Manage Manufacturing process in Viindoo¶
With highly automated production processes, managing the manufacturing operations and capacity is essential. Viindoo All-in-one Enterprise Management Solutions provides you with the tools for these manufacturing activities management.
Configuration¶
To utilize the feature, you navigate to Manufacturing ‣ Configuration ‣ Settings, active the Work Orders feature.
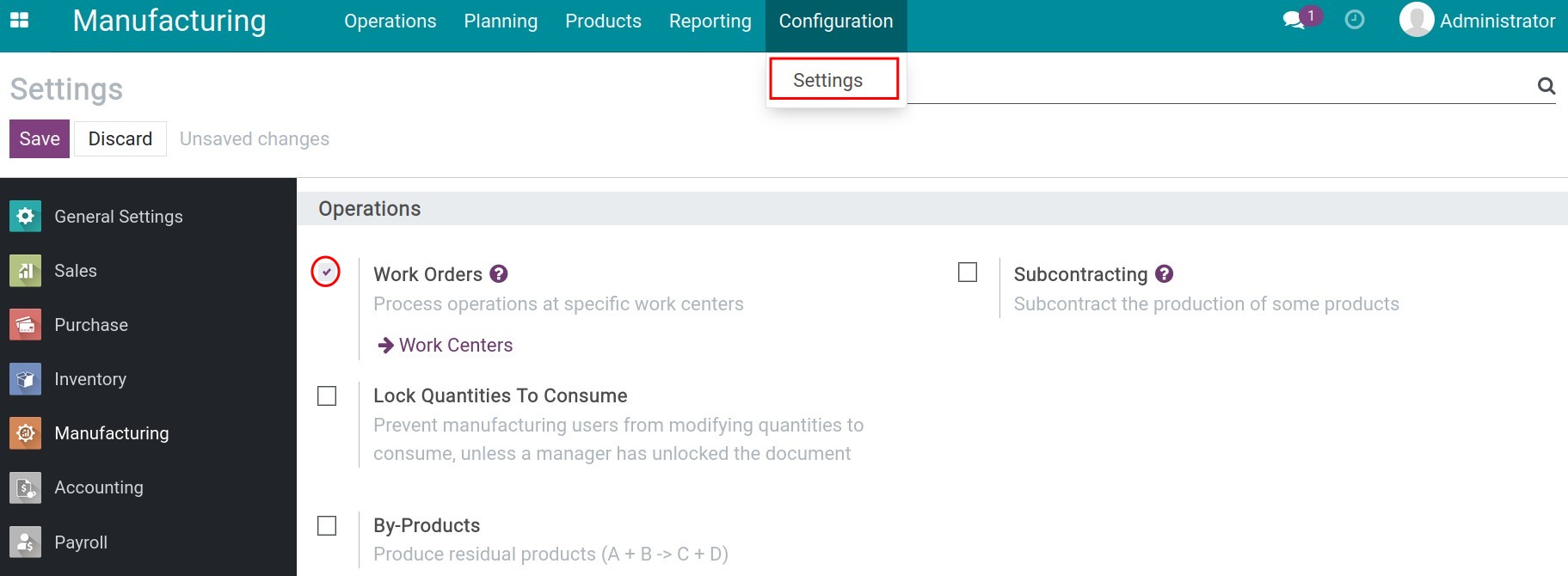
Click on Save to complete the feature activation.
Implement Manufacturing process¶
Let’s take a look at the following example to see how work centers and work orders are applied to the process of manufacturing Table:
Work Centers
Assembly team: 10 person
Time Efficiency: 100%;
OEE Target: 90%;
Regulated working time: 40 hours/week, 8 hours/day;
Cost per hour: 500.000 VND/hour.
Spray paint team: 3 persons
Time Efficiency: 100%;
OEE Target: 90%;
Regulated working time: 40 hours/week, 8 hours/day;
Cost per hour: 300.000 VND/hour.
Operations
Spray paint operation:
Time: Time: On average, it takes 30 minutes for 01 person to spay paint a table.
Assembly operation (this operation will be operate after Spray paint operation):
Time: On average, it takes 15 minutes for 01 person to assemble a table.
Bills of Material for Table:
Table top: 1 unit;
Table legs: 4 units;
Nail: 10 units;
Screw: 12 units;
Spray Paint (Pink): 0,1 liter.
Configure Work Centers¶
To create 2 work centers Assembly and Spray paint team, you go to Manufacturing ‣ Configuration ‣ Work Centers, click onting Create to create a new work center:
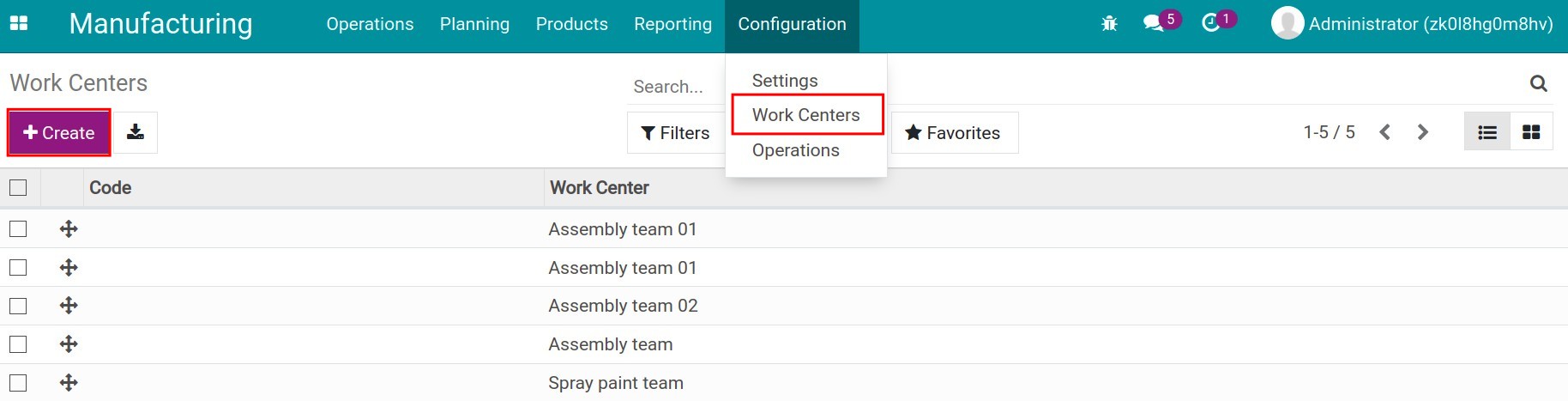
Then, fulfill the information below:
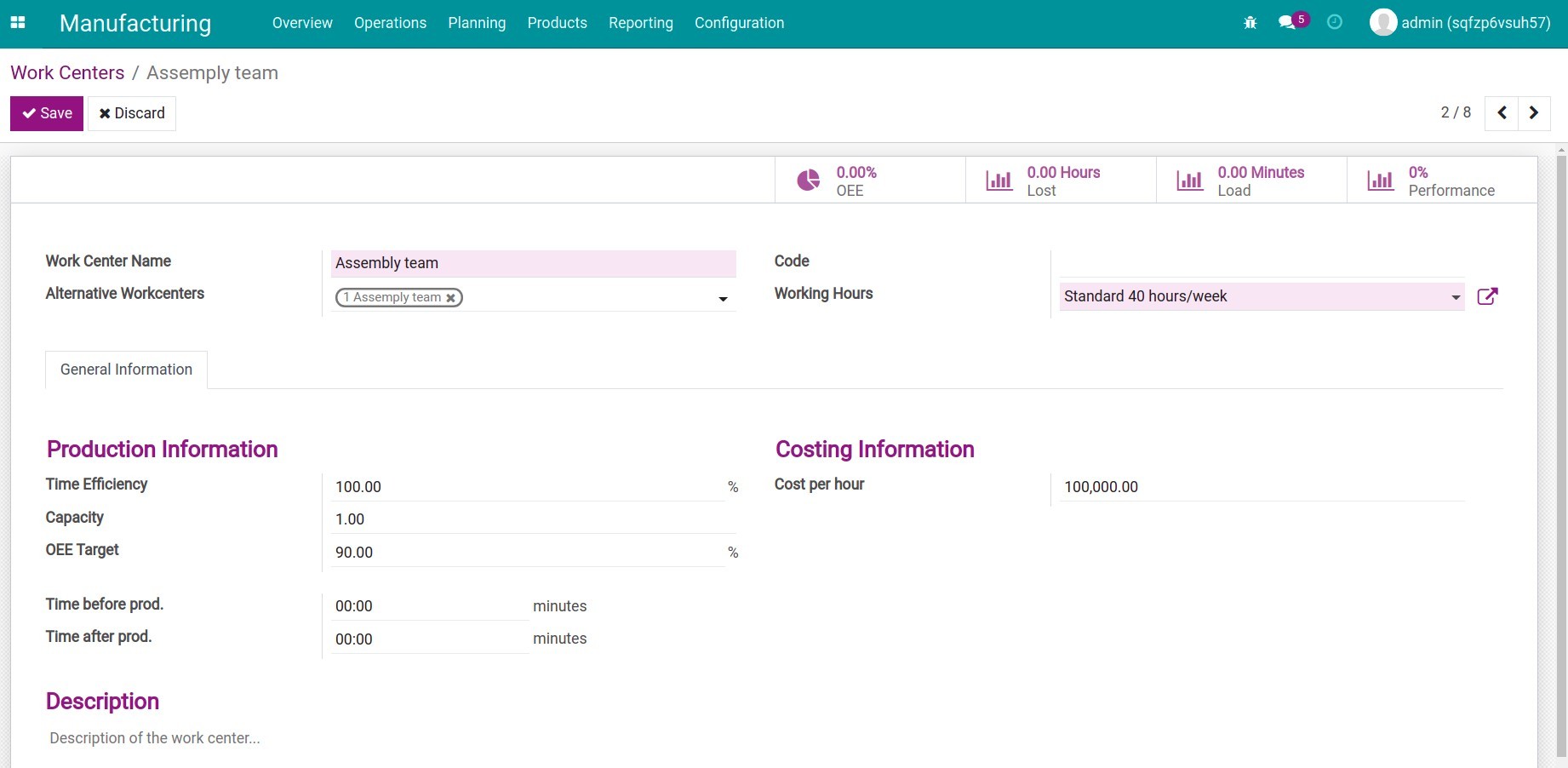
General Information:
Work Center Name: Name of the work center;
Alternative Workcenters: Choose the work center replacing this work center in case it is used to execute other work orders;
