The manufacturing process is a series of sequential, complex steps to transform raw materials into finished products. While manufacturers strive to optimize their operations and maximize productivity, they often encounter many challenging obstacles. In this article, we explore the challenges that manufacturers face in the production process and how Viindoo MRP can effectively address these difficulties.
Learn about The Manufacturing Process
Before delving into the pain points, let's first have a comprehensive understanding of the manufacturing process. This process involves a series of activities, including design, planning, sourcing, manufacturing, quality control, and product distribution. It involves both human labor and the use of machinery and advanced technology. With precision and attention to detail, each stage contributes to the overall success of the production process.
>>>> Read more: What is Demand Driven Material Requirements Planning DDMRP
Product design: The first step of the Manufacturing Process
In the initial stage of the manufacturing process, designers play a crucial role in turning ideas into tangible products. They conceptualize and create prototypes, consider factors such as functionality, aesthetics, and market needs. By leveraging their expertise and creative abilities, designers lay the foundation for a successful production journey.
Product design
Planning: From detailed planning to execution
After the design is completed, meticulous planning is a necessary task to carry out. Manufacturers need to identify necessary resources, estimate costs, and set strategic time milestones. Effective planning will ensure efficient allocation of materials, labor, and equipment, minimize delays, and optimize productivity.
>>>> Check out: Production scheduling software
Find the source of supply: Building a strong supply chain.
The stage of finding the source of supply involves purchasing raw materials, components, and necessary equipment for production. Establishing relationships with reliable suppliers and negotiating beneficial terms can enhance efficiency and reduce costs. However, controlling the supply source within the complexity of the global supply chain and managing potential disruptions are common challenges that manufacturers must face.
Building a strong supply chain
Production: Transforming raw materials
Production execution is the center of a manufacturing process, where raw materials are transformed into finished goods. Machinery and skilled labor work in parallel to ensure accurate production, adhere to strict quality standards.
However, maintaining consistency, meeting production goals, and avoiding bottlenecks can be significant challenges in this phase.
>>>> Read more: Manufacturing BoM
Quality control: Maintaining high quality standards
Quality control is crucial to ensure that all products manufactured meet predetermined quality standards. Strict inspection, testing, and compliance with regulations help identify errors and ensure customer satisfaction.
However, maintaining stable quality in a large-scale manufacturing process can pose unique challenges for manufacturers.
>>>> See Details: How to Implement Quality Control in Manufacturing
Distribution: Market access
After the products have undergone quality control checks, they will be prepared for distribution in the supply chain. Effective logistics management, including inventory control, packaging, and transportation, will ensure timely delivery to customers.
Overcoming barriers in logistics management and optimizing the distribution network play a crucial role in achieving customer satisfaction and meeting market demands.
Pain points in the Viindoo MRP Production Process & Solutions
Although optimizing the production process brings great potential for businesses, there are some challenges that manufacturers often face in this process. Let's explore these challenges and effective solutions to overcome them with Viindoo - a leading provider of manufacturing management software systems.
Viindoo MRP - production management software
Lack of real-time data display capability
A major challenge in the production process is the lack of ability to display real-time data at all stages. Without accurate data on inventory levels, production status, and resource allocation, decision-making becomes guesswork. This leads to delays, excessive reserves, misuse of resources, and missed opportunities to meet customer demands. How can Viindoo MRP reduce this pain point?
Viindoo MRP provides the ability to display comprehensive real-time data for all aspects of your manufacturing operations. Through a visual dashboard, you can monitor inventory levels, track work progress, and identify bottlenecks instantly. With up-to-date information at your fingertips, you can make informed decisions and drive efficiency throughout your operations.
List of production commands in viindoo
Production command report in Viindoo
>>>> Discover more: Software to manage and track production progress
Ineffective planning and scheduling
Effective planning and scheduling are crucial to optimize the manufacturing process. However, manual processes or outdated systems can lead to errors, inefficiencies, and suboptimal resource utilization. This can result in production delays, increased costs, and dissatisfied customers. How can Viindoo MRP directly address these challenges?
Viindoo MRP provides advanced planning and scheduling tools to streamline your operations, including Master Production Scheduling (MPS) and Gantt Chart. With its intelligent algorithms, you can optimize production sequences, allocate resources efficiently, and minimize down-time. By automating the planning processes, Viindoo MRP enables you to meet customer demands accurately, while reducing costs and improving overall productivity.
List of production activities in Viindoo
Make production activities with Gantt Chart in Viindoo
MPS report in Viindoo
>>>> See Details: Production scheduling?
Maintaining stable quality on a large production scale
Strictly maintaining quality control according to standards and recording quality inspection results is crucial in the manufacturing industry. However, ensuring consistent product quality and compliance across different stages in large-scale production can be a challenge. How does Viindoo MRP address these difficulties?
Viindoo MRP integrates quality control modules within its system. It allows you to define quality inspection criteria at each stage of the production process, ensuring compliance with standards and minimizing errors. With Viindoo MRP, you can deliver products that meet or exceed customer expectations and track product defect rates.
Quality control points in Viindoo MRP
Quality check in Viindoo MRP
Quality warning in Viindoo MRP
>>>> Useful knowledge: Manufacturing Scrap: Definition, Measurement, Accounting Treatment
Communication Gaps and Collaboration
Effective communication and collaboration play a crucial role in streamlining the manufacturing process. Misinformation or delays in sharing important information can lead to misunderstandings, errors, and delays. How can Viindoo MRP narrow down this communication gap?
Viindoo MRP provides a centralized platform for communication and seamless collaboration.Viindoo's integrated communication and collaboration system allows individuals and production teams to share real-time updates, quickly resolve issues, and coordinate tasks easily. With Viindoo MRP, everyone involved in the production process can maintain connections, ensure smooth operations, and complete tasks on time.
Message messaging system in Viindoo
Lack of scalability and adaptability
As businesses grow, scalability and adaptability become important factors in the manufacturing process. Traditional systems often struggle to keep up with development needs, leading to inefficient operations and missed opportunities. How can Viindoo MRP empower you to effectively expand the scale of your operations?
Viindoo MRP is designed to meet the changing needs of your business. Whether you are expanding your product lines, introducing new manufacturing processes, or venturing into different markets, Viindoo MRP can seamlessly meet your requirements. Viindoo's modular structure allows you to customize functions and add new features as your business grows. With Viindoo MRP, you can prove your production activities in the future and position yourself to continue succeeding.
FQAs
Is Viindoo MRP suitable for small -scale manufacturers?
Yes, Viindoo MRP serves businesses of all sizes. Its modular design allows you to select functions that suit your specific needs, making it an ideal solution for small-scale manufacturers looking to optimize their production processes.
Can Viindoo MRP handle complicated supply chain management?
Viindoo MRP provides powerful supply chain management capabilities, including inventory management, procurement, and supplier relationship management. Viindoo MRP allows you to streamline your entire supply chain, from sourcing raw materials to delivering finished products.
Does Viindoo MRP provide analytical and reporting features?
Yes, Viindoo MRP includes powerful reporting and analysis tools. It provides comprehensive insights into key performance indicators, production efficiency, and resource utilization. With customizable and real-time visual reports, you can make data-driven decisions to improve productivity and profitability.
Is Viindoo MRP a cloud -based solution?
Yes, Viindoo MRP is a software solution in the form of Software as a Service (SaaS) based on cloud computing. This means that you can access it anytime, anywhere as long as you have an internet connection. The cloud-based nature of Viindoo MRP ensures easy deployment, scalability, and data security.
How much does Viindoo MRP software cost?
Viindoo MRP is permanently free for the first application with unlimited users. See details about service pricing here: https://viindoo.com/pricing
Optimizing the manufacturing process has many pain points, challenges that can hinder the productivity and profitability of manufacturing businesses. However, with Viindoo MRP, these challenges can be effectively addressed. From providing real-time visibility and efficient planning to ensuring quality control and seamless communication, Viindoo empowers manufacturers to optimize their operations and achieve sustainable growth. It is time to say goodbye to the outdated systems and welcome the future of production with Viindoo MRP.
>>>> Related article:
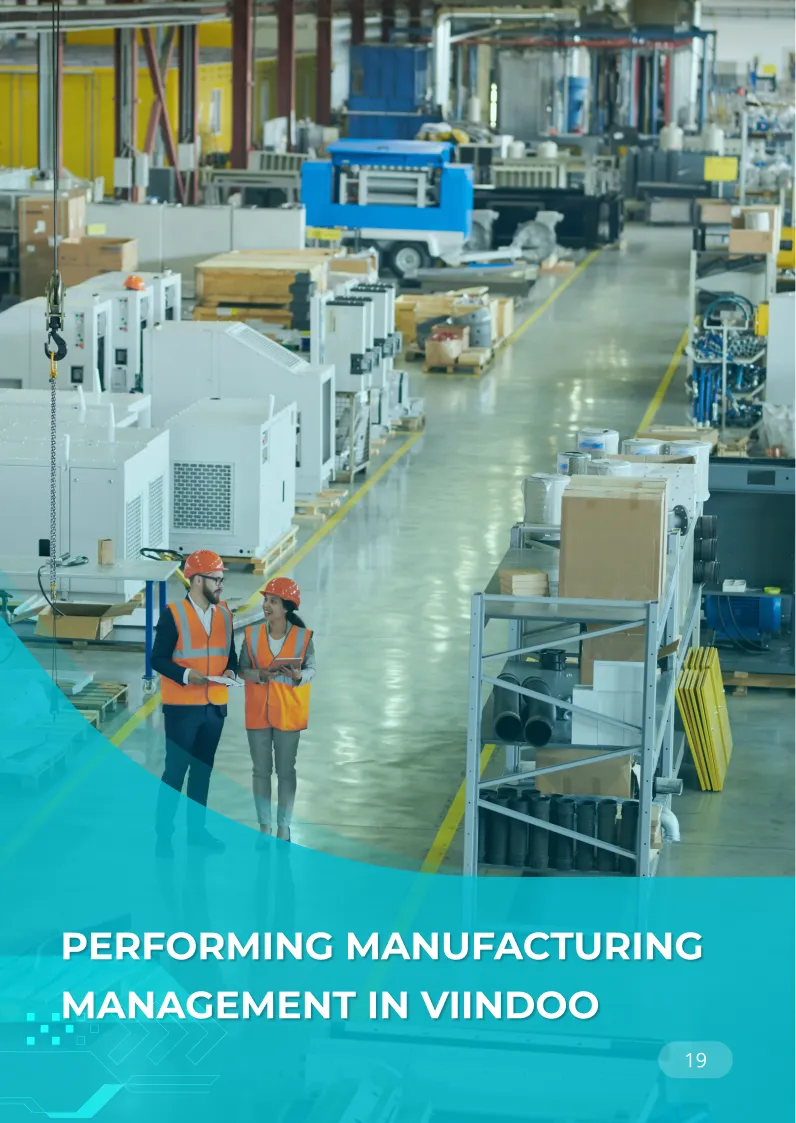
Free Forever
Start using Viindoo MRP and optimize your
production process right now!