Cross Docking is a logistics technique that helps optimize storage costs and improve the efficiency of warehouse management. So, what are the strengths and weaknesses of this management method? Viindoo Warehouse Software will provide information to help businesses gain a better understanding of the distribution model of Cross Docking goods in this article.
1. What is Cross Docking ?
There are four main functions in the warehouse management series: receiving, storing, collecting packages, and transporting goods to partners. Among these, the two functions that consume a significant amount of time, labor, and management costs are storage and package collection.
So, what is Cross Docking? Cross docking is a technique used to eliminate the need for storage and package collection, while still enabling normal receiving and transportation functions. In other words, the goods will be transferred directly from the manufacturer or supplier to the place of consumption without the need to pass through a warehouse.
With Cross Docking, businesses will need a gathering place, but it is not primarily used for storage.
Instead, items from different suppliers are placed in a consolidation station. In this area, the products are classified, gathered, and arranged into output vehicles. The vehicles will depart from the docking classification station and be delivered to each customer.
The entire process typically takes no more than one day, ensuring that the goods are always available for sale. The warehouse serves as a sorting area rather than simply a storage facility. Sometimes, the goods are stored for less than an hour before being distributed to consumers.
Cross docking is widely used in various aspects of the logistics industry, including manufacturing, distribution, and transportation. This model is commonly utilized in production activities to collect components or spare parts from different suppliers, helping to ensure timely maintenance of operations.

Cross docking technique is applied to minimize management costs.
Cross docking is classified as follows:
- Manufacturing Cross Docking: Support and integrate input goods supply sources to support JIT (the right product - the right quantity - at the right place - at the right time) in the production process. For example, a machine assembly factory could rent a nearby warehouse to collect and categorize input materials. After gathering all the necessary parts, the system will prepare for the assembly process based on the requirements of each planned part. Therefore, the factory does not need to maintain a large amount of backup inventory.
- Distributor Cross Docking: This is a supportive activity that involves collecting goods from various sources. After receiving the final shipment, the goods are consolidated onto the same pallet before being delivered to customers. For example, distributor A can search for various sources of machinery components without having to worry about quality assurance. Then deliver the necessary requirements to customers.

Companies of all sizes can use Cross Docking
- Transportation Cross Docking: Collecting and combining multiple shipments from various carriers according to the LTL model (Less Than Truckload - transporting retail products by truck) or small batches, in order to take advantage of economies of scale.
- Retail Cross Docking: The distributor will import products from many different suppliers and transport them to retail businesses in the market. For example, Distributor A can import consumer goods from multiple suppliers and then distribute the goods to mini supermarkets or retail grocery stores.
- Opportunistic Cross Docking: This activity can be implemented in any warehouse. The distributor can transport goods from the point of origin to the customer's specified delivery location to fulfill an order.
>>>> See more: What is Just In Time ? Conditions and principles for applying JIT.
2. How is Cross Docking different from traditional warehouse management?
In a traditional warehouse model, the warehouses have to maintain the quantity of goods until customer orders appear. Then, the products in the warehouse will be selected according to the requirements, packaged, and transported to the delivery location.
When new orders are added to the storage warehouse by the companies, the entire quantity of those orders will have to be transferred to the warehouse and kept there until specific customer recipients are identified before being shipped out.
In the case of the Cross Docking model, goods will not be stored in the warehouse but will be immediately transferred to the recipient's location. If the Cross Docking model is implemented correctly, businesses can significantly reduce costs related to warehousing and transportation in their operations.
>>>> Find out: 10 effective and scientific warehouse management for businesses
3. Advantages and disadvantages of Cross Docking
It is not by chance that many businesses apply the Cross Docking model in managing warehouse production. Here are some prominent benefits of this model:
- Firstly: In some cases, wastage is determined by retailers to be associated with holding inventory for high-demand and stable goods. Therefore, Cross Docking is seen as a way to reduce inventory holding costs.
- Secondly: For some retailers or specialized small cargo transporters, Cross Docking is seen as a way to reduce transportation costs. For example, retail stores may incur high costs when using small cargo transportation services. However, with Cross Docking, small shipments are consolidated into full truckloads, reducing inbound transportation costs and simplifying the process of receiving goods at retail stores.
- Thirdly : Products in the fast supply chain are quickly circulated because there is less inventory being held in the warehouse. Businesses can also reduce concerns about inventory checks or storage.
- Fourthly: The cost of handling is lower because there is no need to reserve a lot of goods and release inventory in the warehouse.