Code: Fulfill the code for the above work center;
Working Hours: Select working hours for the work center. The working hours are the foundation to make work orders for the work centers;
Production Information:
Time Efficiency: Time efficiency is calculated by %. The figure is a basis for calculating the expected time of a work order. For example: With a time efficiency of 100%, this work center can manufacture 1 unit of product in 1 hour. If the time efficiency is 200%, it means that 1 unit of product can be manufactured in 30 minutes;
Capacity: The capacity of the work center. It means the number of units that can be produced in parallel from this work center. For example: A employee of the assembly team can assemble 1 desk in 1 hour, but in a team with 10 people working at the same time, the capacity of the team will make 10 working tables in 1 hour;
OEE Target: You can declare metrics to check the Overall Effective Efficiency of the work center is;
Time before producing: Time in minutes for the setup before utilizing the work center such as the preparing or warm up before running;
Time after producing: Essential time in minutes after utilizing the work center such as the cleaning time after utilizing.
Costing Information:
Cost per hour: Cost of the work center per hour.
Description: Fulfill with the detailed description of the work center.
At each work center, you can see the statistical reports as follows:
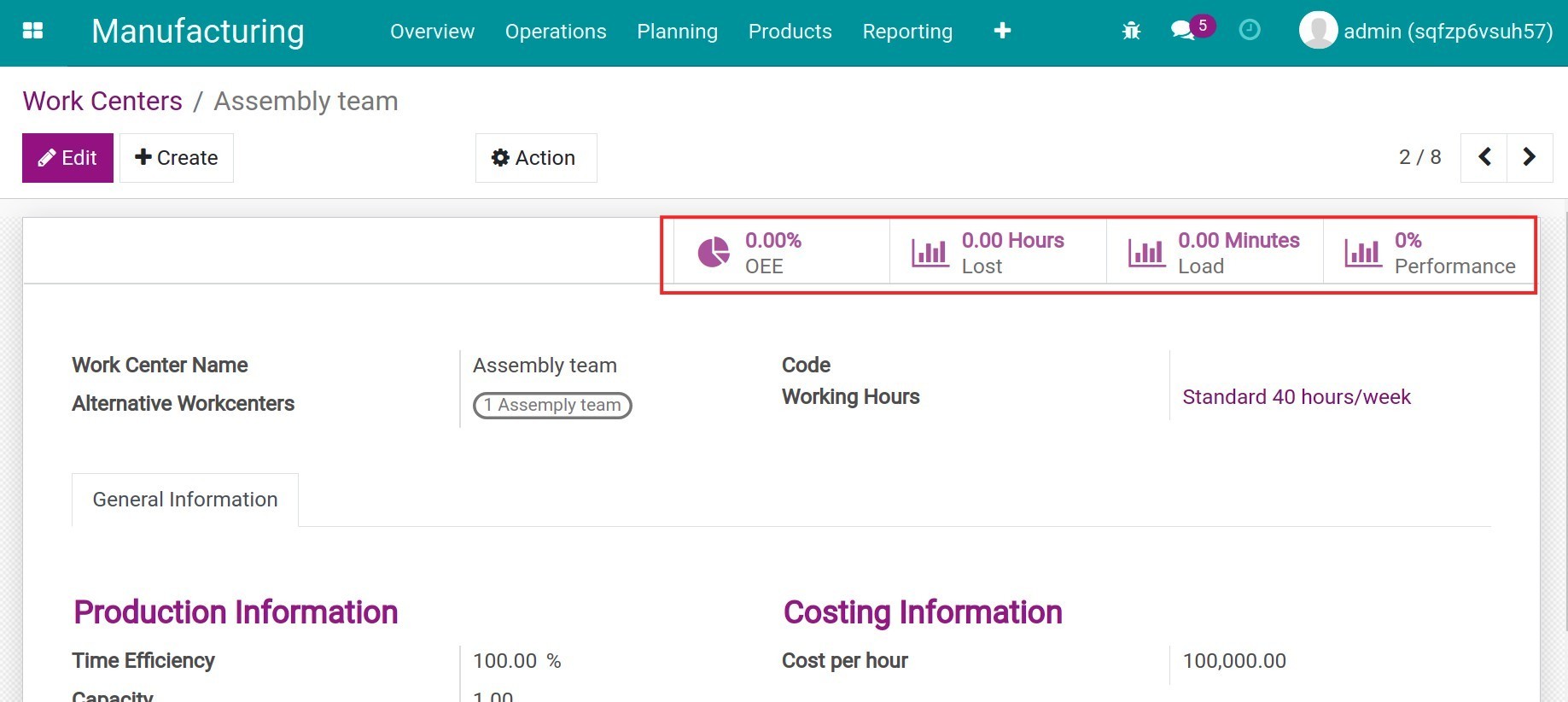
OEE: Performance report of the work center;
Lost: Report of the duration of the performance loss and the reasons for the performance loss during manufacturing execution;
Load: Report of the executed duration of the work center;
Performance: Report about the performance of the work center.
