The application of IoT in manufacturing is revolutionary, poised to transform the industry's landscape for those who are pioneers in the digital revolution. This shift, driven by the advent of super-cheap computer chips and the ubiquity of wireless networks, makes it possible to turn anything, from a pill to an airplane, into a part of the IoT. This transformation has made IoT an essential element in daily life and various business sectors. It's not just about optimizing manufacturing processes, IoT for manufacturing extends to improving product quality, ensuring workplace safety, and supporting sustainable practices.
This blog post delves into the transformative impact of IoT in the manufacturing sector, covering the integration of IoT factory technologies, process automation, and intelligent supply chain management.
So, what is IoT?
IoT stands for the Internet of Things. It describes devices equipped with sensors, processing abilities, software, and other technologies that connect and exchange data with other devices and systems over the internet. These devices range from ordinary household items to complex industrial tools. Simply put, IoT is a network of physical objects connected to the internet that can communicate with each other and with other systems.

The Internet of Things, or IoT, refers to the billions of physical devices around the world now connected to the internet, all collecting and sharing data. Thanks to the advent of super-cheap computer chips and the ubiquity of wireless networks, it's possible to turn anything, from a pill to an airplane, into a part of the IoT. Connecting all these different objects and adding sensors to them adds a level of digital intelligence to devices that would otherwise be dumb, enabling them to transmit data in real-time without human intervention. The Internet of Things is making the fabric of the world around us smarter and more responsive, merging the physical and digital universes.

The speed of growth of IoT devices
Understanding IoT in Manufacturing
The integration of the Internet of Things (IoT) in manufacturing involves the deployment of sensors and devices throughout the production process to collect and transmit data in real-time. This data can encompass a variety of metrics, including temperature, humidity, air quality, energy consumption levels, machine performance, environmental conditions, and product quality. Such real-time data analysis can identify patterns, trends, and anomalies, aiding businesses in optimizing operations and enhancing profitability. This fosters increased automation, reduces production times, improves product quality, and lowers operational costs. Leveraging this data provides manufacturers with valuable insights that drive informed decision-making.

IoT collects data
Data in the manufacturing
In any typical manufacturing process, additional crucial data regarding various assets and resources is generated as part of the production chain but often goes unnoticed or uncollected. This includes operational data, asset conditions, performance metrics, usage patterns, maintenance schedules, logistics, and resource usage (such as water and minerals), along with information on key external factors like temperature, humidity, input materials, and transportation methods.
The potential applications of IoT are vast and varied, with its impact already profoundly felt across multiple industries, including manufacturing, transportation, healthcare, and agriculture. As the number of internet-connected devices continues to grow, IoT is set to play an increasingly significant role in shaping our world, transforming how we live, work, and interact with one another.
What advantages does IoT offer in manufacturing?
The manufacturing industry, traditionally driven by innovation, is currently undergoing the fourth industrial revolution, or 'Industry 4.0'. Technological advancements in manufacturing, fueled by modern sensors, actuators, and robots, have revolutionized areas such as supply chain, transportation, communication, housing, energy, and manufacturing.
For businesses to thrive in the manufacturing sector, they must make precise and timely decisions based on reliable and proven information. Such a workflow can be achieved by leveraging the advanced capabilities of IoT in manufacturing, including machine learning, big data, and automation technologies, which enable the creation of a system within a system.
Viindoo presents some benefits that IoT brings to your business:
Manufacturing KPIs
IoT technology significantly enhances manufacturing efficiency by connecting machines to the internet, providing real-time insights into their health and key performance indicators (KPIs) such as Overall Equipment Effectiveness (OEE) and Overall Process Effectiveness (OPE). This connectivity allows manufacturers to identify and address causes of unplanned downtime, optimize machine utilization through preventive maintenance, and improve overall production performance. Additionally, the use of KPIs offers valuable insights into business effectiveness, enabling manufacturers to focus on critical aspects for improvement. By tracking, analyzing, and optimizing these KPIs over time, businesses can guide decision-making, streamline operations, and ensure they are moving in the right direction. IoT platforms play a crucial role in compiling and contextualizing data into simplified reports and dashboards, reducing the time and effort needed to assess performance alignment with expectations, ultimately enhancing operational efficiency and business productivity.

Manufacturing KPI example
Predictive maintenance
Machine downtimes and damages can critically impact manufacturing companies, and they can also pose dangers to frontline workers.
Real-time data from IoT-connected systems can aid in predicting defects in machinery. This enables manufacturers to implement preventative measures against potential issues before they occur, ultimately leading to increased machine uptime and enhanced overall productivity. Preventing equipment failures helps reduce processing time, rework, scrap, and unplanned downtime. These improvements assist manufacturers in saving on associated costs.

Applying IoT in manufacturing to collect and analyze maintenance forecasts
Improved Production Planning and Scheduling
Adding to this, experience shows that companies with superior production planning capabilities consistently achieve better production efficiency. Effective planning invariably requires access to comprehensive and accurate information regarding the manufacturing process and market conditions. The integration of IoT technology plays a pivotal role in gathering this vital data, ensuring that planning is based on the most current and precise information available. This not only streamlines the production process but also significantly improves a company's ability to respond to market trends and demands, ultimately leading to a more competitive and productive manufacturing operation.

Applying IoT in manufacturing for more accurate planning
Remote control
Integrating IoT into manufacturing revolutionizes how central control rooms operate, granting them the capability to oversee numerous devices, production lines, or entire factories with unprecedented ease and efficiency. This digital transformation eliminates geographical barriers, enabling expert analysts to contribute their skills remotely, without the time and expense associated with physical travel. A particularly innovative application of this technology is the direct sharing of machinery data with the equipment's manufacturers. This facilitates a more focused approach to production, where the operational teams can concentrate on optimizing processes rather than being bogged down by concerns over machinery performance or maintenance.
Moreover, this collaboration with equipment manufacturers isn't just about offloading the task of monitoring; it's about enriching the production ecosystem with deep insights and predictive analytics. These manufacturers, leveraging the comprehensive data collected via IoT, can provide not only real-time analysis but also proactive maintenance alerts. This predictive capability ensures potential issues can be addressed before they escalate, dramatically reducing downtime and enhancing overall productivity.
This model of interconnected manufacturing not only streamlines operational efficiency but also fosters a culture of continuous improvement and innovation. By harnessing the full potential of IoT, manufacturers can achieve a more agile, resilient, and responsive production environment, one that is better equipped to adapt to the demands of the modern market and the challenges of future growth.

Remote control and data sharing in IoT
Supply chain management (SCM)
The integration of IoT in supply chain management transcends traditional methodologies by offering real-time data analytics, predictive maintenance for logistics infrastructure, and automated decision-making capabilities. This technology facilitates seamless communication between devices, enabling a more synchronized operation across the supply chain. It allows for the implementation of advanced tracking systems that not only monitor the physical conditions of goods, such as temperature and humidity, to ensure product integrity but also enable geo-fencing features that alert managers to unauthorized movements, further securing the supply chain.

Application of IoT in supply chain management
Moreover, IoT-driven supply chains benefit from enhanced visibility and connectivity, leading to more informed decision-making and strategic planning. By leveraging data collected from IoT devices, businesses can predict trends, anticipate demand fluctuations, and adjust their strategies accordingly, ensuring a more dynamic and resilient supply chain.
Additionally, IoT contributes to sustainability in supply chain operations by optimizing routes to reduce fuel consumption and carbon emissions, and by monitoring energy use within warehouses, contributing to environmental conservation efforts. The integration of IoT not only streamlines operations but also promotes a more sustainable and responsible supply chain management approach.
In summary, IoT revolutionizes supply chain management by providing comprehensive tracking, improved efficiency, and strategic insights, which collectively enhance operational performance, profitability, and sustainability. As technology continues to evolve, the potential for IoT in transforming supply chain practices becomes increasingly significant, marking a new era of intelligent, responsive, and sustainable supply chain management.
Discover Viindoo's IoT in Manufacturing
Viindoo's IoT in Manufacturing platform is professionally designed for seamless data collection and analysis. This provides deep insights and accurate analysis of differentiating factors in the manufacturing process, significantly enhancing operational efficiency.
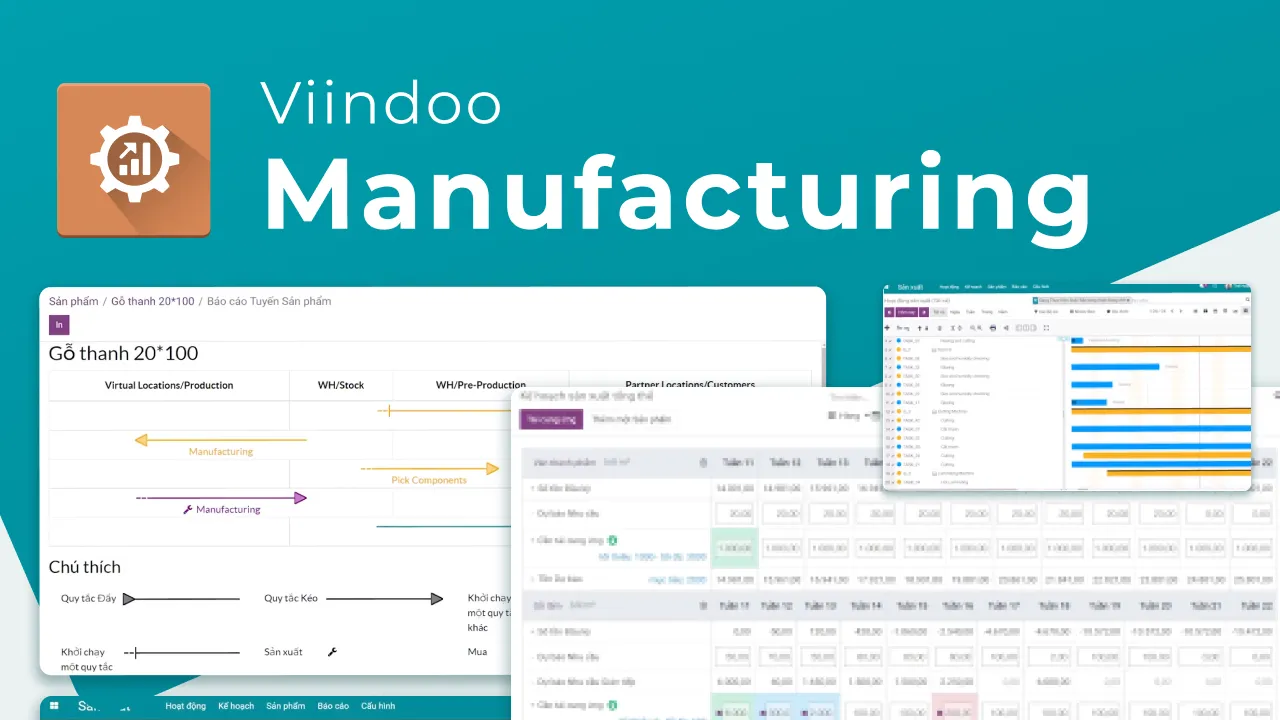
Viindoo Manufacturing with IoT integration
Conclusion
The global IoT market is experiencing strong growth. Implementing IoT in manufacturing enables businesses to increase productivity, swiftly meet customer demands, comply with environmental and safety requirements, extend the lifespan of equipment, and more.
If you are unsure which IoT solution to implement, our company is ready to assist you. Viindoo is a software development company with extensive experience in the field of enterprise management software development on the ERP platform, including the integration of IoT in manufacturing processes. We help companies simplify complex issues with the aid of advanced technologies.
FAQs
IoT in manufacturing refers to the integration of interconnected devices and sensors to collect and exchange data, enabling real-time monitoring and optimization of production processes.
The implementation of IoT in manufacturing brings numerous benefits to businesses. Specifically, some benefits include manufacturing KPIs, predictive maintenance, Improved production planning and scheduling, remote control, quality control, etc
IoT can enhance manufacturing efficiency by intelligently monitoring and controlling devices and production processes. IoT sensors can provide real-time data on the operational status of machinery, helping to prevent malfunctions and minimize production downtime.
My company Viindoo has modules supporting the connection of sensors, data collection devices, control devices, etc., to the ERP platform.