Delivery Schedule stands at the forefront of supply chain management, embodying the critical rhythm that drives business operations across various sectors. This crucial aspect of logistics not only concerns the transportation of goods from one location to another but emphasizes executing this task with utmost efficiency, promptness, and cost-effectiveness. It's a sophisticated balancing act that necessitates meticulous coordination of inventory management, order processing, route optimization, and communication with customers.
In an era where the pace of business is ever-accelerating and consumer expectations continually rise, mastering delivery schedules ensures that companies can reliably provide the right product, at the right place, at precisely the right time, distinguishing themselves in a competitive marketplace.
Understanding Delivery Schedule
Definition and Importance
Delivery schedule, at their essence, are structured timelines that outline when and how goods are transported from suppliers to end customers. This systematic approach to managing deliveries is vital for maintaining the fluidity and efficiency of supply chain operations. It encompasses a series of planned actions, from order placement to the final delivery, ensuring that products reach their destination within the agreed timeframe.
The role of delivery schedules extends beyond mere logistics; they are foundational to achieving high levels of customer satisfaction. In today's digital era, where immediacy is often expected, the ability to reliably predict and meet delivery times can significantly influence customer perceptions and loyalty. A well-orchestrated delivery schedule not only ensures that products are available when needed but also helps in building trust between businesses and their customers. It signals to customers that a company is reliable and committed to providing quality service, thereby enhancing the overall customer experience.
In supply chain management, delivery schedules are crucial for streamlining operations and optimizing resource allocation. They allow businesses to plan ahead, ensuring that inventory levels are maintained efficiently, warehouse operations are smooth, and transportation resources are used effectively. By minimizing delays and maximizing delivery efficiency, companies can reduce operational costs, improve turnaround times, and increase profitability.
>>>> See more: Mastering Inventory Forecasting: Strategies for Anticipating Demand and Optimizing Supply Chains
Challenges in Delivery Scheduling
Despite their importance, crafting and adhering to effective delivery schedules is fraught with challenges. One of the primary obstacles is the unpredictability of external factors such as traffic congestion, adverse weather conditions, and unexpected delays in customs or regulatory approvals. These elements can disrupt even the most meticulously planned schedules, necessitating constant adjustments and flexibility.
Another significant challenge lies in balancing on-hand inventory with delivery schedules. Overstocking to ensure product availability for delivery can lead to increased storage costs and potential wastage, whereas understocking might result in stockouts and delayed deliveries, adversely affecting customer satisfaction.
Furthermore, the increasing demand for customized delivery options poses a complex challenge. Today's consumers often expect various delivery choices, including express shipping, time-slot deliveries, and eco-friendly options. Meeting these expectations requires sophisticated scheduling capabilities and can significantly complicate the delivery process.
Moreover, the coordination between multiple stakeholders, including suppliers, logistics providers, and retailers, adds another layer of complexity. Ensuring that all parties are aligned and that information flows seamlessly between them is essential for maintaining accurate and efficient delivery schedules.
How to plan Delivery Schedules?
Practical example
The example illustrates how to plan delivery schedule using various lead times collaboratively ensure the on-time fulfillment of orders.
- Sales security lead time: 1 day
- Purchase security lead time: 1 day
- Vendor lead time: 4 days
- Manufacturing security lead time: 2 days
- Manufacturing lead time: 3 days
- September 1st: a sales order is confirmed.
- September 9th: components must be ordered to meet a 4-day vendor lead time.
- September 13t: the components' arrival.
- September 14th: manufacturing must start.
- September 19th: delivery, a day ahead of the original September 20th schedule due to sales security lead time adjustments.
These lead times, when applied in sequence, provide a structured timeline for each phase of the order process, from order placement to final delivery, highlighting the importance of each lead time in achieving efficient and timely order fulfillment.
So, how to automate them using management software?
Step-by-Step Guide
In Viindoo, accurately setting up delivery schedules is essential for meeting customer expectations and streamlining business operations. Viindoo Inventory app facilitates this through advanced lead time configurations, allowing effective coordination and planning of manufacturing orders, deliveries, and receptions.
The system incorporates various lead times, including customer lead time, sales security lead time, purchase lead time, and more, to ensure timely and efficient delivery processes.
In Viindoo, managing lead time is crucial for the order fulfillment process. Types of lead times include:
- Sales lead times
- Customer Lead Time: The period from when a sales order is confirmed to when products are shipped.
- Sales Security Lead Time: Adds extra days to the delivery date for preparation against delays.
- Purchase lead times
- Purchase Lead Time: The time from purchase order confirmation to product receipt.
- Purchase Security Lead Time: Moves the order deadline forward to mitigate vendor or shipping delays.
- Manufacturing lead time
- Manufacturing Lead Time: The duration to complete a manufacturing order, including non-working days.
- Manufacturing Security Lead Time: Advances the manufacturing order date for early replenishment.
Sales lead times
In Viindoo, you can set customer lead times and sales security lead times to automatically determine an expected delivery date on a Sales Order (SO), ensuring shipments have realistic delivery schedules. Viindoo will alert you if a chosen delivery date is too soon, potentially affecting the ability to fulfill the order and impacting warehouse operations.
Customer lead times
To assign customer lead time for a product in Viindoo, first access the Sales app, then click on Products > Products to open the product list.
Choose a product and navigate to the Inventory tab. Here, you'll find the Customer Lead Time field, where you should input the total days needed to complete a delivery order from its initiation to completion.
Sales security lead time
To configure the sales security lead time in the Inventory app, access the Configuration and Settings section.
Under Advanced Scheduling, find and activate the Security Lead Time for Sales option. Specify the buffer period in days to ensure your team is alerted to prepare shipments ahead of the planned date. This feature helps in managing early shipment preparations effectively.
Deliver several products
When managing orders with multiple products of varying lead times in Viindoo, you can adjust lead times directly within the quotation. Navigate to the "Other Info" tab on the quotation page, where you can set the "Shipping Policy".
- As soon as possible: to expedite delivery based on the shortest product lead time, calculating the delivery order's scheduled date from today.
- When all products are ready: to consolidate the shipment, using the longest lead time among the items to determine the delivery date.
For a quote with a Product A and a Product B having lead times of 8 and 5 days respectively, and today being Jan 2nd, setting the Shipping Policy to "As soon as possible" results in a delivery by Jan 7th, based on the shortest lead time. Choosing "When all products are ready" schedules delivery for Jan 10th, accounting for the longest lead time.
Purchase lead times
Viindoo simplifies the procurement process by automating the calculation of order placement dates from suppliers. It determines the supplier shipment receipt date and purchase order (PO) deadline based on when the product is needed in the warehouse. By considering vendor lead times and purchase security lead times and working backward from the receipt date, Viindoo sets the PO deadline. This deadline indicates the latest date by which the order should be confirmed to ensure its timely arrival by the expected receipt date.
Vendor lead time
To configure vendor lead times for warehouse deliveries in Viindoo, start by accessing a product's details via the Purchase app, under Products. Choose the product you're interested in and switch to the Purchase tab.
Here, you can modify the vendor pricelist by adding a new line. This action allows you to input the vendor's name, the price they offer, and crucially, the Delivery Lead Time for the product. This process ensures accurate and efficient management of delivery expectations from vendors.
Establishing the vendor lead time in Viindoo auto-calculates the item's expected arrival date by adding the vendor lead time to the purchase order (PO) confirmation date. This feature ensures that warehouse staff are alerted if products fail to arrive as anticipated, enhancing inventory management efficiency.
Purchase security lead time
In Viindoo, the Purchase Security Lead Time is set universally within the Inventory application, specifically under the Configuration and Settings menu. This setting, found under the Advanced Scheduling section, introduces a buffer period to safeguard against potential delays in receiving supplies from vendors.
Activating this feature and specifying a buffer duration in calendar days helps ensure smooth operations by accommodating unforeseen supplier delays, thus enhancing supply chain reliability.
Manufacturing lead times
Configuring lead times is key for streamlining the procurement of materials and components in manufacturing. By setting manufacturing and security lead times, businesses can establish a Manufacturing Order (MO) deadline.
This deadline helps ensure the manufacturing process starts on time to meet the scheduled delivery date, optimizing the production workflow and enhancing efficiency in meeting customer demands.
Manufacturing lead time
To adjust manufacturing lead times in Viindoo, access the Manufacturing app, select your product, and then go to the Inventory tab. Here, input the required manufacturing days in the Manufacturing Lead Time field.
For example, inputting a 14-day manufacturing lead time directly in this tab sets the period needed to manufacture the product.
The Manufacturing Order (MO) deadline is then determined by subtracting the manufacturing lead time from the expected delivery date, ensuring production starts on time.
Note that these lead times count every calendar day, excluding considerations for weekends, holidays, or work center capacities.
Manufacturing security lead time
To set up Manufacturing Security Lead Time in Viindoo, navigate through the Manufacturing app to Configuration and then to Settings. Under the Planning section, you'll find an option for Security Lead Time.
Enable this feature by checking the box, and then specify the number of calendar days you desire. This setup introduces a precautionary buffer to mitigate any unforeseen delays in the manufacturing cycle, ensuring smoother operations and on-time production.
Benefits of Using Viindoo for Delivery Scheduling
Viindoo software is a innovation in tackling the myriad challenges associated with delivery scheduling. Its comprehensive suite of tools and features is meticulously designed to address the intricate needs of modern businesses, streamlining the delivery process to achieve unparalleled efficiency and reliability. Here's how Viindoo stands out:
- Streamlined Operations: Viindoo's intuitive platform simplifies the complex process of delivery scheduling, enabling businesses to efficiently plan and execute their delivery operations. By automating routine tasks, Viindoo frees up valuable resources, allowing teams to focus on strategic decision-making.
- Enhanced Customer Experience: At the heart of Viindoo's design is a commitment to elevating the customer experience. By providing accurate delivery estimates and real-time tracking capabilities, Viindoo empowers businesses to keep their customers informed and satisfied, fostering loyalty and trust.
Discover Viindoo Suppy Chain Management Software
The All-in-one SCM Software for SMEs. Optimize stock in-out process leading to increased efficiency, accuracy, and ultimately, cost savings.
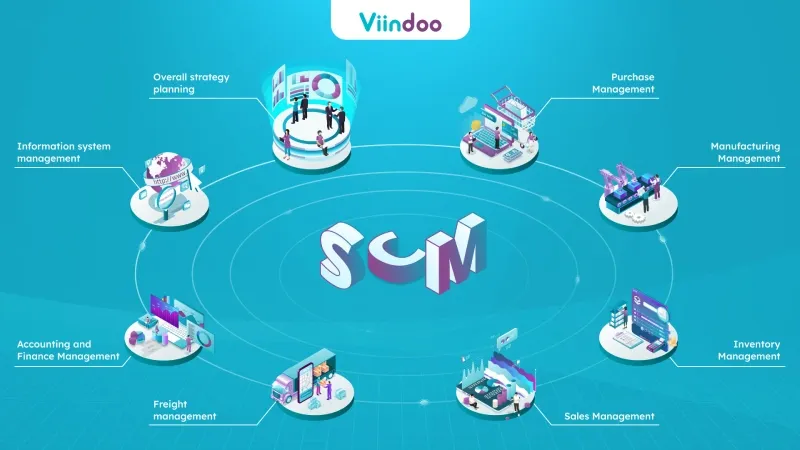
FAQs
By configuring customer and sales security lead times, Viindoo automatically computes the expected delivery date for sales orders.
Yes, Viindoo allows for direct configuration of lead times from the quotation, adjusting delivery schedules accordingly
By setting manufacturing lead times and security lead times to ensure the manufacturing process begins on time.
Conclusion
In the intricate landscape of modern business operations, the efficiency of delivery scheduling can significantly impact a company's ability to meet customer expectations and maintain a competitive edge. Viindoo software is a transformative solution, offering a wide array of benefits designed to streamline delivery scheduling processes.
By harnessing the power of Viindoo, businesses can enjoy enhanced operational efficiency, improved customer satisfaction, and substantial cost savings.