Configure Operations¶
With 2 manufacturing operations as Assembly Table and Spray paint, you navigate to Manufacturing ‣ Configuration ‣ Operations, click onting Create to create an operation.
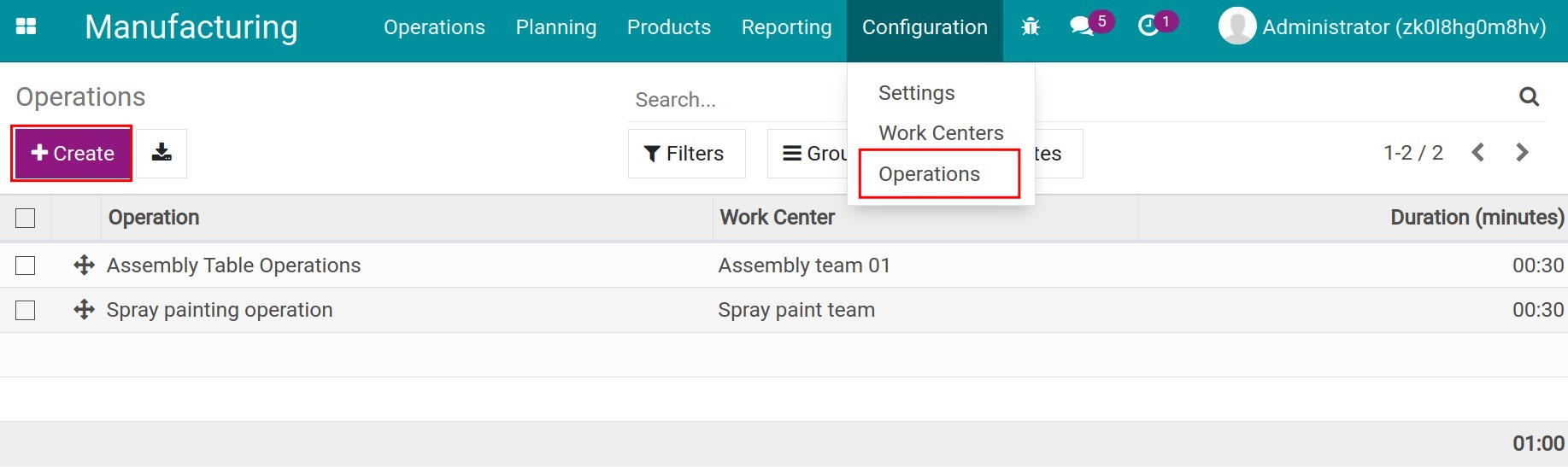
Then, fulfill the information below:
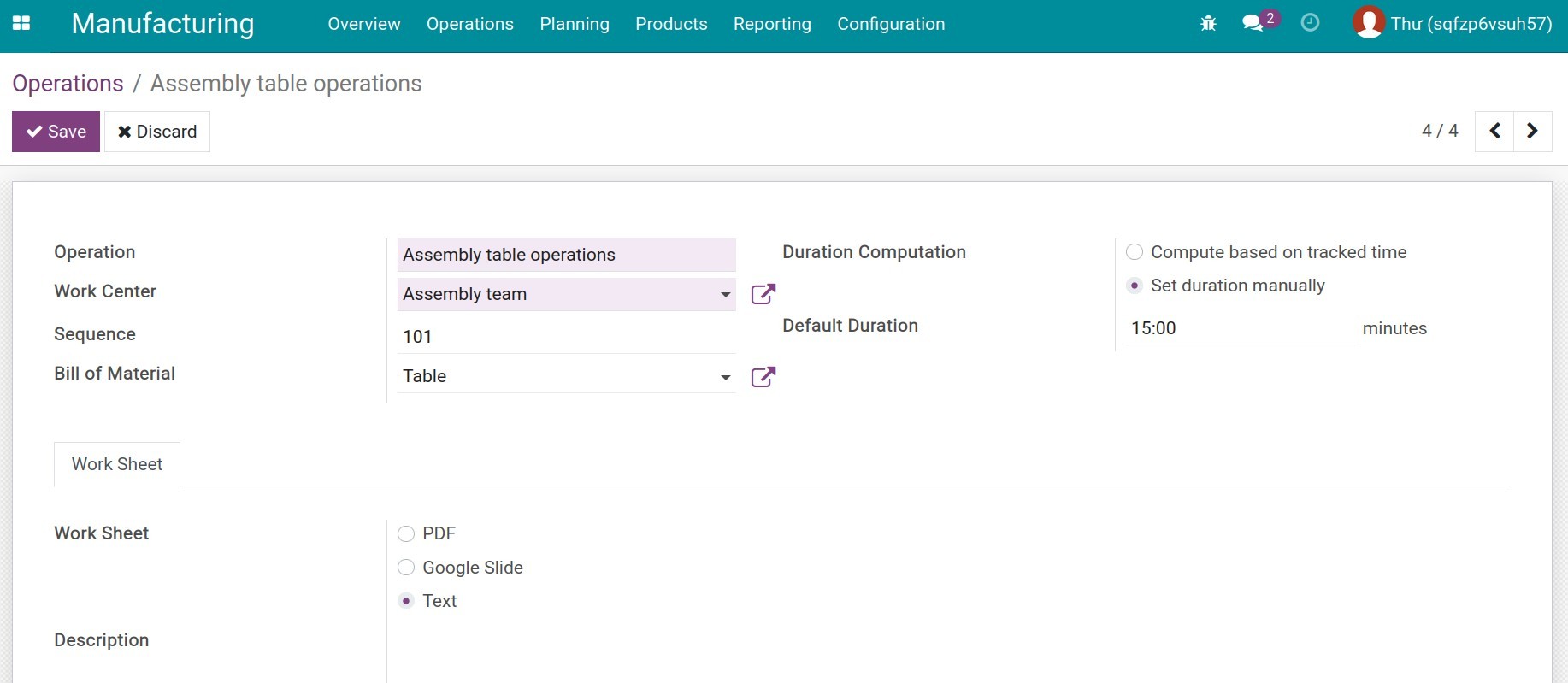
Operation: Name of the manufacturing operation;
Work Center: Select the work centers that execute the manufacturing operation;
Bill of Material: Select the bill of the material linked to the operation;
Duration Computation:
Compute based on tracked time: Compute based on tracked time: If checked, the system will automatically calculate based on the actual time data of the declared number of work orders. For example: You can choose to compute based on the 5 nearest finished worker orders;
Set duration manually: If checked, you will be allowed to set the estimated duration manually for the operation.
