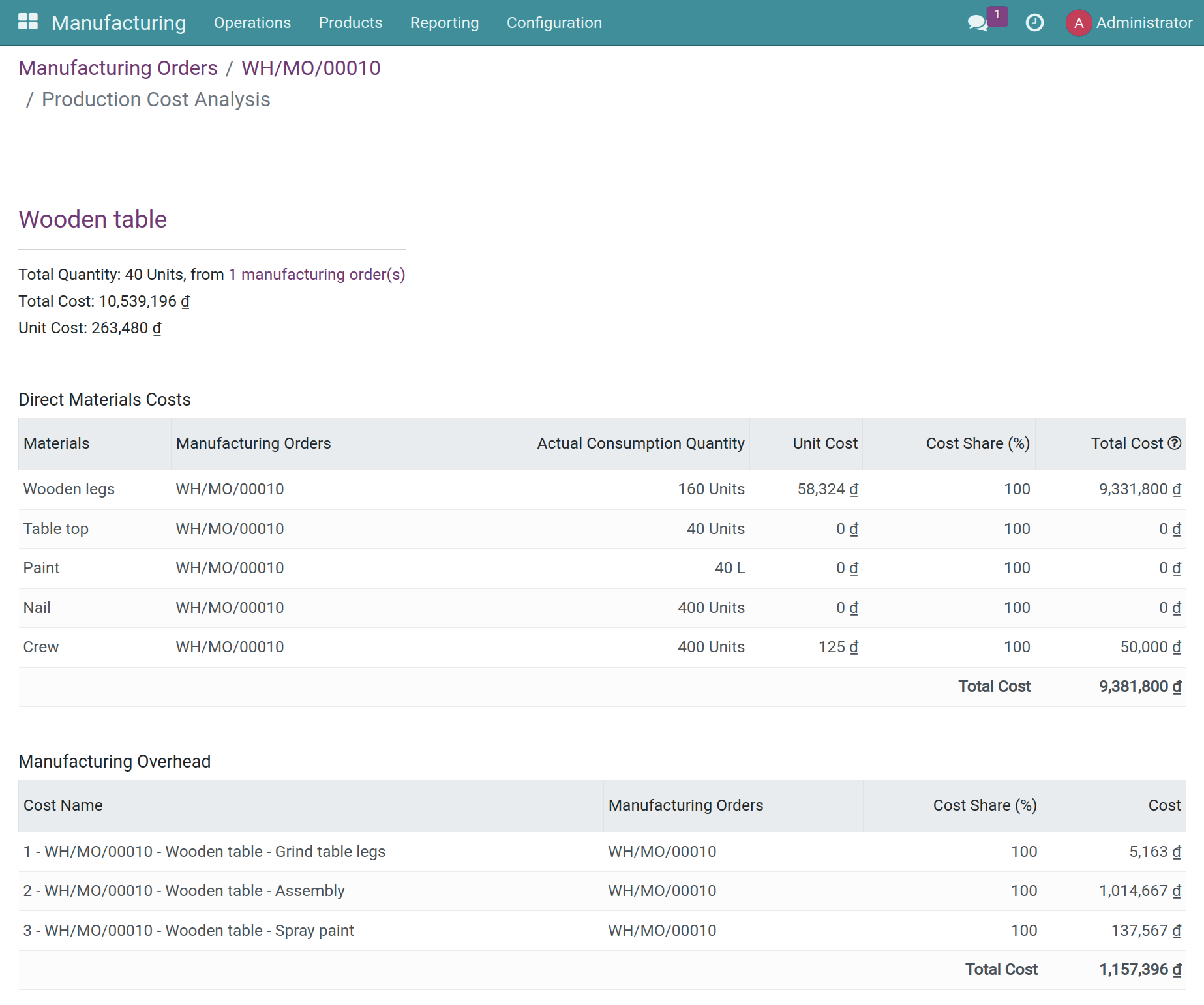
See also
Related article
Optional module