Have you ever been curious about the definition of a flexible maufacturing system? It is essentially a computerized production process that enables manufacturers to increase their production capacity and efficiency significantly. This adaptable manufacturing system, also known as FMS, can be implemented across various industries such as textiles, electronics, and food processing. The present blog post from Viindoo intends to delve into the different types of flexible manufacturing systems accessible today, along with their advantages and disadvantages.
>>>> See More: Manufacturing software
What is Flexible Manufacturing System?
A Flexible Manufacturing System (FMS) is a highly automated and computer-controlled manufacturing system that is designed to be adaptable and responsive to changing production requirements. An FMS typically consists of a group of machines, such as CNC (computer numerical control) machines, robots, and material handling systems, that are interconnected by a computer network and controlled by a central computer system.
The FMS is capable of producing a wide variety of products, using a variety of manufacturing processes, with minimal setup time and human intervention. This flexibility is achieved through the use of software programming and advanced robotics, which allow the system to quickly reconfigure itself to meet changing production needs.
FMS technology can be used in a variety of industries, including automotive, aerospace, electronics, and consumer goods manufacturing. The benefits of implementing an FMS include increased efficiency, improved quality, greater flexibility, lower costs, and a competitive advantage in a rapidly changing market.
Overall, an FMS is a highly advanced and complex manufacturing system that is designed to be responsive to changing production requirements and is capable of producing high-quality products with minimal human intervention.
>>>> See also: ERP for Manufacturing

What is Flexible Manufacturing System?
>>>> Read More: Lean manufacturing System
Who invented the Flexible Manufacturing System?
The concept of a Flexible Manufacturing System (FMS) was first introduced by Joseph Harrington in the late 1960s. Harrington was a professor of industrial engineering at Purdue University in the USA.
He proposed the idea of a manufacturing system that could be reprogrammed and reconfigured quickly to produce a variety of products, in order to meet changing customer demands. The first FMS was implemented in the 1970s by Westinghouse Electric Corporation in the USA.
>>>> See More: MRP software
Will the future be impacted by Flexible Manufacturing Systems?
To the cost-saving benefits and increased productivity, FMS offer several long-term advantages for manufacturers. As technology evolves, FMS will become more adaptable and responsive to changing customer demands, enabling them to quickly switch between different products or services without needing time-consuming retooling or reconfiguration processes that are common in traditional manufacturing methods.
FMS is also expected to play a significant role in advancing Industry 4.0, the fourth industrial revolution. This will involve integrating digital technologies such as artificial intelligence, machine learning, and data analytics to connect machines and factories to smart systems that can optimize production processes in real-time. FMS will be at the forefront of this shift towards a more dynamic and interconnected manufacturing sector.
Moreover, FMS provides manufacturers with deeper insights into their operations, including better visibility over supply chain management, product development, and inventory control. This information is instrumental in helping manufacturers remain competitive in the industry beyond 2023.
In conclusion, FMS is a critical component of the future of manufacturing, leveraging automation to provide greater flexibility and efficiency while providing deeper insights into operations. Manufacturers looking to stay competitive in the increasingly digital world must utilize the benefits of FMS to improve their productivity and reduce costs.

The technology can help to improve efficiency, quality, and flexibility in manufacturing
>>>> Read More: What is an MES system
Advantages of Flexible Manufacturing System?
There are several advantages to implementing a Flexible Manufacturing System (FMS), including:
- Increased efficiency: An FMS allows for greater automation and integration of manufacturing processes, which can lead to increased productivity and reduced lead time.
- Improved quality: An FMS can be programmed to perform quality control checks at various points in the manufacturing process, which can help to identify defects or errors before they become major problems.
- Greater flexibility: As the name suggests, an FMS is designed to be flexible, which means that it can be quickly reconfigured to produce different products or handle different production volumes. This can be especially beneficial in industries where demand is highly variable.
- Lower costs: By automating many manufacturing process, an FMS can help to reduce labor costs and minimize waste, which can translate into significant cost savings over time.
- Competitive advantage: Companies that implement FMS technology can gain a competitive advantage by being able to quickly adapt to changing market conditions and customer demands.
An example of an FMS in action might be a manufacturer of automotive parts. By implementing an FMS, they are able to quickly switch from traditional manufacturing to agile manufacturing - producing one type of part to another, depending on the needs of their customers.
Additionally, the FMS can help to ensure that each part is manufactured to the highest possible quality standards, which can improve customer satisfaction and build brand loyalty.

This allows them to respond quickly to shifts in demand.
>>>> Apply Now With: Food production management software
Disadvantage of Flexible Manufacturing System?
While there are several advantages to implementing a Flexible Manufacturing System (FMS), there are also some potential disadvantages that should be taken into consideration, including:
- High initial cost: Setting up an FMS can require a significant investment in equipment, software, and training. This initial cost may be prohibitive for some companies, particularly smaller ones.
- Complex programming: FMS technology requires sophisticated software programming and engineering expertise, which can be challenging for some organizations to implement and maintain.
- Vulnerability to breakdowns: Because an FMS relies on a complex network of interconnected machines and systems, a breakdown in one part of the system can have ripple effects throughout the entire process, leading to delays and downtime.
- Need for skilled labor: To operate and maintain an FMS, companies need employees with specialized skills and knowledge, which may be in short supply or require additional training.
- Limited customization: While an FMS is designed to be flexible, there may be limits to how much customization is possible within the system, which can limit its usefulness in certain applications.

It's important for companies to carefully weigh the advantages and disadvantages
What Are Some Examples Of Flexible Manufacturing Systems?
There are several examples of FMS used in various industries. Here are a few examples:
- Automotive industry: One example of an FMS used in the automotive industry is the machining of engine blocks and cylinder heads. The FMS consists of a series of computer-controlled machining centers that can produce engine blocks and cylinder heads of different sizes and specifications with minimal human intervention.
- Aerospace industry: In the aerospace industry, FMS technology is used to produce components for aircraft engines, such as turbine blades and compressor disks. The FMS consists of several automated machining centers that can produce these components to high precision with minimal human intervention.
- Electronics industry: An example of an FMS in the electronics industry is the production of printed circuit boards (PCBs). The FMS consists of several machines that can perform different operations, such as drilling, routing, and plating, on PCBs of different sizes and complexity. The FMS can quickly reconfigure itself to produce different types of PCBs as needed.
- Consumer goods industry: An example of an FMS used in the consumer goods industry is the production of furniture. The FMS consists of several machines, such as CNC routers, that can produce furniture components of different sizes and designs. The FMS can quickly reconfigure itself to produce different types of furniture as needed.
- Medical device industry: In the medical device industry, FMS technology is used to produce components for surgical instruments, such as blades and handles. The FMS consists of several automated machining centers that can produce these components to high precision with minimal human intervention.
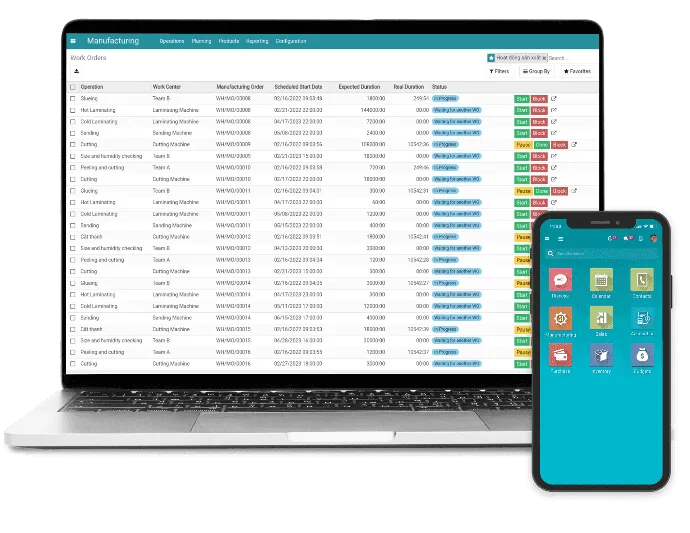
Viindoo MRP - Comprehensive Software Solution for Manufacturing
FREE FOREVER
Manage Your Manufacturing Process on a Single Platform!
Flexible Manufacturing Systems (FMS) is already having a major impact on the future of manufacturing. By 2023, FMS will be an indispensable tool for many companies. Using robots, computer numerical control machines, and other automation technologies, FMS can significantly improve production efficiency and reduce labor costs. Follow Viindoo for more intelligent and comprehensive software in order to solve your business problems
>>>> Continue With:
FAQs
What industries are FMS commonly used in?
FMS is commonly used in industries such as automotive, aerospace, electronics, and consumer goods.
Can FMS be integrated with other manufacturing systems?
Yes, FMS can be integrated with other manufacturing systems, such as computer-aided design (CAD) and computer-aided manufacturing (CAM).
How long does it take to implement an FMS?
The implementation time for an FMS varies depending on the complexity of the system and the size of the company. On average, it can take anywhere from six months to two years.
What is the cost of implementing an FMS?
The cost of implementing an FMS varies depending on the size and complexity of the system. On average, it can range from $500,000 to $5 million.
What are some challenges that come with implementing an FMS?
Some challenges that come with implementing an FMS include technical complexity, the need for skilled technicians, and the potential for downtime during the implementation process.