Default Duration: Declare the estimated time for this operation. In the above example, it is 15 minutes;
Work Sheet: Select the format of the drawing/instruction file uploaded for the operation;
Description: Fulfill with the detailed description of this operation.
How to apply Work Centers, Operations and Bills of Materials¶
After configuring work centers and operations, navigate to Manufacturing ‣ Products ‣ Bills of Materials, choose the above selected BoM, at the Components, you will see the bills of materials that you configured. To see details, please refer to: How to create bills of materials.
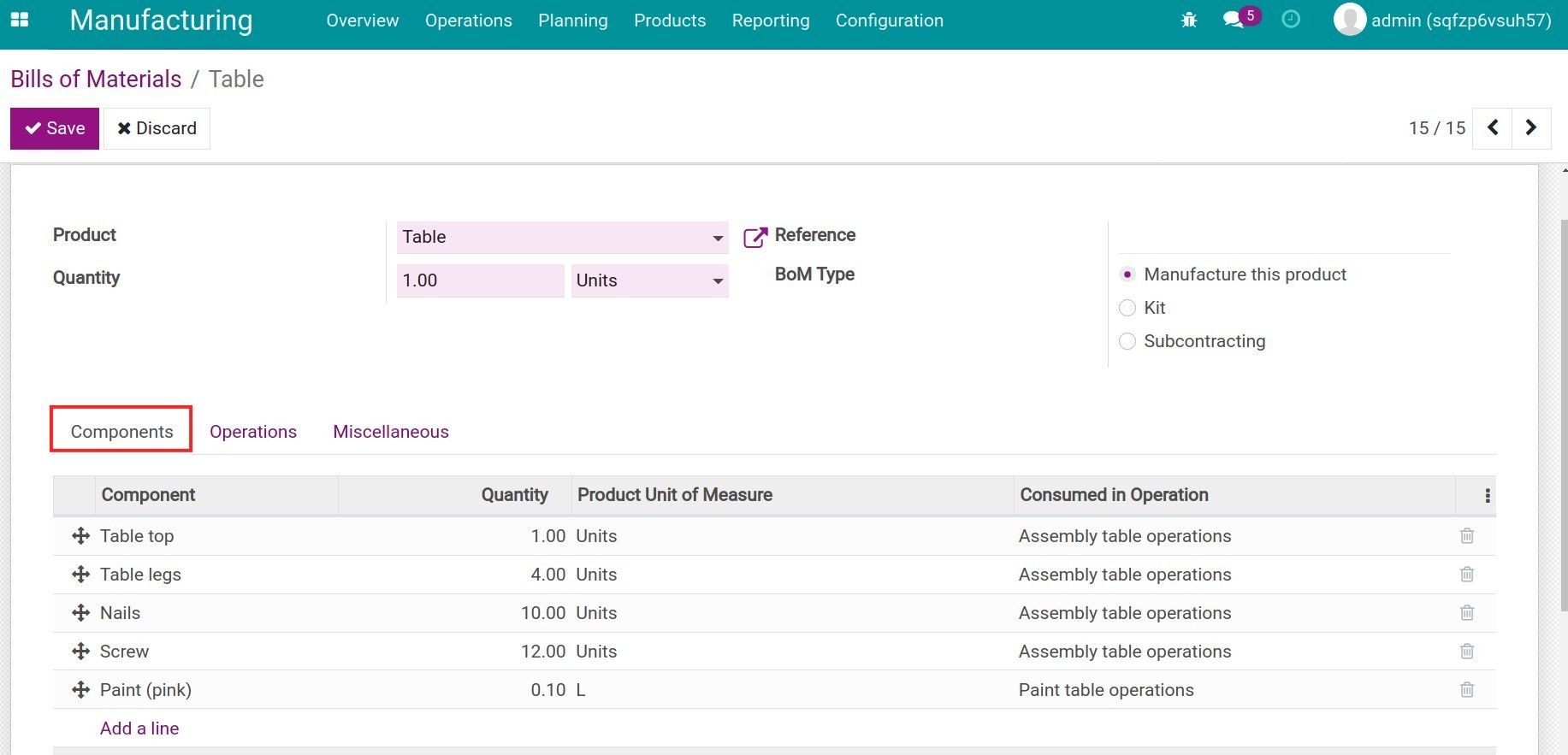
In addition, on the Operations tab, you can see the manufacturing operation where the components of the materials to be consumed.
