Overall Equipment Effectiveness (OEE) stands as a pivotal metric in today's fiercely competitive manufacturing sector, where attaining optimal operational efficiency is not merely a goal but a requisite for enduring and expanding. It plays an essential role in measuring the productivity of manufacturing processes.
Definition of OEE and its Importance in Manufacturing
Overall Equipment Effectiveness (OEE) is a comprehensive metric used to evaluate how effectively a manufacturing operation utilizes its resources, specifically focusing on three critical aspects of production: equipment availability, performance, and quality. It is expressed as a percentage, where 100% represents perfect production with only good parts produced (Quality), as fast as possible (Performance), and without any stop time (Availability).
The significance of OEE in manufacturing cannot be overstated. It acts as a vital indicator of production efficiency, pinpointing areas of waste and loss that, when addressed, can lead to significant improvements in productivity and profitability. By providing a clear and quantifiable measure of production effectiveness, OEE helps manufacturers to:
- Identify potential areas for improvement in their production processes.
- Benchmark performance against industry standards or internal goals.
- Optimize the use of existing equipment and resources, reducing the need for additional capital investment.
- Enhance the capacity to meet customer demand with higher quality and in shorter lead times.
Brief Overview of the Three OEE Factors: Availability, Performance, and Quality
At the core of the OEE metric are three fundamental factors that provide insights into different dimensions of production efficiency:
- Availability measures the proportion of scheduled time that the equipment is available to operate. It takes into account all events that halt production for significant periods, such as machine breakdowns, maintenance, setup, and adjustments, subtracting this downtime from the planned production time.
- Performance evaluates how well the manufacturing process operates when it is running, compared to its maximum speed. This factor considers all elements that prevent the process from achieving its theoretical top speed, including minor stops, idling, and slow cycles, thereby reflecting the speed efficiency of the machinery.
- Quality reflects the share of good parts produced out of the total parts produced, highlighting the effectiveness of the production process in delivering products that meet quality standards. It accounts for parts that require rework or are scrapped due to defects, providing insight into the process's ability to produce goods that meet quality specifications right the first time.
Together, these three factors offer a comprehensive view of manufacturing productivity, enabling managers and operators to drill down into specific areas of loss and inefficiency. By focusing on improving these key areas, businesses can drive significant gains in OEE, leading to enhanced operational performance and competitiveness.
Understanding the Three Pillars of OEE
The Overall Equipment Effectiveness (OEE) framework provides a robust measure of manufacturing productivity by analyzing three critical factors: Availability, Performance, and Quality. Each of these pillars offers insights into different areas of the production process, highlighting potential improvements that can lead to significant efficiency gains.
Availability
Explanation of what Availability measures
OEE Availability is a measure of how often production equipment is ready and available to produce goods versus the time it was scheduled to do so. It essentially captures the ratio of operating time to planned production time, taking into account all the events that prevent the equipment from performing its intended tasks during the scheduled time.
Factors affecting Availability
- Equipment Failures: Unexpected breakdowns are the most straightforward examples of what can reduce availability. These can range from minor issues that are quickly resolved to significant malfunctions requiring extensive repairs.
- Planned Maintenance: Scheduled downtime for preventive maintenance, though necessary for long-term efficiency and reliability, directly impacts availability. The key is to optimize maintenance schedules to minimize their impact on production time.
- Changeovers and Setups: The time taken to switch from producing one product to another, including adjustments to equipment settings and testing before full production resumes, affects availability. Streamlining these processes can significantly improve this metric.
Performance
Understanding Performance in the context of OEE
OEE Performance measures the efficiency of production when the equipment is running, comparing the actual production rate to the maximum possible rate. It reflects the speed at which products are manufactured during available production time, highlighting losses due to inefficiencies in the operation of the machinery.
How minor stops and speed losses impact Performance
- Minor Stops: Short-duration stops for reasons such as jams, misfeeds, or sensor issues. Though brief, their cumulative effect can substantially reduce performance.
- Speed Losses: Occurs when machinery operates below its maximum speed capacity. This can be due to suboptimal machine settings, wear and tear, or the need to run slower to ensure product quality, each contributing to reduced performance.
Quality
The role of Quality in OEE calculation
OEE Quality is the measure of production that meets the required standards without the need for rework or scrapping. It's calculated by dividing the number of good units produced by the total units started. This factor highlights the effectiveness of the manufacturing process in delivering products that meet specifications the first time through.
Impact of rejects, reworks, and defects on Quality score
- Rejects: Products that are discarded because they don't meet the quality standards directly reduce the Quality score, indicating material loss and effort.
- Reworks: The need to reprocess or correct a product consumes additional resources and time, indicating inefficiencies in the initial production process.
- Defects: High defect rates can point to issues in the production process, equipment malfunctions, or material quality, each affecting the overall Quality score.
OEE Formula
Calculating Overall Equipment Effectiveness (OEE) is pivotal for manufacturers seeking to optimize production processes, reduce waste, and enhance product quality. The OEE formula is a multiplication of its three primary factors: Availability, Performance, and Quality, each offering insights into different aspects of production efficiency. Here's a step-by-step guide to calculating OEE, accompanied by examples and tips to avoid common pitfalls.
Step-by-step Guide on OEE Calculator
1. Calculate Availability
- Availability = (Run Time / Planned Production Time)
- Planned Production Time: Total time your production system is scheduled to operate.
- Run Time: Planned Production Time minus Downtime (both planned and unplanned).
2. Calculate Performance
- Performance = (Ideal Cycle Time × Total Count) / Run Time
- Ideal Cycle Time: The shortest time to produce one item.
- Total Count: Total number of items produced during the Run Time.
3. Calculate Quality
- Quality = Good Count / Total Count
- Good Count: Number of defect-free items produced.
4. Calculate OEE
- OEE = Availability × Performance × Quality
- or OEE = (Good Count × Ideal Cycle Time) / Planned Production Time
Examples of OEE Calculation
- Planned Production Time: 8 hours (480 minutes)
- Downtime: 1 hour (60 minutes)
- Run Time: 480 - 60 = 420 minutes
- Total Count: 10,000 pieces
- Ideal Cycle Time: 0.04 minutes (24 seconds)
- Good Count: 9,800 pieces
Availability: 420 / 480 = 0.875 (87.5%)
Performance: (0.04 × 10,000) / 420 = 0.952 (95.2%)
Quality: 9,800 / 10,000 = 0.98 (98%)
OEE: 0.875 × 0.952 × 0.98 = 0.82 (82%)
Common Pitfalls in OEE Calculation and How to Avoid Them
- Overestimating Ideal Cycle Time: Setting an unrealistic Ideal Cycle Time can inflate your Performance factor. Ensure the Ideal Cycle Time is based on the actual capability of your equipment under optimal conditions.
- Ignoring Short Stops: Not accounting for minor stops or slowdowns can give a false sense of high Performance. Record and include all forms of interruptions, no matter how brief, in your calculations.
- Poor Data Quality: Relying on inaccurate or incomplete data can skew OEE calculations. Implement reliable data collection methods and regularly review data for accuracy.
- Focusing Solely on OEE Percentage: While a high OEE score is desirable, understanding the underlying factors (Availability, Performance, Quality) is crucial for targeted improvements. Use OEE as a diagnostic tool, not just a metric.
- Not Benchmarking Against Industry Standards: Without benchmarking, it's challenging to gauge your performance relative to peers. Use industry standards as a guide to set realistic goals for your OEE improvement efforts.
Improving OEE with Lean Manufacturing Principles
Lean Manufacturing is a systematic approach to identifying and eliminating waste through continuous improvement, focusing on enhancing product value with fewer resources. Its principles are highly relevant to improving Overall Equipment Effectiveness (OEE) as they target the root causes of inefficiencies within the production process.
By applying Lean tools and techniques like 5S, Six Sigma, Kanban, etc, manufacturers can significantly boost their OEE scores, leading to improved productivity, reduced costs, and enhanced product quality.
Role of Viindoo Manufacturing Software in Enhancing OEE
Viindoo Manufacturing Software offers a comprehensive suite of tools designed to improve manufacturing efficiency and effectiveness, directly impacting the Overall Equipment Effectiveness (OEE) of production processes.
Through advanced functionalities like real-time data collection, thorough analysis and reporting, and provision of actionable insights, Viindoo becomes an indispensable tool for manufacturers aiming to optimize their operations.
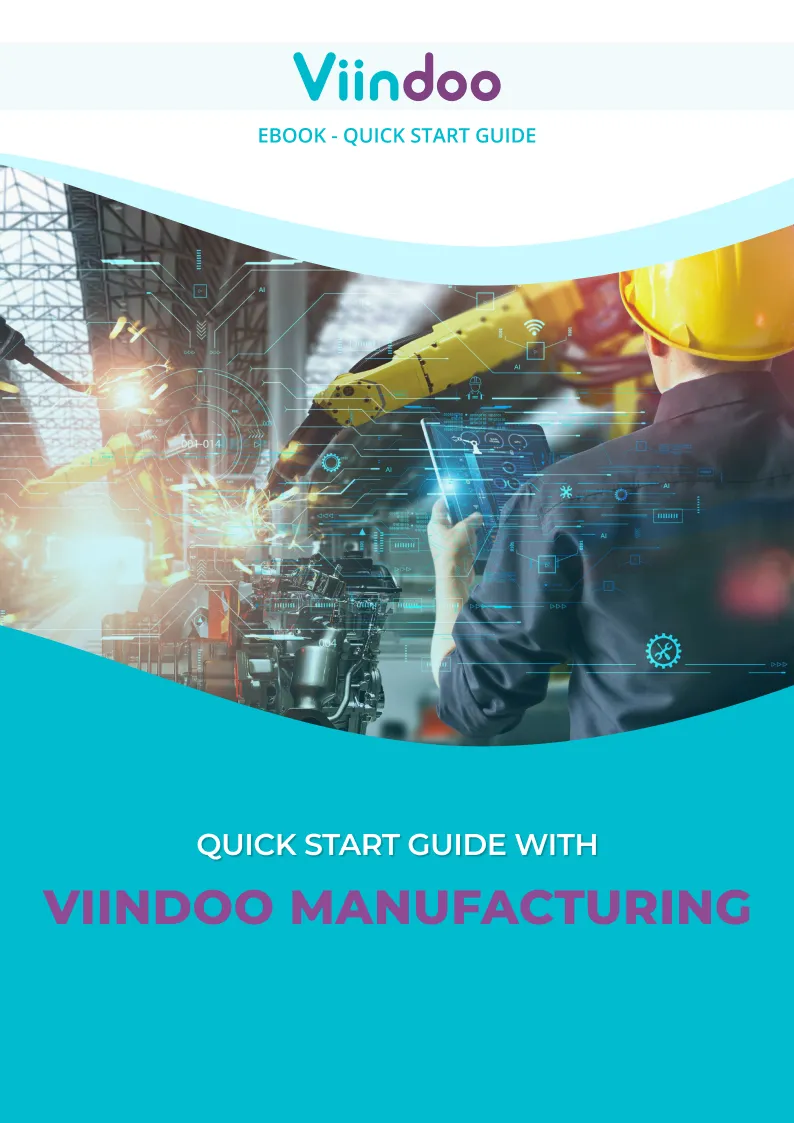
Quick Start Guide with Viindoo Manufacturing
A Free ebook Quick Start Guide with Viindoo Manufacturing for manufacturing enterprises seeking to optimize management processes and achieve significant business growth.
Real-time Data Collection
How Viindoo Automates Data Collection for Accurate OEE Calculation: Viindoo Manufacturing Software automates the collection of critical data points needed for OEE calculation, including machine availability, performance rates, and quality metrics. This automation minimizes human errors and ensures that the data used for OEE calculations is both accurate and timely.
Analyzing and Reporting
Tools within Viindoo for Analyzing OEE Data: Viindoo includes powerful analytics tools designed to break down OEE data into actionable insights. These tools allow for deep dives into each component of OEE — Availability, Performance, and Quality — highlighting areas for improvement and tracking the effectiveness of implemented changes.
Customizable Reports and Dashboards to Visualize OEE Trends: The software features customizable reports and dashboards that present OEE trends, losses, and bottlenecks in a user-friendly format. These visualizations help identify patterns and areas requiring attention, facilitating strategic decisions to enhance productivity.
Actionable Insights for Improvement
Using Viindoo to Identify Bottlenecks and Inefficiencies: Viindoo's analytical capabilities extend to identifying bottlenecks and inefficiencies within the manufacturing process. By analyzing the collected data, the software suggests specific areas where improvements can be made, such as reducing machine downtime, optimizing performance, or enhancing product quality.
Case Studies or Examples where Viindoo has Helped Improve OEE: Numerous manufacturing entities have leveraged Viindoo to significantly improve their OEE scores. For instance, a case study within the provided documentation illustrates how a manufacturer utilized Viindoo to reduce unplanned equipment downtime by 30% and increase production output by 15%, showcasing Viindoo's potential to transform manufacturing operations.
Implementing OEE Measurement with Viindoo
Implementing OEE (Overall Equipment Effectiveness) measurement with Viindoo Manufacturing Software involves setting up your manufacturing environment within the system to track and analyze production efficiency. Here's how to get started:
Steps to Setup OEE Tracking in Viindoo Manufacturing Software
To be able to set up OEE Tracking in Viindoo, we need to manage manufacturing process in Viindoo software:
>>>See more: Manage manufacturing process in Viindoo
1. Activate Work Orders Feature
Enable the Work Orders feature to manage detailed operations at work centers.
2. Configure Work Centers:
Enter the name, working hours, and other relevant details like Time Efficiency, Capacity, and OEE Target for each work center.
3. Configure Operations
Detail the operation name, associated bill of materials (BoM), and the work center where the operation will be performed. Also, specify duration computation methods.
4. Configure Quality Control Points and Quality Check
Incorporate material management strategies by assigning control points at various phases of the manufacturing process, including checks on input materials and inspections of the final product quality. This approach ensures that material management plays a crucial role in maintaining the integrity and efficiency of the production line.
>> See more: Create Control point and Quality Check
5. Configure Bills of Materials (BoM)
Fill in product details, quantity, Manufacturing BoM type, and components required for manufacturing.
>> See more: How to create bills of materials
6. Schedule Manufacturing Orders:
Select the product, add the quantity, and set the scheduled date. The system auto-fills information based on the predefined BoM.
>> See more: Create the Manufacturing Orders
7. Data Analysis and Reporting
Viindoo offers extensive reporting capabilities, allowing you to analyze OEE trends over time. Use these insights to identify areas for improvement in your manufacturing processes.
Implementing OEE measurement with Viindoo streamlines the process of collecting and analyzing production data. By configuring your equipment, shifts, and orders within Viindoo, you can gain a clear understanding of your manufacturing efficiency and pinpoint areas for enhancement.
Discover Viindoo Manufacturing Software
The All-in-one Inventory Software for Manufacturers. Monitor OEE and optimize your manufacturing operation.
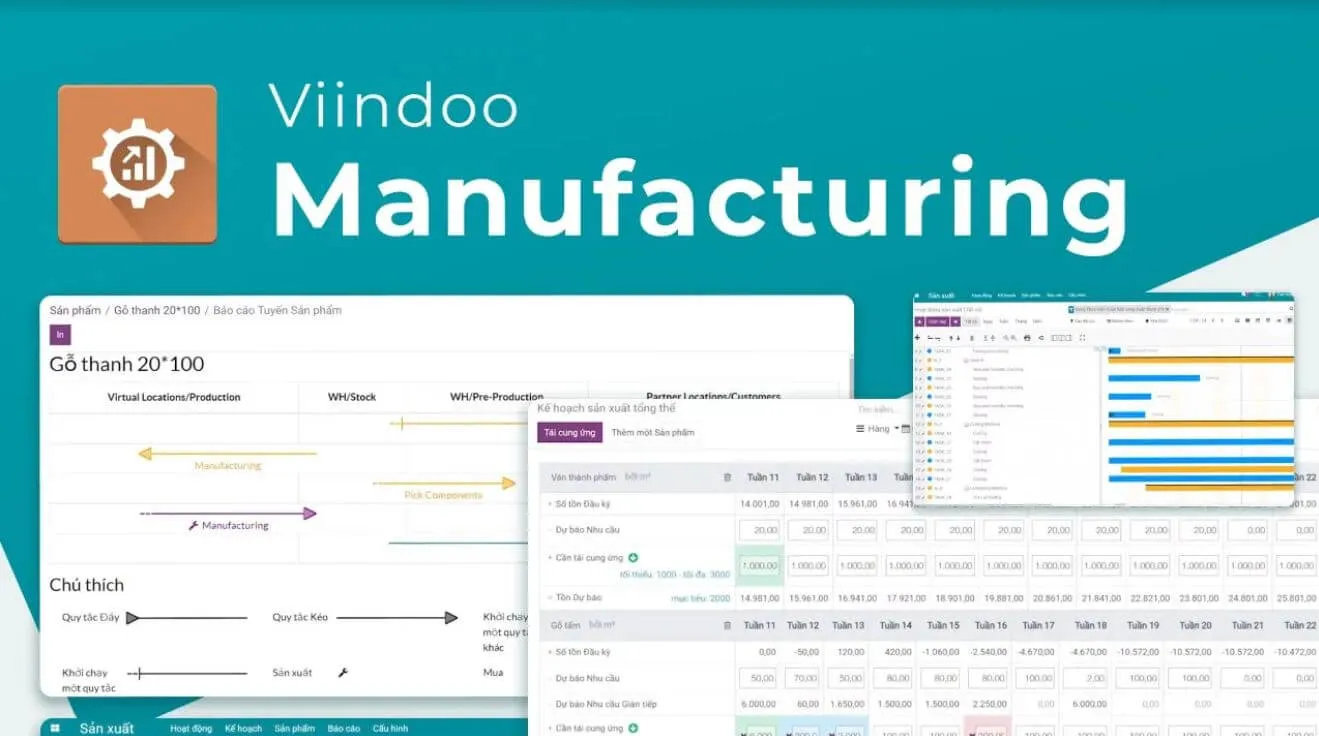
Lessons Learned and Best Practices from These Implementations
- Data-Driven Decision Making: Leveraging real-time data collection and analysis for informed decision-making.
- Employee Engagement: Actively involving employees in the process of using the software and in continuous improvement initiatives.
- Iterative Improvement: Starting with small, manageable changes and gradually expanding the scope of improvements.
- Comprehensive Training: Ensuring all users are well-trained on how to use Viindoo Manufacturing Software effectively.
FAQs
OEE stands for Overall Equipment Effectiveness. It is a key performance indicator (KPI) that measures the efficiency and effectiveness of a manufacturing process. OEE helps in identifying the percentage of manufacturing time that is truly productive. It combines three essential factors: Availability, Performance, and Quality, to provide a single comprehensive metric that can be used to drive improvements in manufacturing processes.
OEE is important because it directly correlates to a plant's productivity, helps in identifying losses, and provides actionable insights to eliminate waste and improve the manufacturing process.
OEE is calculated by multiplying three components: Availability, Performance, and Quality, which are expressed as percentages.
- Availability measures the portion of planned production time that the operation is actually running. It factors in downtime losses due to equipment failure, setup, and adjustments.
- Performance measures the speed at which the equipment operates as a percentage of its designed speed. It includes losses due to idling and minor stops, as well as reduced speed.
- Quality measures the production of quality products as a percentage of the total products produced, accounting for losses due to defects and rework.
The formula for OEE is:
OEE=Availability×Performance×Quality.
mproving OEE involves strategies aimed at enhancing its three components: Availability, Performance, and Quality. Here are some targeted approaches:
- For Availability: Reduce equipment downtime by implementing preventive maintenance, improving setups and changeovers, and ensuring that machinery is properly calibrated and functioning efficiently.
- For Performance: Optimize the speed of your machinery through regular maintenance, operator training, and by addressing any bottlenecks in the production process. Implement Lean manufacturing principles to streamline operations and reduce idle time.
- For Quality: Focus on reducing the number of defects and rework. This can be achieved through quality control checks at different stages of the production process, employee training, and by using high-quality materials.
Conclusion
Summary of Key Points
- OEE is a critical metric for measuring manufacturing efficiency, encompassing Availability, Performance, and Quality.
- Viindoo Manufacturing Software significantly enhances the ability to measure and improve OEE by automating data collection, providing in-depth analysis, and enabling real-time monitoring and actionable insights.
The Strategic Importance of Continuously Monitoring and Improving OEE
Continuously monitoring and improving OEE is essential for maintaining competitive advantage in the manufacturing industry. It helps in identifying inefficiencies, reducing costs, and ensuring product quality, ultimately leading to increased customer satisfaction and business growth.
Encouragement to Adopt Viindoo Manufacturing Software for OEE Optimization
Manufacturers looking to optimize their production processes and improve their OEE scores are encouraged to consider Viindoo Manufacturing Software. Its comprehensive features and user-friendly interface make it an invaluable tool for achieving operational excellence.