Kaizen in Manufacturing: Constantly seeking efficiency gains, manufacturers turn to the Japanese principle of continuous improvement. Explore how this philosophy can be integrated into manufacturing processes using ERP systems like Viindoo.
Introduction to Kaizen in Manufacturing
Kaizen originated in Japan after World War II as a way to rebuild the country's economy. It was first introduced by Toyota as part of their lean manufacturing philosophy, but has since been adopted by companies all over the world. The core principle of kaizen is to continuously strive for improvement, no matter how small the changes may be.
In the context of manufacturing, kaizen involves identifying and eliminating waste in all aspects of production, from materials and resources to time and energy. This leads to increased efficiency, reduced costs, and improved quality. By implementing kaizen, manufacturers can create a culture of continuous improvement within their organization, leading to long-term success.
Kaizen Principles for Continuous Improvement
There are several key principles that guide the kaizen approach to continuous improvement:
Focus on Small, Incremental Changes
The first principle of kaizen is to focus on making small, incremental changes rather than large, sweeping ones. This allows for easier implementation and reduces the risk of disrupting the entire production process. By making small improvements over time, manufacturers can achieve significant results without causing major disruptions to their operations.
Involve Everyone in the Process
Another important principle of kaizen is to involve everyone in the organization in the improvement process. This includes not only management and employees, but also suppliers and customers. By involving all stakeholders, manufacturers can gain valuable insights and ideas for improvement from different perspectives.
Continuously Review and Improve Processes
Kaizen is an ongoing process that requires constant review and improvement. This means that manufacturers should regularly evaluate their processes and look for ways to make them more efficient and effective. By continuously reviewing and improving processes, manufacturers can stay ahead of the competition and adapt to changing market conditions.
Kaizen Tools and Techniques for Manufacturing
In order to implement kaizen in manufacturing, there are several tools and techniques that can be used to identify and eliminate waste. These include:
Value Stream Mapping
Value stream mapping is a visual tool used to analyze and improve the flow of materials and information through the production process. It involves mapping out all the steps involved in producing a product, from raw materials to finished goods, and identifying areas where waste can be eliminated.
5S Methodology
The 5S methodology is a system for organizing and maintaining a clean and efficient workplace. The five S's stand for Sort, Set in Order, Shine, Standardize, and Sustain. By following these steps, manufacturers can create a more organized and productive work environment.
Kanban System
The kanban system is a method for managing inventory and production levels. It involves using visual signals, such as cards or bins, to indicate when materials should be replenished or when production should be started. This helps to prevent overproduction and reduce waste.
Implementing Kaizen in Manufacturing with ERP Systems
Enterprise Resource Planning (ERP) systems are software solutions that integrate various business functions, such as accounting, inventory management, and production planning. These systems provide a centralized platform for managing all aspects of a manufacturing operation. By incorporating kaizen principles into ERP systems, manufacturers can further enhance their continuous improvement efforts.
Customization and Flexibility
One of the key benefits of ERP systems is their ability to be customized to meet the specific needs of a manufacturing operation. By incorporating kaizen principles into the customization process, manufacturers can ensure that their ERP system supports their continuous improvement efforts. This may include features such as real-time data analysis, automated workflows, and customizable reporting.
Streamlined Processes
ERP systems can help to streamline processes by automating tasks and eliminating manual data entry. This not only saves time and reduces the risk of errors, but also allows for a more efficient production process. By continuously reviewing and improving these processes, manufacturers can further increase efficiency and reduce waste.
Real-Time Data Analysis
Another advantage of ERP systems is their ability to provide real-time data analysis. This allows manufacturers to monitor key performance indicators (KPIs) and identify areas where improvements can be made. By using this data to drive decision-making, manufacturers can make more informed and strategic decisions to support their kaizen efforts.
Optimizing Workflow: Implementing Kanban System with Viindoo ERP
The first step in implementing a Kanban system with Viindoo ERP is to identify the existing workflow processes within the organization. This involves mapping out the various stages of production, service delivery, or project management. By understanding the flow of work, it becomes easier to create a Kanban board within Viindoo that accurately represents these processes.
Once the workflow stages are identified, the next step is to configure the Kanban card within Viindoo to reflect these stages. Viindoo provides customizable features that allow users to create boards tailored to their specific workflow requirements. Each stage of the process can be represented as a column on the Kanban board, providing a visual representation of the work as it progresses through the system.
One of the key benefits of integrating Kanban with Viindoo ERP is the real-time visibility it provides. Team members can easily track the status of tasks, identify bottlenecks, and prioritize work based on actual demand. This transparency fosters collaboration and empowers teams to make informed decisions to keep the workflow moving smoothly.
Additionally, the use of Kanban within Viindoo facilitates the implementation of pull-based systems, where work is pulled only when there is capacity, rather than pushed onto the next stage. This helps in reducing overburdening of resources and ensures a more balanced workflow.
Furthermore, Viindoo's flexibility allows for the adaptation of the Kanban system to different departments and processes within the organization. Whether it's managing sales pipelines, tracking production stages, or handling service requests, Viindoo's modular structure and customizable Kanban boards make it suitable for diverse business functions.
Kanban interface, visually displaying tasks, provides invaluable support for the Kanban system
Kaizen in Manufacturing: Value Stream Mapping with Viindoo MRP
Viindoo MRP - ERP System provides a comprehensive platform for managing various aspects of manufacturing, including inventory, production planning, scheduling, quality management, and more. Integrating Value Stream Mapping with Viindoo MRP allows businesses to align their strategic goals with operational processes, leading to improved resource utilization, reduced lead times, and enhanced product quality.
When implementing Value Stream Mapping with Viindoo MRP, the first step is to thoroughly understand the existing manufacturing processes. This involves mapping out each stage of production, from receiving orders to shipping finished products. With Viindoo's user-friendly interface, this information can be easily input into the system, allowing for a clear visualization of the entire value stream.
Once the current state is mapped out, the next step is to identify areas for improvement. This could include reducing inventory levels, optimizing production flow, or minimizing downtime. By leveraging Viindoo's MRP capabilities, businesses can analyze production data, track material usage, and monitor machine performance, enabling them to pinpoint bottlenecks and inefficiencies within the manufacturing process.
After identifying improvement opportunities, businesses can use Viindoo MRP to simulate and evaluate different scenarios for process optimization. This may involve adjusting production schedules, reorganizing workstations, or implementing new technologies. The system's robust features allow for the modeling of these changes, providing insights into potential outcomes before actual implementation.
Furthermore, Viindoo MRP facilitates the implementation of lean manufacturing principles, such as Just-In-Time (JIT) production and continuous improvement. By integrating Value Stream Mapping with Viindoo's ERP system, businesses can establish a culture of ongoing refinement, where employees are empowered to suggest and implement process improvements based on real-time data and feedback.
In addition, Viindoo's MRP system offers seamless integration with other business functions, such as sales, procurement, and accounting. This interconnectedness enables a holistic view of the entire value chain, allowing for better coordination between departments and ensuring that manufacturing processes are aligned with market demand and supply chain dynamics.
Understand the Product Life Cycle Leveraging Data and Control with Value Stream Mapping in Viindoo ERP
Measuring Success with Kaizen in Viindoo MRP
Viindoo MRP is an ERP system specifically designed for manufacturing companies. It offers a range of features and modules to support all aspects of the production process, from inventory management to quality control. When implementing kaizen in Viindoo MRP, it is important to establish metrics and benchmarks to measure the success of the continuous improvement efforts.
Some key metrics that can be used to measure the success of kaizen in Viindoo MRP include:
- Reduction in lead times : By continuously improving processes, manufacturers can reduce the time it takes to produce a product, leading to faster delivery times and increased customer satisfaction.
- Increase in productivity: Kaizen aims to eliminate waste and improve efficiency, which can result in increased productivity. By tracking productivity levels before and after implementing kaizen, manufacturers can see the impact of their efforts.
- Cost savings: By reducing waste and improving efficiency, kaizen can lead to cost savings for manufacturers. This can be measured by comparing costs before and after implementing kaizen.
- Quality improvements: Kaizen also focuses on improving quality by eliminating defects and errors. By tracking the number of defects and customer complaints, manufacturers can see the impact of their continuous improvement efforts.
Discover Viindoo Manufacturing Software
The All-in-one Software for Manufacturers. Provides all manufacturing reports and powerful visualization data necessary for implementing Kaizen.
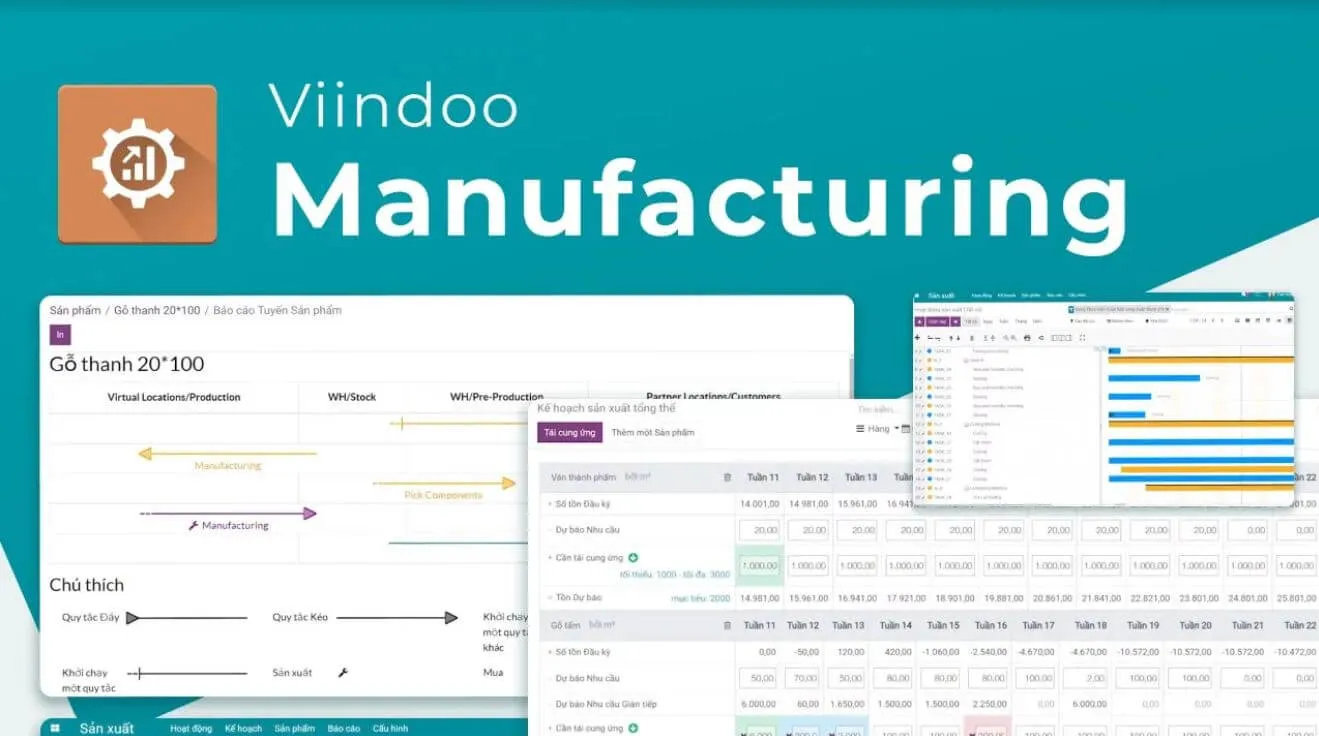
FAQ
A: Yes, kaizen can be applied to any type of manufacturing industry, from automotive to food production. The principles of kaizen are universal and can be tailored to fit the specific needs of each industry.
A: While an ERP system is not a requirement for implementing kaizen, it can greatly enhance the process by providing real-time data analysis and streamlining processes. However, kaizen can also be implemented using other tools and techniques without an ERP system.
A: The timeline for seeing results from kaizen will vary depending on the size and complexity of the manufacturing operation. However, by focusing on small, incremental changes, manufacturers can start to see improvements within a few weeks or months.
Conclusion
In today's competitive manufacturing landscape, continuous improvement is essential for success. By implementing kaizen principles and tools, manufacturers can create a culture of continuous improvement within their organization. By incorporating these principles into ERP systems, such as Viindoo MRP, manufacturers can further enhance their efforts and achieve significant results over time. By continuously reviewing and improving processes, measuring success, and involving all stakeholders, manufacturers can stay ahead of the competition and achieve long-term success with kaizen.