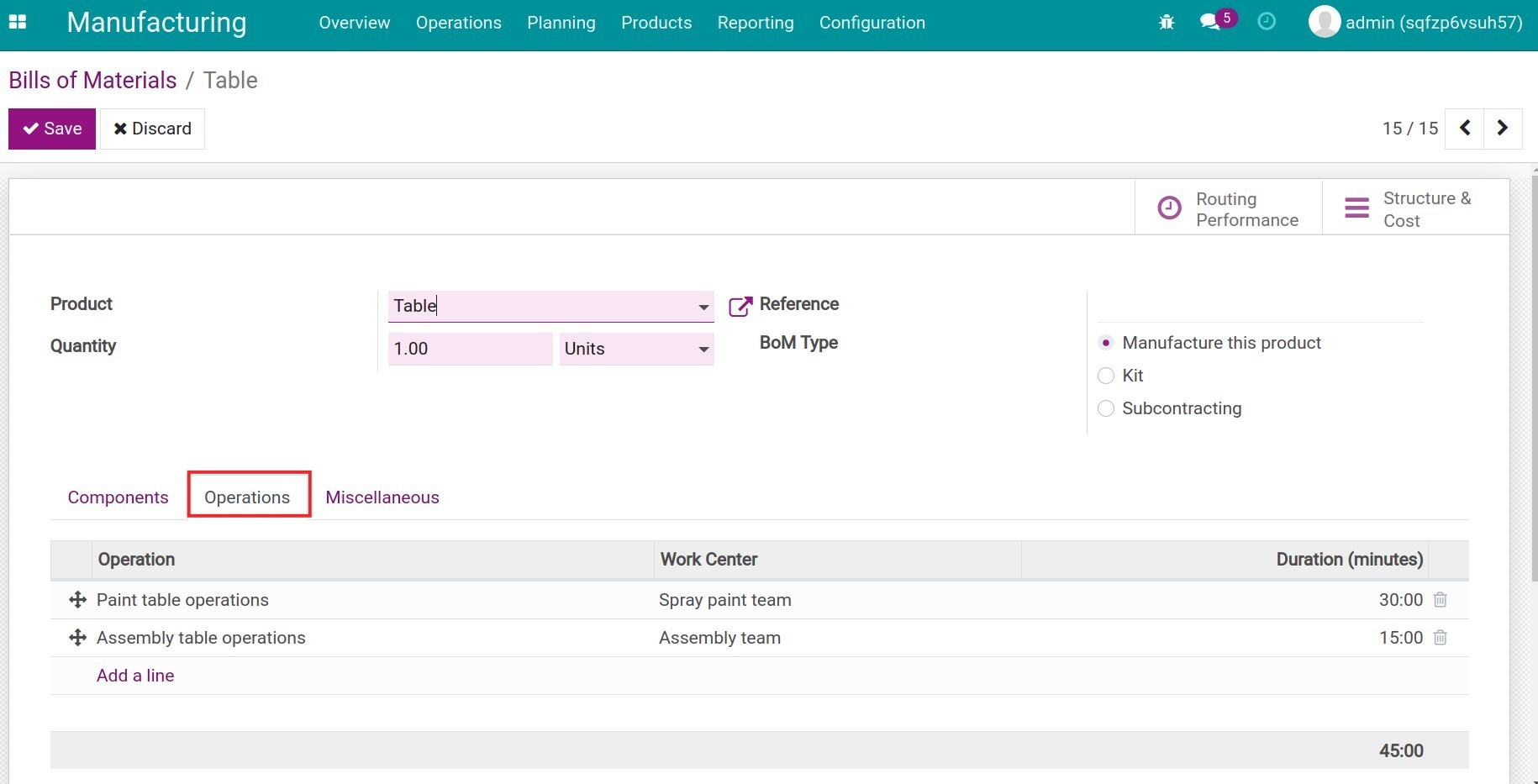
Create the Manufacturing Orders¶
You can navigate to Production ‣ Operations ‣ Manufacturing Orders to create a new manufacturing order for Table:
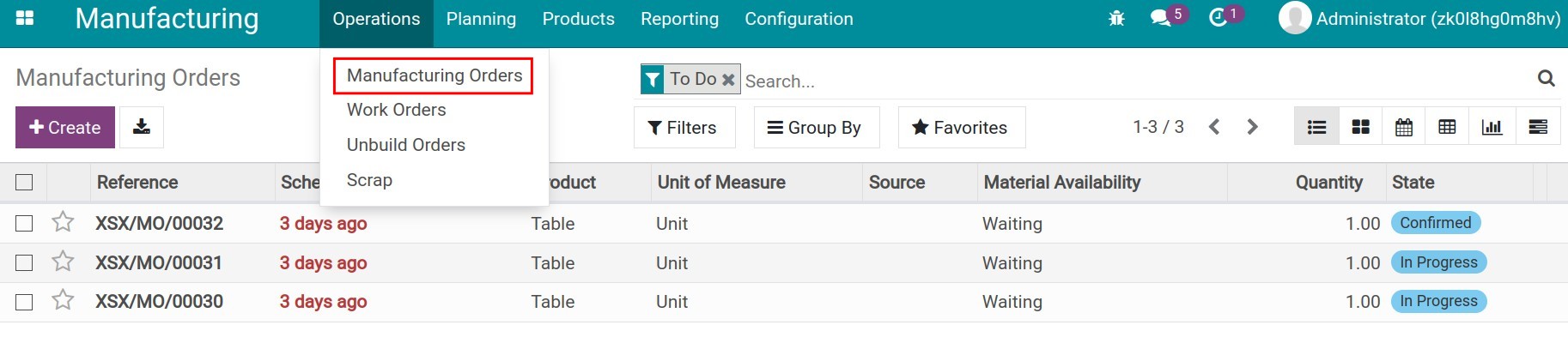
The information to set up the manufacturing order includes:
Product: Choose the product as Table;
Quantity: Fulfill the number of product;
Bill of Material: Select the Bills of materials for the product. When selected, the information of components of bills of materials will be automatically suggested in the Components tab;
Scheduled Date: Scheduled date at which you plan to start the manufacturing operation.
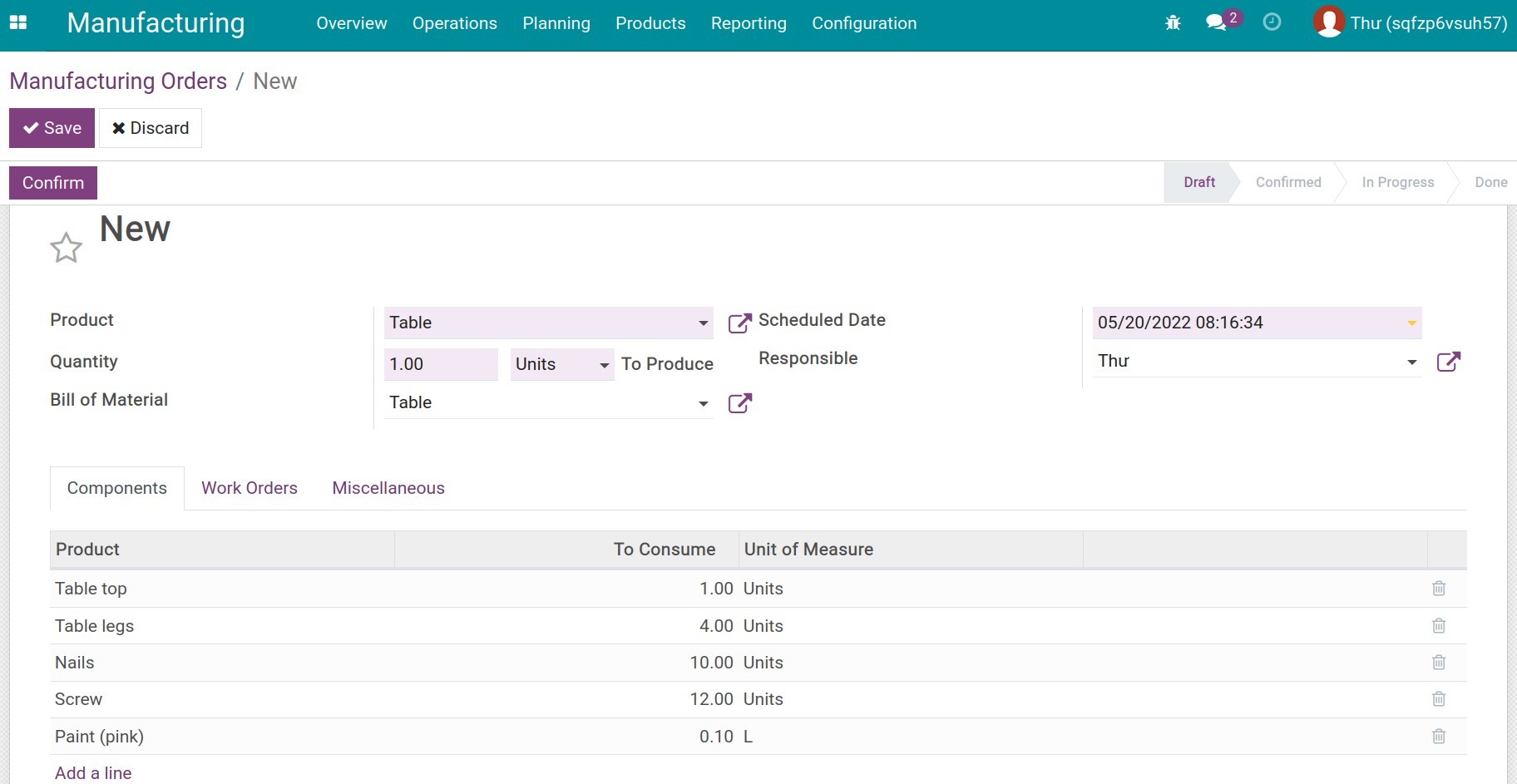
Click on Confirm and Plan for the manufacturing order.
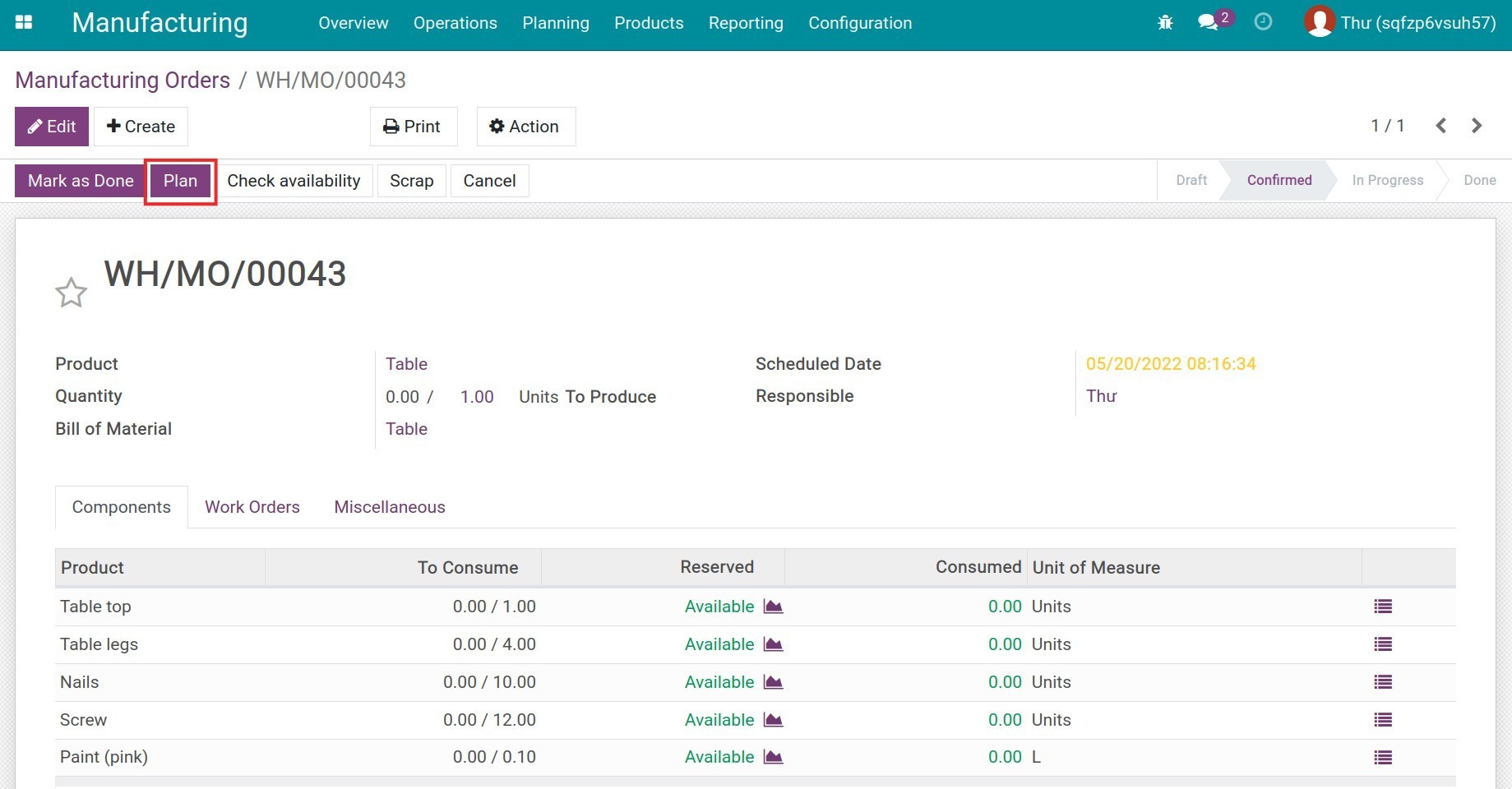
You will then be able to track the status, scheduled start date, expected duration and real duration for each manufacturing operation in the Work Orders tab.
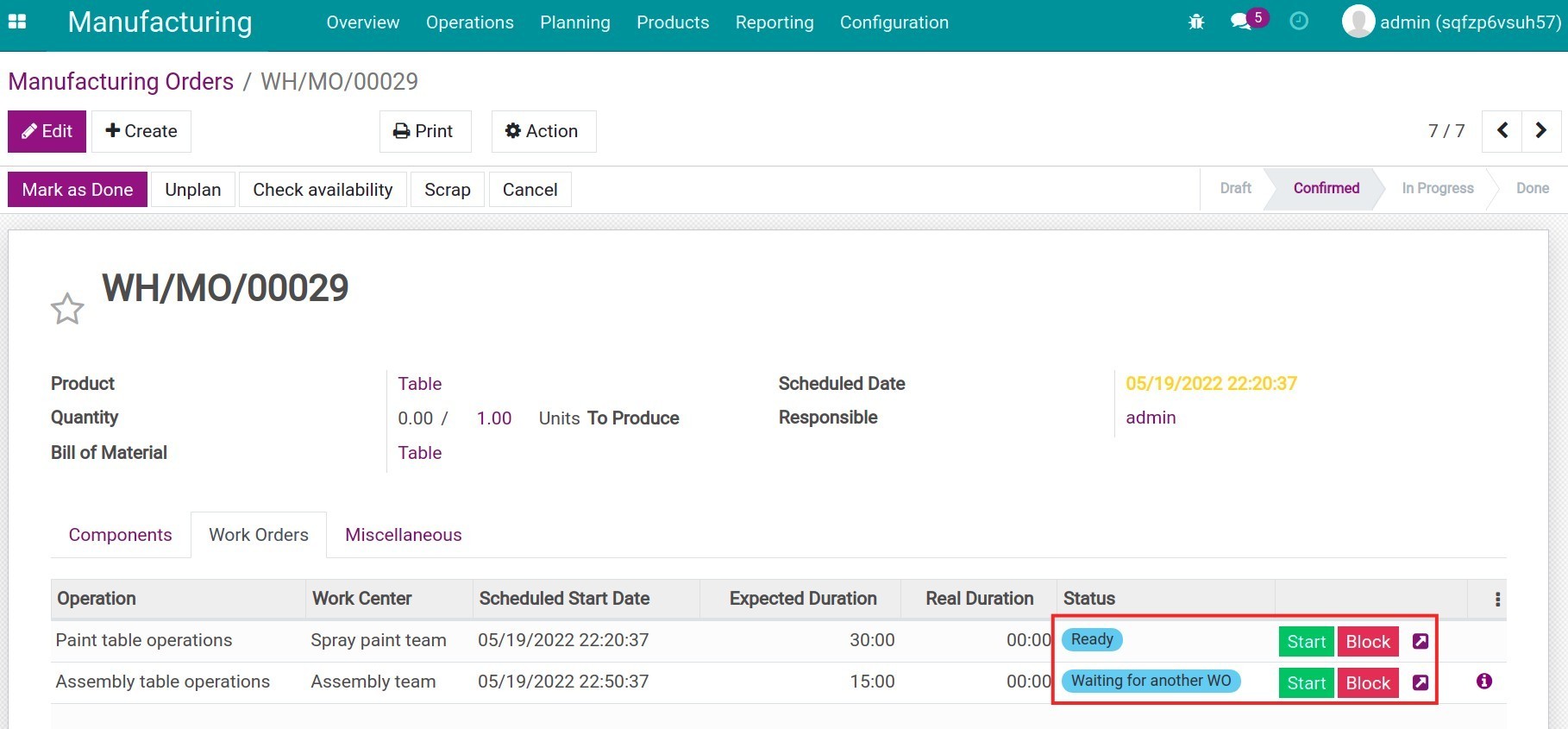
In there:
Click on Start to start the operation;
Click on Pause to pause the operation;
Click on Block if you want to block the operation.
Press Mark as Done after completing the manufacturing operations for Table. Then, on Manufacturing Orders, you can view information about Valuation and Cost Analysis.
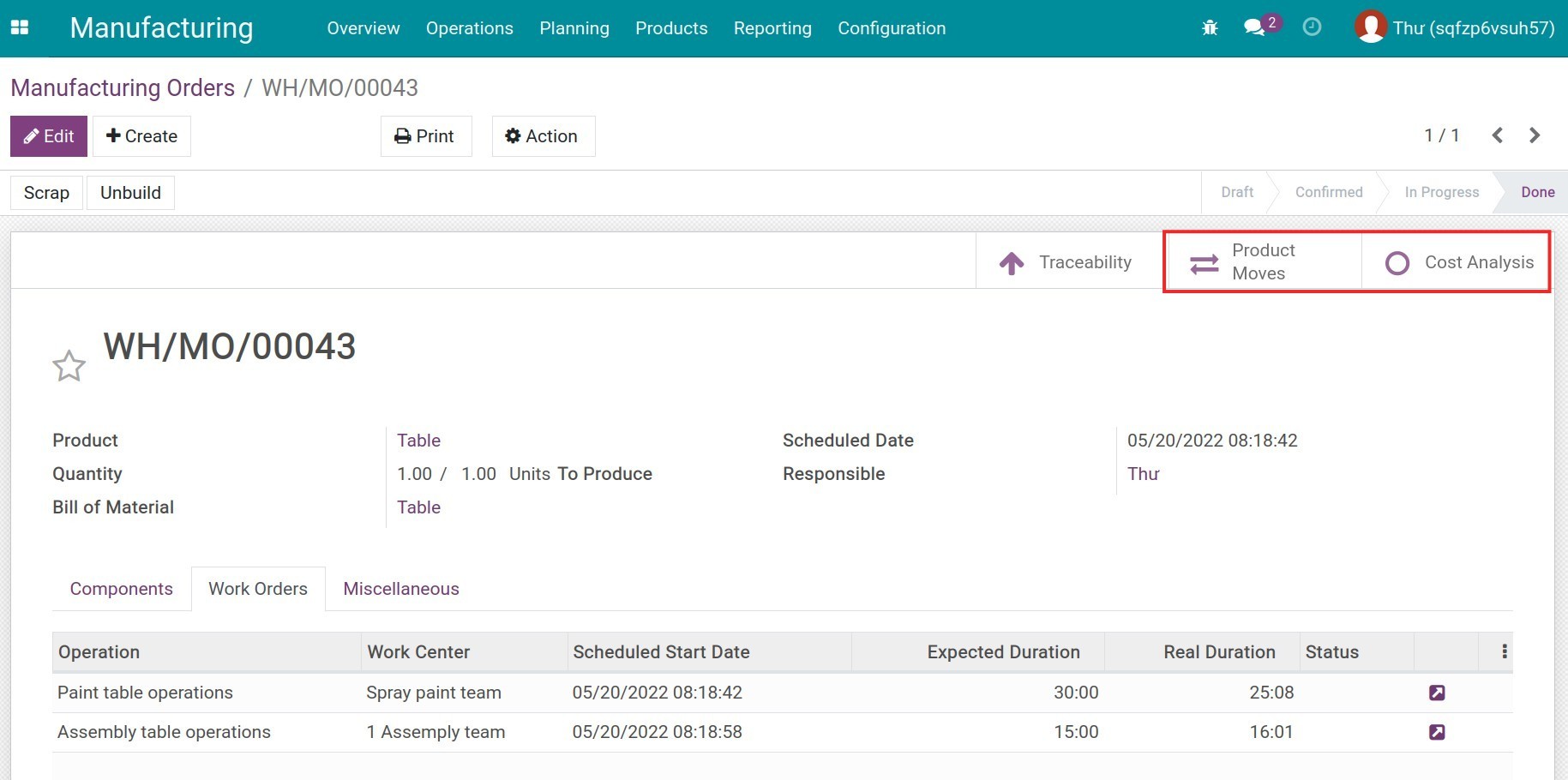
Valuation: Record the quantity and value of components and finished product of manufacturing order.
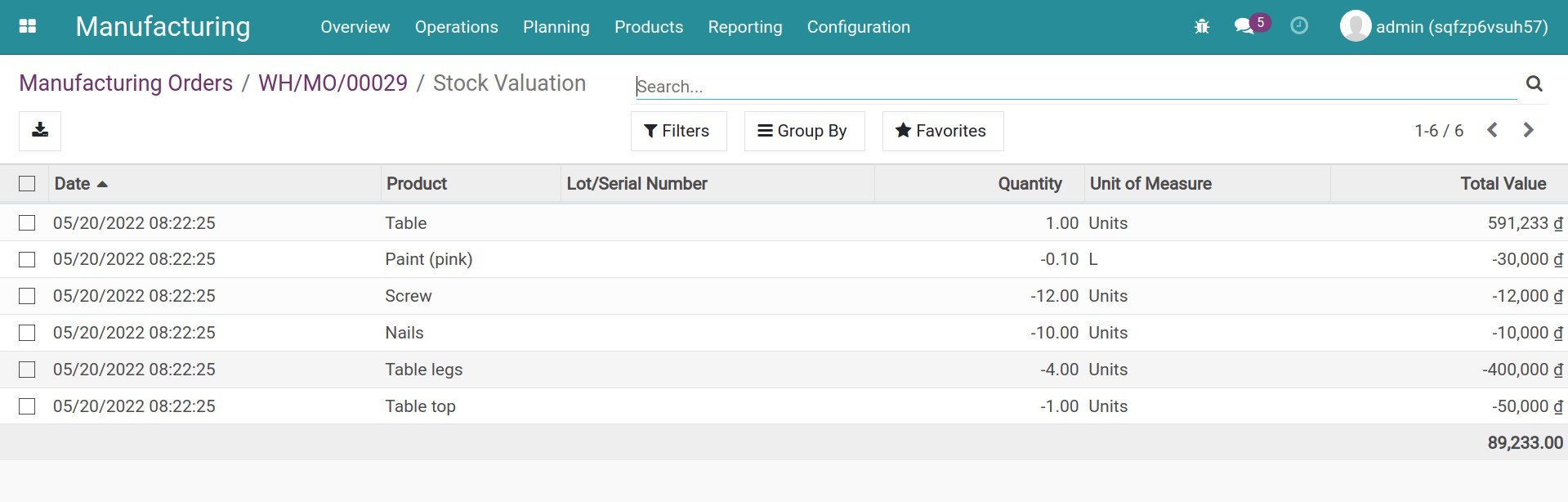
Cost Analysis: Record the manufacturing cost of this manufacturing order.
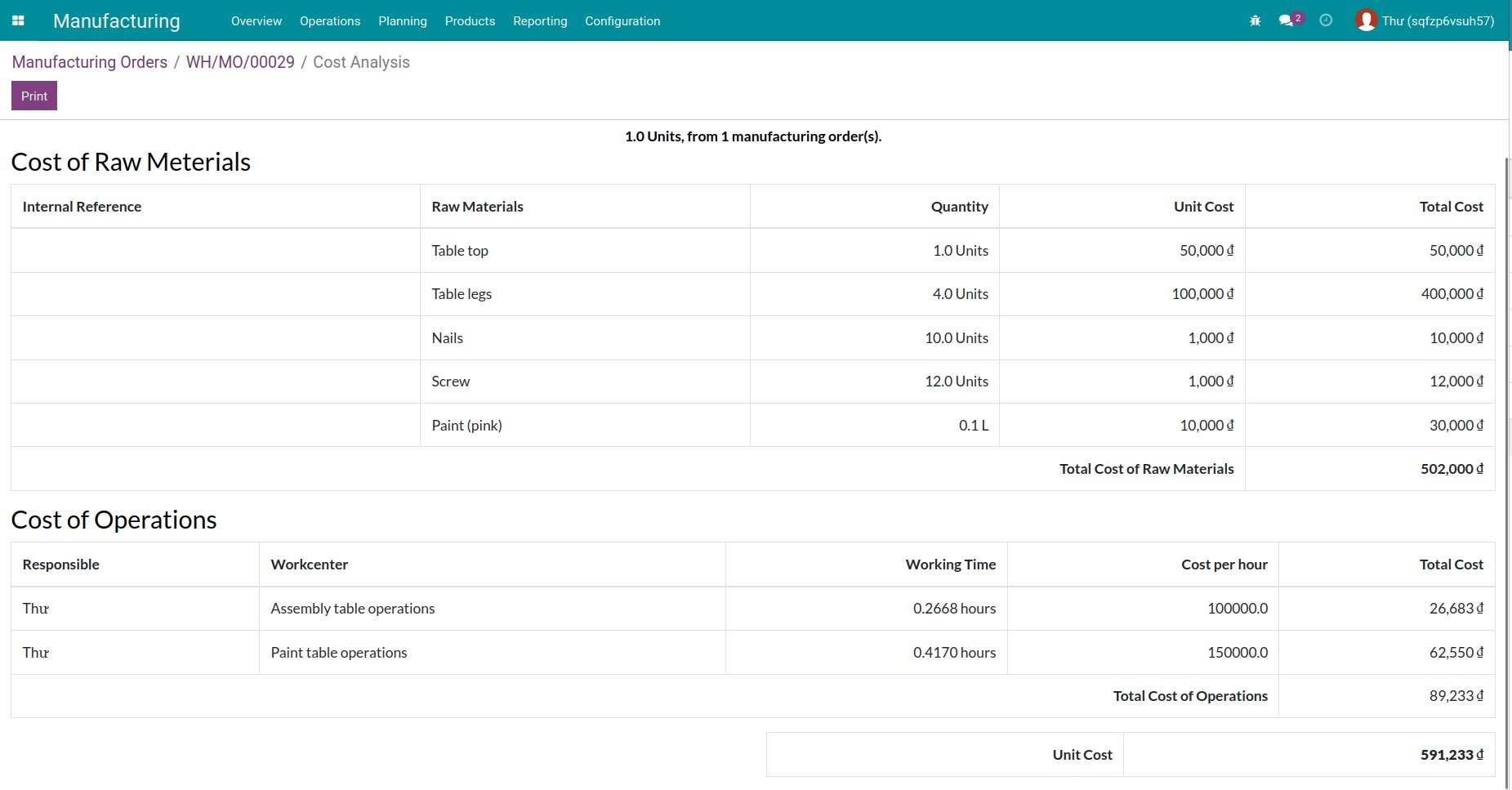