Manufacturing BoM (Bill of Materials) is a crucial component in the production process, enabling efficient manufacturing management. By properly managing BoMs, manufacturers can streamline their operations, optimize resources, and ensure the timely delivery of high-quality products. In this article, we will explore the critical aspects of manufacturing BoM, discuss best practices for effective manufacturing management.
What is BoM (Bills of Materials)?
A Bills of Materials (BoM) is a comprehensive and structured list that outlines all the components, parts, materials, sub-assemblies, and instructions required to manufacture a final product. It serves as a critical reference document within manufacturing and production processes, providing a clear breakdown of the items needed for each stage of assembly.
A Bill of Materials (BoM) in manufacturing management
BoMs are utilized in various industries, such as manufacturing, engineering, construction, and electronics, to ensure accurate communication and coordination among different teams involved in the production cycle. They play a pivotal role in maintaining consistency, precision, and efficiency throughout the manufacturing process.
A typical BoM includes detailed information about each component, including part numbers, descriptions, and quantities, and often includes the relationships between components. This hierarchical structure allows for easy visualization of how parts fit together and how they contribute to the overall product.
There are different types of BoMs, each serving specific purposes:
- Engineering BoM (EBoM): Primarily used by design and engineering teams, an EBoM focuses on the product's design and structure. It includes all the components needed to create the product as conceptualized in the design phase.
- Manufacturing BoM (MBoM): This type of BoM is used by production and manufacturing teams. It includes additional details relevant to the manufacturing process, such as assembly instructions, manufacturing sequences, and specific quantities required for production.
- Sales BoM (SBoM): Used by sales and marketing teams, an SBoM emphasizes the final product as it will be sold to customers. It might include packaging details, optional components, or accessories.
>>>> Read more: Breaking Down the Differences: Production vs Manufacturing
BoMs are dynamic documents that can undergo revisions and updates as designs evolve, new materials are introduced, or improvements are made to the manufacturing process. Effective management of BoMs is crucial to ensure that all stakeholders have access to accurate and up-to-date information, minimizing errors, delays, and discrepancies during production.
Manufacturing BoM is an essential factor in the manufacturing industry
How Does a Manufacturing BoM Improve Efficiency?
A manufacturing BoM is a comprehensive list of all the components, materials, assemblies, and sub-assemblies required to build a product. It serves as a roadmap for manufacturers, detailing the quantity and specifications of each item necessary for successful production. A well-structured BoM ensures accurate planning, efficient resource allocation, and seamless coordination throughout the manufacturing process.
By creating a detailed manufacturing BoM, companies can streamline their operations and enhance overall efficiency.
Precise Resource Allocation and Planning
A manufacturing BoM functions as a compass, guiding the allocation of resources with unparalleled precision. Detailing the requisite components and quantities empowers production managers to strategically plan material acquisition, labor allocation, and equipment usage. This meticulous foresight preemptively averts shortages, reduces wastage, and ensures a harmonious workflow, ultimately culminating in a more efficient production cycle.
>>>> Read more: Production Capacity Planning: Definition, Types, and Best Practices
Seamless Production Sequencing and Scheduling
Manufacturing BoMs are akin to a symphony conductor, orchestrating the intricate dance of production sequences. Each component's placement within the BoM delineates its chronological significance in the assembly process. This hierarchical arrangement aids in sequencing operations, optimizing the order of tasks, and minimizing idle time or bottlenecks. The result is a synchronized, uninterrupted workflow that accelerates throughput and expedites the manufacturing timeline.
Informed Decision-Making and Continuous Improvement
Informed decisions are the bedrock of efficiency. A comprehensive BoM empowers managers with a holistic view of the product's composition, allowing them to make data-driven choices. Whether it's evaluating alternative components, identifying cost-effective substitutes, or implementing design enhancements, BoM-driven insights fuel continuous improvement initiatives. This agile responsiveness enhances product quality, reduces lead times, and fosters an environment of perpetual refinement.
Manufacturing BoM is one of the important factors in Manufacturing management
Accurate Inventory Management
Effective inventory management hinges on precision and real-time visibility. Manufacturing BoMs serve as a compass for maintaining accurate inventory levels. By specifying required quantities, they enable inventory managers to align procurement with production needs. Timely replenishment and judicious stockpiling prevent stockouts and excess stock, striking an equilibrium that curtails carrying costs and optimizes cash flow.
>>>> Read more: Manufacturing Inventory: Definition, Types, and Best Practices
Reduced Rework and Rework
Manufacturing BoMs serve as a beacon of accuracy, diminishing the likelihood of errors and rework. Clear instructions regarding component placement, specifications, and quantities mitigate the risk of assembly mishaps. By ensuring that each component fits seamlessly into the whole, BoMs minimize the need for rework, revisions, and corrective actions. This not only expedites production but also conserves resources and labor hours.