Although there are many advantages, there are also many difficulties associated with using this model. Businesses should carefully consider the following disadvantages of Cross Docking before choosing to use this model:
- Time-consuming: If the management and supervision do not ensure an efficient operation process, the Cross Docking model will consume a lot of time for the business if there are any disruptions during transportation. This requires good management skills and technological support from the business.
- Large investment capital is needed: Companies can only save costs after this management model operates smoothly. But at the beginning, businesses will face difficulties in establishing a smooth and error-free operational structure for goods.

The disadvantage of the Cross Docking management model makes businesses hesitate
- Being dependent on suppliers: If there are continuous issues in the process of receiving goods due to delays or errors from the supplier, the business will lose a lot of time and experience delayed deliveries. This causes many businesses to operate at a loss and lose credibility with their partners.
- Transportation issue: Cross Docking mainly relies on road transportation, so the transportation costs can be higher. In addition, the goods consolidation location needs to have a spacious outdoor area for the staff to move the goods.
4. Suitable Products for Cross Docking
In order to utilize the Cross Docking model, a company's products need to meet two requirements: low variability and high volume. If these requirements are not met, the company should not risk choosing this method as it may disrupt the balance between supply and demand, between suppliers and customers. Some suitable products may include:
- The product is fragile and needs to be transported immediately upon arrival at the transfer point.
- The product does not require inspection during the receiving process.
- The products are equipped with barcodes, RFID, ready to be sold to consumers.
- The advertised items have been introduced to the consumer market.
- Retail products have stable quality and quantity to meet customer demand in the market.
- The orders are directly selected from customers, already packaged from the factory (always ensuring the product's condition) and only need to be transported.
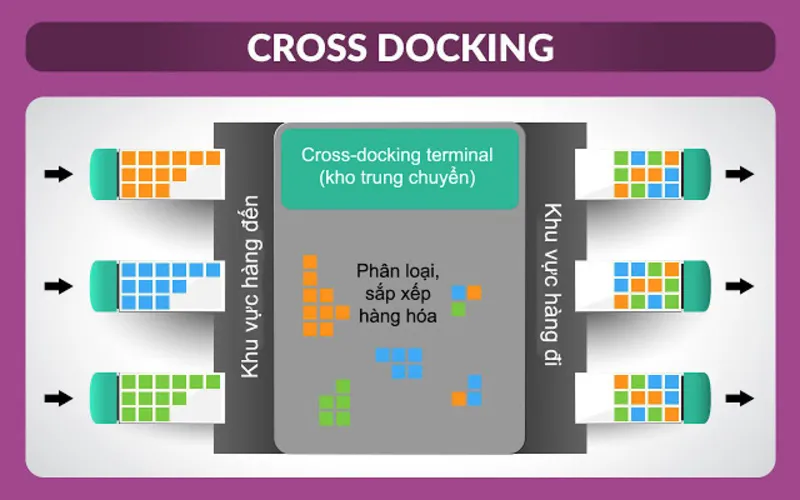
The general model of the Cross Docking warehouse management method
>>>> Read more: Stock Count
- Excel method, process and sample
5. Example of Walmart's Cross Docking
Walmart's success in implementing Cross Docking is a classic example in the logistics industry. Walmart has been implementing this strategy for over 40 years, which helps the company save handling and operational costs, significantly reduce inventory, and most importantly, reach customers directly without intermediaries.
The business strategy of this company is to become a low-cost retailer through the advantage of low costs. All price-conscious consumers trust and remain loyal to the market created by Walmart. Walmart's Cross Docking has helped minimize costs in warehouse and product distribution.

Walmart - The company applies the most successful cross docking model
The product, after being manufactured and packaged at the factory, will be directly transported to Walmart's own warehouse and immediately divided into smaller batches for distribution to other units.
In addition, Walmart has established long-term partnerships with major brands to import large quantities of goods and enjoy discounted benefits. As a result, consumers have more trust in the quality of the products. Combined with transportation advantages, Walmart's 160 distribution centers are built to provide continuous and long-term supply cycles across the United States.
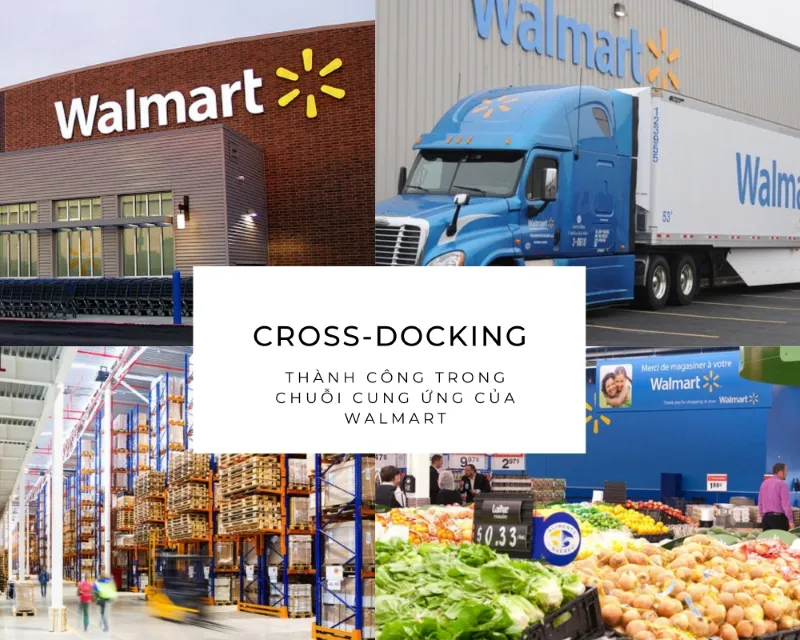
The supply chain model applies Walmart's Cross Docking strategy
This large company also uses advanced technologies such as EDI, CPFR to speed up the process of receiving and transporting goods. The large parallel processing system helps Walmart's staff in managing and distributing to track inventory levels, reserve goods at distribution centers and stores to consolidate goods and deliver them on time, meeting consumer demand effectively.
>>>> Can't miss:
Effective finished goods inventory process for businesses
6. Using Cross Docking with Viindoo
6.1 Managing the Goods Consolidation Point
The goods consolidation point is not a storage area. In fact, it is a temporary location/area for consolidating goods before delivery to customers.
Viindoo Inventory support helps businesses organize their locations for efficient goods collection and reduce inventory levels by eliminating storage. Businesses can set up collection points in the same location without needing to establish multiple warehouses with intricate inventory management processes. As a result, businesses can make more frequent deliveries and enhance relationships with partners in the supply chain.
6.2 Tracking the movement of goods
In inventory management, we are also very familiar with Lavoisier's principle "Nothing lost, everything changed." This means that "All products and goods do not naturally appear and disappear, but only move from one location to another."
Viindoo has applied this principle to develop the Viindoo Inventory warehouse management software. The software helps record the source and destination locations for transfer transactions, details of quantities, exchange history, transaction times, responsible personnel... providing strong support for inventory checking, stocktaking, and traceability to the ultimate source. As a result, controlling the flow of goods using the Cross Docking method becomes easier.
6.3 Controlling the quantity of goods at the Docking sorting stations
In fact, in the Cross Docking model, there is no warehouse to manage the consolidation of goods before delivery to customers. The location could be a consolidation station or a very large container to consolidate, sort, and deliver goods quickly to customers without any storage costs. However, it is also very difficult for businesses to control the goods at these Docking consolidation locations.
However, with Viindoo, products operating on the Cross Dock line can completely control the quantity of goods entering and leaving.
Discover Viindoo Inventory Software
The All-in-one Inventory Software for SMEs. Automate your inventory process leading to increased efficiency, accuracy, and ultimately, cost savings.
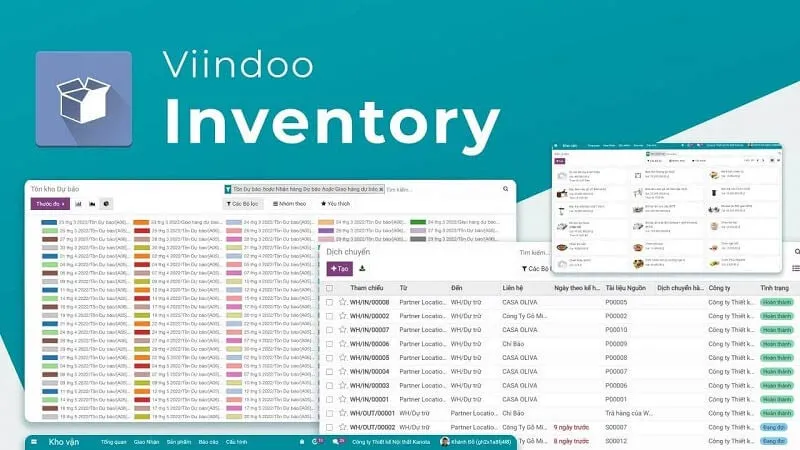
Here is the information about Cross Docking shared by Viindoo. Through the presented benefits, businesses should seize the opportunity to implement this logistics model to ensure the quality and timeliness of goods transportation. Contact Viindoo now to experience more effective business management solutions in the future.
>>>> Continue With: