DMAIC? This is a method applied by many businesses around the world to their business processes. This method was first used in manufacturing and is increasingly applied in other industries such as finance, health,... Viindoo's following article will summarize detailed information for businesses.
1. What is six sigma?
Six Sigma is a quality management and process improvement system developed by Motorola in 1985. The main goal of Six Sigma is to eliminate errors and fluctuations in production and business processes by using statistical techniques and data analysis. This approach focuses on improving product quality, minimizing costs, enhancing customer satisfaction, and maximizing profits.
Since it was created by Motorola and fully applied by Jack Welch at General Electric in 1995, Six Sigma quickly became a standard quality management method, trusted by multi-industry corporations around the world. use and bring high efficiency.
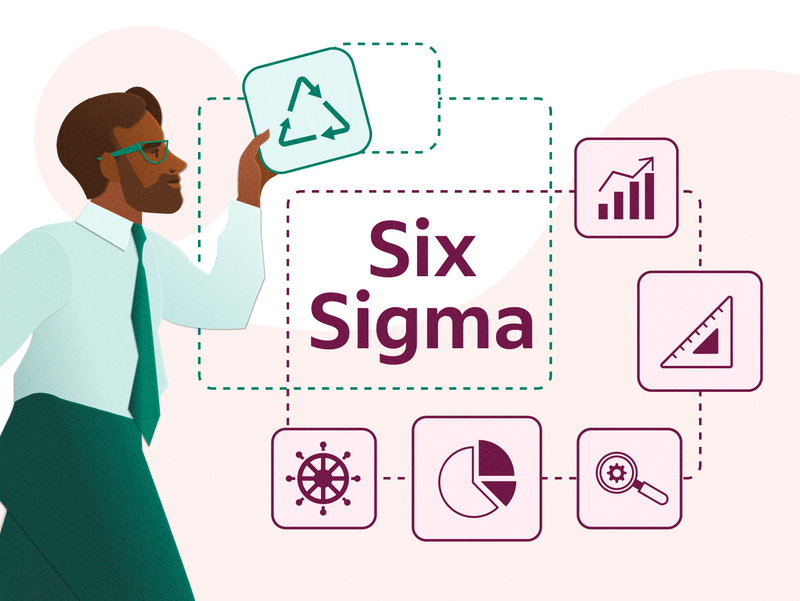
Six Sigma is a quality management system developed in 1985
2. 5 basic principles of 6 sigma
2.1 Focus on customers
First principle of Six Sigma is putting customers first. To achieve this, businesses need to clearly understand the needs and desires of customers. With this principle, businesses strive to meet the quality standards that customers require. From there, businesses can create superior products and services, enhancing customer satisfaction and loyalty.

Focus on customers
2.2 Measure current value and find problems that need to be solved
Six Sigma emphasizes measuring and analyzing the current value of processes. In this discipline, businesses map the steps in the process and collect detailed data. Thanks to this, businesses can identify existing problems and need to fix them. This helps ensure that any improvements are based on accurate and specific information, helping to optimize operational efficiency.
2.3 Eliminate process errors
One of the main goals of Six Sigma is to eliminate errors and defects in the manufacturing process. With this goal, businesses detect and fix the root causes of errors. From there, businesses can improve product and service quality, reduce waste, and increase operational efficiency. This helps save costs and improve the reputation of the business in the market.

Eliminate process errors
2.4 Ensure continuous operation
Six Sigma encourages the maintenance of continuous and uninterrupted operations. This requires businesses to develop and adhere to standard processes, ensuring that every aspect of operations is strictly controlled. Maintaining continuity in the process helps optimize productivity and ensures that the business is always ready to meet customer needs.

Ensure business operations continue continuously
2.5 Establish a flexible and highly adaptive ecosystem
Finally, Six Sigma emphasizes building a flexible and adaptable business ecosystem. This means businesses must be able to adjust quickly to changes in the market and customer requirements.
With this principle, businesses create a flexible working environment that promotes innovation. Not only that, businesses can also improve their competitiveness and ensure long-term sustainable development.
3. 2 main methods of Six Sigma
3.1 DMAIC
DMAIC stands for the stages: Define, Measure, Analyze, Improve and Control. This is a mainstream method in Six Sigma to improve existing processes to enhance customer satisfaction and operational efficiency.

DMAIC
3.2 DMADV
DMADV stands for the stages: Define, Measure, Analyze, Design and Verify. It is part of the Design for Six Sigma (DFSS) process, which is used to design or re-engineer product manufacturing or service delivery processes.

DMADV
4. Process of applying Six Sigma to businesses
Procedure Six Sigma is a standard approach to optimizing and improving business processes, with a strong customer focus and the use of data for decision making. The DMAIC method, commonly used in Six Sigma, includes five main stages as follows:
DEFINE (Define)
This phase begins with a focus on the customer.
Step 1: Businesses need to identify problems from the customer's perspective.
Step 2: Set specific goals. What does the business want to achieve and what resources should it use to achieve its goals?
Step 3: Map current processes and verify with stakeholders to ensure that the business is on track.
MEASURE (Measurement)
This phase focuses on measuring and collecting process-related data.
Step 1: Businesses need to measure the problem with metrics or supporting data.
Step 2: Determine the required performance indicators and set the limits for “Y”.
Step 3: Evaluate the current measurement system to ensure it can help achieve the desired results.
ANALYZE (Analysis)
This phase analyzes the process to find the influencing factors and root causes of the problem.
Step 1: Determine if the current process is effective and satisfactory. Does the process help achieve the set goals?
Step 2: Quantify goals with specific data. For example, reduce the rate of defective goods by 20%.
Step 3: Analyze variations using historical data to determine the cause of the problem.
IMPROVE (Improved)
This phase focuses on finding solutions and improving processes.
Step 1: Identify possible causes of the problem. Perform experiments to determine which variable "X" affects "Y".
Step 2: Discover relationships between variables to find effective solutions.
Step 3: Determine process tolerances, i.e. the exact values that variables can have and still stay within acceptable limits. Businesses can use tools to achieve these tolerances.
CONTROL (Control)
This final phase ensures that improvements are made and remain effective over the long term.
Step 1: Revalidate the measurement system to ensure accuracy and reliability.
Step 2: Establish process capabilities to ensure performance goals are achieved. For example, is the target of reducing defective goods by 20% being met?
Step 3: After the previous steps have been fully implemented, businesses proceed to implement the process and maintain the improvements made.
Streamline Six Sigma - DMAIC Process with Viindoo ERP
Viindoo is open source ERP software that provides many applications to help businesses manage their operations. It is highly customizable and can be tailored to meet the specific needs of manufacturing companies. Here are some ways that Viindoo software can support the key principles of Six Sigma.
Define
The first step in the DMAIC process is to identify the problem or opportunity for improvement. With Viindoo Dashboards and reporting tools, companies can easily track and measure key performance indicators (KPIs) to identify areas for improvement. This provides a solid foundation for the rest of the Six Sigma process.
Measure
Once the problem has been identified, the next step is to measure the current state. Viindoo's data management system enables real-time data collection and analysis, making it easier to monitor and measure processes. This helps companies identify bottlenecks and areas for improvement more accurately.
Analysis
With the help of Viindoo's advanced analytics tools, companies can analyze data to identify the root cause of the problem. This can be done by creating custom reports and dashboards that provide insights into different aspects of the manufacturing process. By understanding the underlying cause of the problem, companies can implement effective solutions.
Improve
Viindoo's customizable workflow and automation features can help companies make improvements quickly and efficiently. For example, if a company identifies a bottleneck in its manufacturing process, it can use Viindoo to automate certain tasks or streamline communication between departments to eliminate the bottleneck.
Control
The final step in the Six Sigma process is to establish controls to maintain the improvements made. With Viindoo's real-time data and analytics, companies can monitor processes and ensure that they run smoothly. If any problems arise, they can be addressed promptly to prevent them from becoming bigger problems.
Forecasted Report is ultimate tool to Control Manufacturing Plan with JIT in Viindoo ERP
Discover Viindoo Manufacturing Software
In the dynamic manufacturing sector, the Viindoo MRP (Manufacturing Resource Planning) application stands out as a flexible tool that fits perfectly with the principles of the Six Sigma methodology. Designed to optimize manufacturing processes, improve efficiency and drive continuous improvement, Viindoo MRP serves as the foundation for manufacturing excellence.
Through comprehensive features such as scheduling inventory management and quality management, Viindoo MRP provides manufacturers with the tools needed to streamline operations and reduce waste. Furthermore, its intuitive interface and customizable modules make it adaptable to the unique needs of diverse production environments.
When integrated with the Six Sigma methodology, which emphasizes data-driven decision making, process optimization and error reduction, Viindoo MRP becomes a powerful catalyst to drive export performance. sharp. By leveraging Six Sigma's DMAIC (Define, Measure, Analyze, Improve, Control) framework, manufacturers can identify areas for improvement, implement targeted solutions, and monitor Monitor performance metrics in real time with Viindoo MRP's powerful reporting capabilities.
When integrated with the Six Sigma methodology, which emphasizes data-driven decision-making, process optimization and error reduction, Viindoo MRP becomes a powerful catalyst to drive export performance sharp. By leveraging Six Sigma's DMAIC (Define, Measure, Analyze, Improve, Control) framework, manufacturers can identify areas for improvement, implement targeted solutions, and monitor performance metrics in real time with Viindoo MRP powerful reporting capabilities.
Discover Viindoo Manufacturing Software
Viindoo MRP (Manufacturing Resource Planning) is a ultimate tool that fits perfectly match with the principles of the Six Sigma methodology support the DMAIC Progress
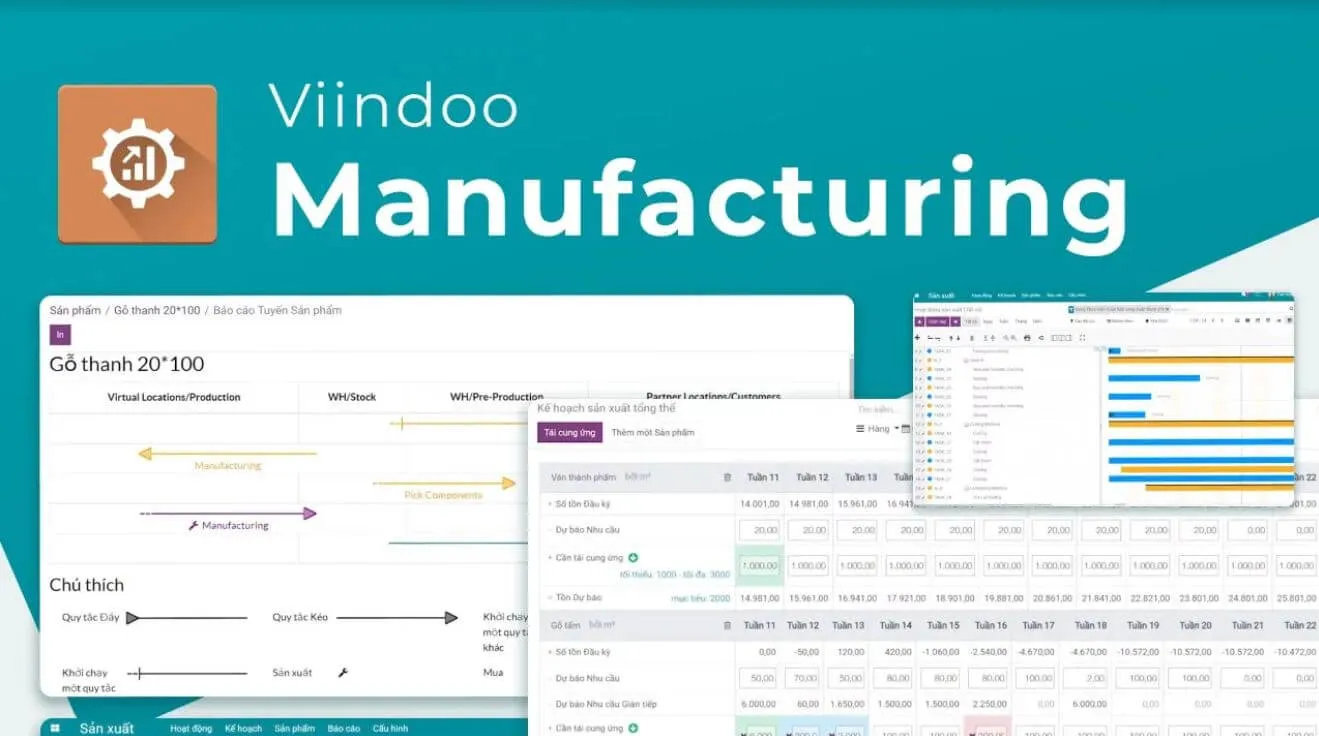
FAQ
What is the difference between Six Sigma and Lean manufacturing?
While both aim to improve efficiency and reduce waste, Six Sigma focuses on reducing process variation and defects, while Lean manufacturing focuses on eliminating waste and maximizing value for the customer.
How can ERP software support Six Sigma in manufacturing?
ERP's software can support Six Sigma by providing real-time data and analytics, automating processes, and streamlining communication between departments.
What is the DMAIC process?
DMAIC stands for Define, Measure, Analyze, Improve and Control. This is a structured problem solving method used in Six Sigma.
Can Six Sigma be integrated with ERP software?
Yes, Six Sigma can be integrated with ERP software to further enhance its effectiveness. Viindoo is an open-source ERP software that offers a wide range of applications to help businesses manage their operations.
Conclusion
In today's fast-paced manufacturing industry, companies must constantly strive to improve efficiency and productivity to stay ahead of the competition. Six Sigma manufacturing offers a data-driven approach to process improvement that can help companies achieve this goal. By understanding the differences between Six Sigma and Lean manufacturing, overcoming common challenges, and integrating Six Sigma with ERP software like Viindoo, companies can maximize efficiency and reap the benefits of this approach.