Backorders are a common phenomenon in many businesses, where demand for a product exceeds the available inventory. This situation can arise due to multiple factors such as sudden increases in sales, disruptions in the supply chain, or inaccurate forecasting. Dealing with backorders poses a challenge for businesses striving to meet the demands with limited stock on hand.
In this article, we will take an in-depth look at backorders and their significance across businesses. We will also explore how Viindoo offers a solution for managing backorders efficiently. So, let's dive in!
What is a Backorder?
A backorder is an order for products that are not currently in stock. This order is not limited to a sales order, but can also be a transfer order, or a manufacturing order, etc. Instead of canceling the order outright, we accept it and promises to deliver the item once it becomes available again. For instance, if a customer orders 10 widgets but only 5 are in stock, we will ship 5 widgets first, and a backorder for the remaining 5 widgets is created.
Backorders serve as a commitment to fulfill the order once the product becomes available again. This practice enables businesses to continue accepting orders even when immediate inventory fulfillment isn't possible, thereby preserving customer satisfaction, preventing potential sales loss, and maintain a seamless supply chain process .
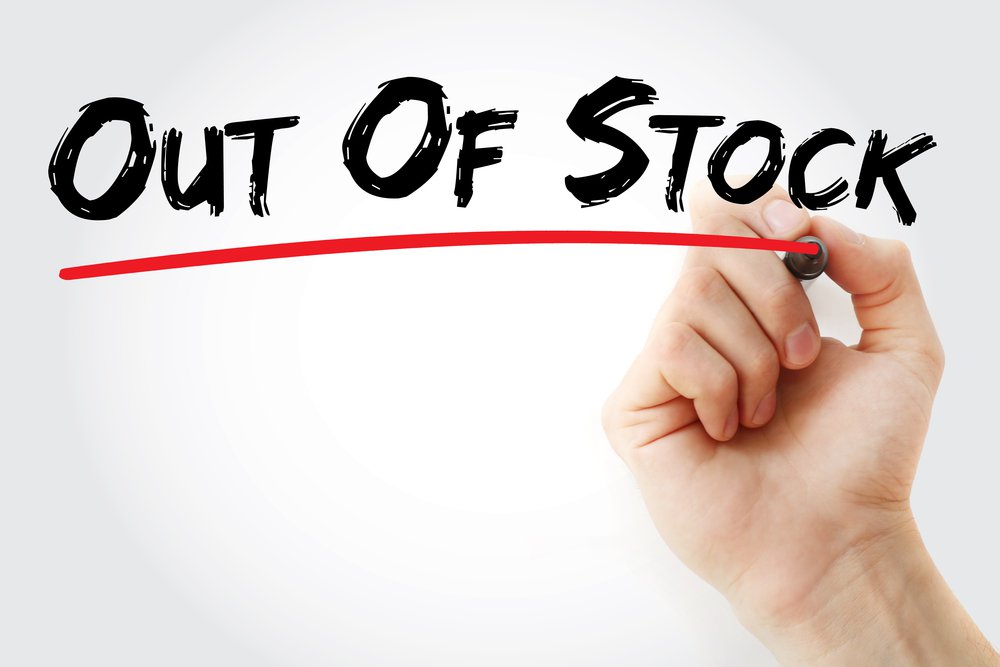
Reasons for Backorders
Several factors can contribute to backorders across businesses:
- Unexpected Increase in Demand: Sudden spikes in demand due to events like marketing campaigns or social media exposure can catch businesses off guard, resulting in backorders.
- Supply Chain Disruptions: Delays in production, transportation issues, or supplier shortages can disrupt the supply chain, leading to backorders.
- Inaccurate Forecasting: Underestimating product demand due to lack of real-time data or reliance on outdated forecasting methods can result in backorders.
Impact of Backorders
Backorders can have both positive and negative impacts on businesses:
- Positive Impact: They enable businesses to continue accepting orders, maintaining customer satisfaction and avoiding sales loss without overstocking inventory.
- Negative Impact: Poorly managed backorders can lead to dissatisfied customers, lost sales, and increased costs such as expedited shipping fees.
Backorders Management with Viindoo
Viindoo offers a comprehensive solution for managing backorders efficiently. Let's take a closer look at how this app works and its features.
About Viindoo
Viindoo is an all-in-one business management software that offers a range of applications for different business functions such as accounting, sales, inventory, and more. With Viindoo, businesses can effectively manage many aspects, boosting efficiency and driving growth.
Understanding Backorders in Viindoo
Before delving into the configuration of automatic backorders, it's essential to grasp the fundamental concept. There are two types of backorder in Viindoo:
- Inventory Transfer Backorders: These backorders often occur when there's a shortage of stock to fulfill a transfer request from one location to another. Typically linked to the sales flow, when a customer places an order for a product unavailable in their preferred location, a transfer order is initiated. If there's insufficient stock at the source location, a backorder arises.
- Manufacturing Backorders: Arising from raw material shortages or capacity constraints hindering production completion within the scheduled timeframe, these can disrupt production schedules. Manufacturing backorders are closely linked to the purchase flow, as when a manufacturing order is created, corresponding purchase orders for raw materials are generated. If procurement delays or insufficient quantities occur, manufacturing backorders may arise.
In both scenarios, whether it's inventory transfer backorders or manufacturing backorders, Viindoo provides robust tools to manage and resolve these issues effectively. By integrating inventory management, sales, procurement, and manufacturing processes, Viindoo enables businesses to streamline operations, optimize resource utilization, and enhance customer satisfaction.
Configuring Automatic Transfer Backorders
First, let's learn about Inventory Transfer Backorders in Viindoo. Viindoo Inventory app provides a feature that allows users to flexibly configure the automatic generation of backorders. This functionality is governed by picking policies, dictating how orders are handled when inventory falls short. Two primary policies guide this process:
- Ship Products as Soon as Available, with Back Orders: This policy allows businesses to expedite order fulfillment by shipping available products while automatically generating backorders for the remaining items.
- Ship All Products at Once: In contrast to the above policy, this method requires order confirmation only when all products in the order are available, not supporting the creation of backorders.

Now, let's navigate through the Operation Types configuration to leverage the potential of automatic backorders efficiently. Under each types, users are provided with three distinct options to manage backorders:
- Ask Option: When selecting the Ask option, users are presented with a pop-up notification when encountering insufficient inventory. This allows users to make informed decisions regarding backorder creation, aligning with their business needs.
- Always Option: Opting for the Always method streamlines the process by automatically generating backorders, eliminating manual intervention. This ensures a smooth workflow, especially in high-volume sales environments.
- Never Option: Conversely, selecting the Never option ensures consistency by canceling the remaining products without generating backorders. While this method may lack the flexibility of creating backorders, it provides a swift solution to inventory management conflicts.
These options can be applied to all types of operations like delivery orders, receipts, returns, manufacturing, etc.

Through Viindoo interface, users can view the list of backorders, their references, transfer statuses, and delivery information. This visibility ensures efficient order management and timely fulfillment.

Discover Viindoo Inventory Software
The All-in-one Inventory Software for SMEs. Automate backorder management to optimizes processes, ensures customer satisfaction, and maximizes profits.
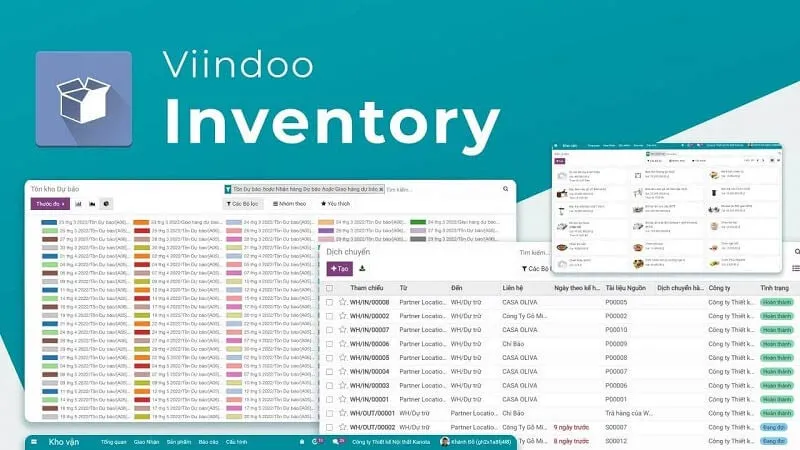
Creating Manufacturing Backorders
Manufacturing backorders occur when the full quantity of a manufacturing order cannot be produced immediately. Instead of halting production altogether, Viindoo Manufacturing app allows for the creation of partial quantities while generating a backorder for the remaining amount.
Creating a manufacturing backorder in Viindoo has never been easier with following several simple steps:
- Navigate to manufacturing orders: Begin by navigating to the Manufacturing app and selecting the desired manufacturing order.
- Confirm manufacturing order: Confirm the manufacturing order, ensuring the quantity reflects the units being produced immediately.
- Validation and backorder creation: Click Validate, and if the produced quantity is less than the initial demand, a pop-up window will appear. From here, you can create a backorder, splitting the order into two separate entities.
- Management of orders: The initial order containing the manufactured items is closed immediately, while the backorder remains open until the remaining units can be manufactured.

Strategies to Avoid Backorders
While backorders can be managed efficiently with the help of Viindoo, it is always better to avoid them in the first place. Here are some strategies that businesses can adopt to prevent backorders:
- Accurate Forecasting: Investing in reliable forecasting methods ensures optimal inventory levels, reducing the likelihood of backorders.
- Real-time Inventory Tracking: Utilizing tools like Viindoo for real-time inventory tracking enables informed decision-making and proactive restocking.
- Safety Stock: Maintaining safety stock cushions against unexpected demand spikes, mitigating the risk of backorders.
- Supplier Relationships: Cultivating strong supplier relationships facilitates timely deliveries, minimizing supply chain disruptions and potential backorders.
Conclusion
Backorders present a common challenge across businesses, but they can be managed efficiently with the right tools and strategies. Viindoo offers a comprehensive solution for managing backorders, allowing businesses to navigate the complexities of inventory demands, avoiding negative impacts and sustaining customer satisfaction.
FAQ
Yes, backorders can be created manually in Viindoo by selecting the Create Backorder option in the delivery order or receipt form.
Yes, backorders can be canceled in Viindoo by selecting the Cancel Backorder option in the delivery order or receipt form.
Yes, backorders can be tracked in Viindoo through the Backorders tab in the Inventory app. This provides an overview of all the backorders and their status.
Yes, Viindoo software is highly customizable and can be tailored to meet the specific needs of small businesses. It is also cost-effective, making it an ideal solution for small businesses.
Yes, the picking policy can be customized in Viindoo to suit the specific needs of a business. This can be done through the configuration settings in the Inventory app.