Enhanced Cross-Functional Collaboration
Efficiency flourishes in an ecosystem of collaboration. BoMs act as a lingua franca, facilitating communication across departments - from design and engineering to procurement and production. This shared understanding promotes cohesive teamwork, reduces misinterpretations, and fosters a culture of synergy. As a result, projects move forward cohesively, without undue friction, and with a collective drive towards operational excellence.
Consistency in Quality
By meticulously detailing every material component, specifying precise sequences, and providing comprehensive specifications, BoMs create a framework that guides manufacturing processes with pinpoint accuracy. This results in reduced errors minimized rework, and a standardized approach that guarantees consistent, top-tier product quality. Explore how harnessing the power of BoMs can elevate your manufacturing operations to new levels of excellence and reliability.
>>>> Read more:
- How to Implement Quality Control in Manufacturing
- Maximizing Efficiency of Byproducts in Manufacturing
- Manufacturing Scrap: Definition, Measurement, Accounting Treatment
How can Managers create and manage the Manufacturing BoM effectively?
A Manufacturing Bill of Materials (BoM) is the blueprint that guides the production process, ensuring accurate assembly and consistent product quality. Effective creation and management of BOMs require a systematic approach. Certainly, here are five key factors to help managers create and manage the Manufacturing Bill of Materials (BoM) effectively:
1. Clear and Detailed Component Information:
Ensure that each component in the Manufacturing BoM is accurately described with all necessary details such as part numbers, descriptions, quantities, and units of measure. This clarity prevents confusion during production.
2. Standardized BoM Structure:
Establish a consistent format for structuring BoMs. Clearly define parent-child relationships between assemblies and sub-assemblies, ensuring a logical and easy-to-follow hierarchy.
3. Version Control and Change Management:
Implement a robust version control system to track revisions and changes to the BoM. Establish a well-defined process for documenting and approving changes to avoid errors and ensure everyone is working with the latest information.
4. Cross-Functional Collaboration:
Foster collaboration between various departments, such as engineering, procurement, production, and quality control. Effective communication and coordination help prevent misunderstandings and ensure all teams are aligned.
5. BoM Management Software or ERP System:
Utilize specialized BoM management software or an Enterprise Resource Planning (ERP) system to centralize BoM data, streamline updates, and ensure real-time access for managers.
The flow of MRP management in Viindoo
Importantly, an Enterprise Resource Planning (ERP) system streamlines data flow, ensuring real-time updates and accurate synchronization across departments like design, engineering, production, and procurement. This synergy eliminates manual data entry, enhances inventory management with automatic updates, optimizes procurement processes, supports precise production planning, and enables efficient cost control through linked BoM data. The integration fosters consistency, reduces errors, and provides a comprehensive platform for collaborative BoM management, ultimately bolstering manufacturing efficiency and product quality.
By focusing on these factors, managers can enhance the accuracy, efficiency, and overall effectiveness of creating and managing the BoM, leading to smoother production processes and improved product quality.
>>>> Read more: Streamline Your Manufacturing with These Top MRP Software Solutions
Viindoo - The optimal solution for effective Manufacturing BoM management
In the ever-evolving landscape of modern business, seizing opportunities and maximizing potential is essential. Viindoo stands as a comprehensive software solution designed to unlock your enterprise's capabilities and drive growth.
Viindoo goes beyond conventional software systems. It's a dynamic toolset engineered to streamline your operations, enhance collaboration, and amplify your overall efficiency. Whether you're a startup, a growing company, or an established industry leader, Viindoo is tailored to meet your diverse needs.
Moreover, Viindoo steps in as your trusted partner, offering a range of cutting-edge features designed to empower your organization with streamlined and effective BoM management.
Viindoo Empowers Managers to create, Apply, and Reuse Manufacturing BoM with Ease
Viindoo allows users to create the Manufacturing BoM. A finished and semi-finished product is a technical product in the system. Once the Manufacturing order is created, the system will automatically check and show every component's availability, resulting in the automation of supply rules in order to fulfill the components. Moreover, with the miscellaneous manufacturing features in Viindoo, the managers can define when the manufacturing order will be ready to process, and when either all components are available for components for 1st operation are available.
In Manufacturing, flexibility plays an important role. The consumption of materials can be changed because of many objective reasons. When using Viindoo, the users can allow flexible consumption of materials: allowed, allowed within warning, and blocked.
Viindoo provides tools for the user to create and manage the Manufacturing BoM
Viindoo automatically generates the rules for components fulfillment
Based on the Manufacturing BoM configures, Viindoo will automatically generate the supply-chain rules and routes to fulfill insufficient quantities in case the components are not available for the Manufacturing order such as creating a purchase order, a child manufacturing order,...Thereby, the chain including Purchase-Inventory-Manufacturing can be ensured with a smooth process.
Viindoo unlocks the BOM Management with BoM Structure & Cost
Because of the real-time data, generating BoM Structure and cost can be easy in Viindoo system. After creating BoM for the product, the managers can have a view of the product cost and BoM cost computed by summing the costs of the components and operations needed to build the product. Viindoo's real-time cost tracking keeps you updated on cost fluctuations, ensuring that you have a pulse on the financial aspect of your manufacturing operations. Thereby, armed with Viindoo's cost insights, managers and users can make data-driven decisions that optimize resources, enhance profitability, and drive efficiency. The managers can even add information on the product quantity that they would like to view the structure cost for more details.
In addition to BoM management, Viindoo offers a robust Manufacturing Resource Planning system) designed to optimize your production processes, inventory control, and resource allocation. Viindoo MRP empowers manufacturers to:
- Demand Forecasting: Predict future demand accurately based on historical data, enabling you to plan production and procurement activities effectively.
- Production Scheduling: Create optimized production schedules that align with demand, resource availability, and delivery timelines, enhancing overall efficiency.
- Inventory Optimization: Viindoo MRP helps you strike the right balance between maintaining adequate inventory levels and avoiding excess stock, reducing carrying costs.
- Resource Allocation: Allocate resources such as labor, machinery, and materials efficiently to maximize utilization and minimize downtime.
- Order Tracking: Monitor orders from creation to fulfillment, ensuring timely delivery and customer satisfaction.
- Performance Analytics: Viindoo MRP provides insights into your manufacturing performance, helping you identify bottlenecks, inefficiencies, and areas for improvement.
With Viindoo's advanced BoM management and MRP capabilities, you can elevate your manufacturing operations to unprecedented levels of efficiency and effectiveness. Embrace a future where BoMs are seamlessly managed and production processes are optimized for success. Explore Viindoo today and embark on a journey toward manufacturing excellence.
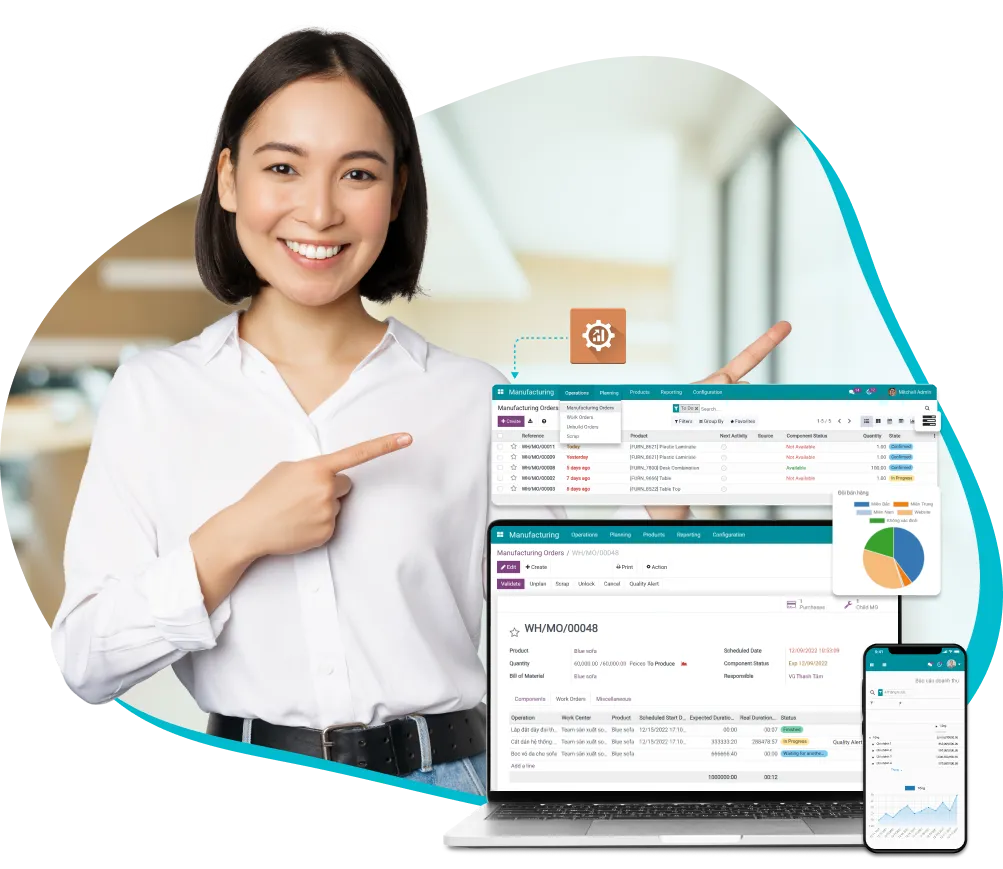
Comprehensive Manufacturing software
FREE TRIAL - NO CREDIT CARD REQUIRED
Comprehensive Manufacturing software fulfills the production management needs of enterprises in the 4.0 era.
Conclusion
Manufacturing BoM and manufacturing management are critical elements in optimizing production processes, reducing costs, and ensuring high-quality output. By understanding the intricacies of BOM creation and implementing effective manufacturing management techniques, manufacturers can streamline their operations, minimize errors, and enhance overall efficiency. With proper attention to detail, continuous improvement, and the utilization of modern software tools, manufacturers can unlock the full potential of their manufacturing processes and achieve greater success in the competitive market.
>>>> See more: