Production costs configuration¶
For manufacturing enterprises, besides accounting operations for purchasing and selling activities, there are other accounting operations for manufacturing such as recording direct or indirect product-related costs, allocation costs, production costs, etc. This article will show you how to configure the accounting accounts for each production stage.
Requirements
This tutorial requires the installation of the following applications/modules:
Set up accounts for product categories of production activities¶
For example, to manufacture a Table (finished product), the company needs to purchase raw materials to produce semi-finished products which are Table legs and Table surfaces, and then assemble them as a Table.
For the settings related to product categories of each raw material, semi-finished product, and finished product category, you can access Inventory > Configuration > Product Categories and see details in the Managing product categories article. You need to set up the accounting rules for each of these product categories as follows:
Raw material products category:
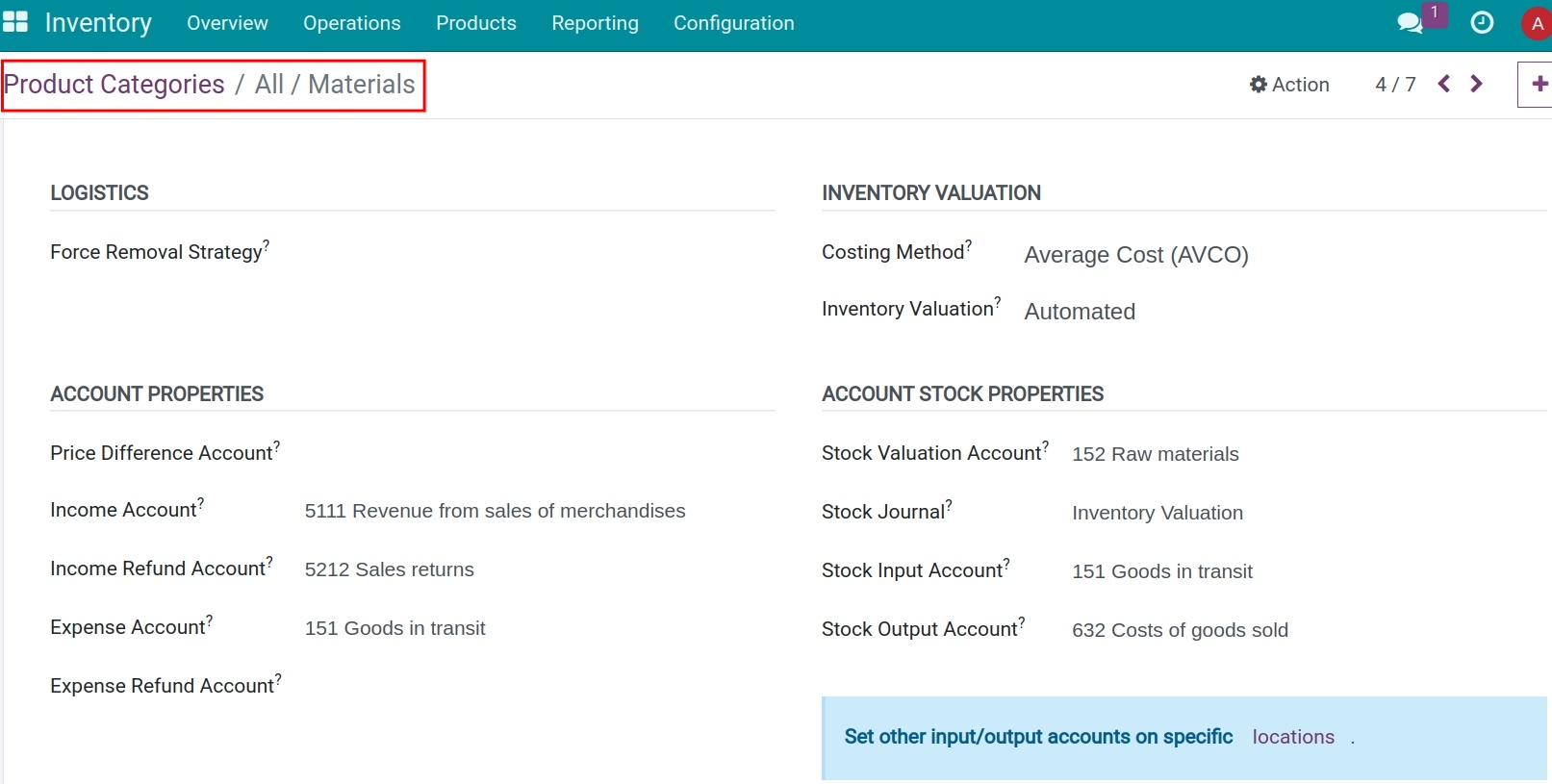
Semi-finished products category:
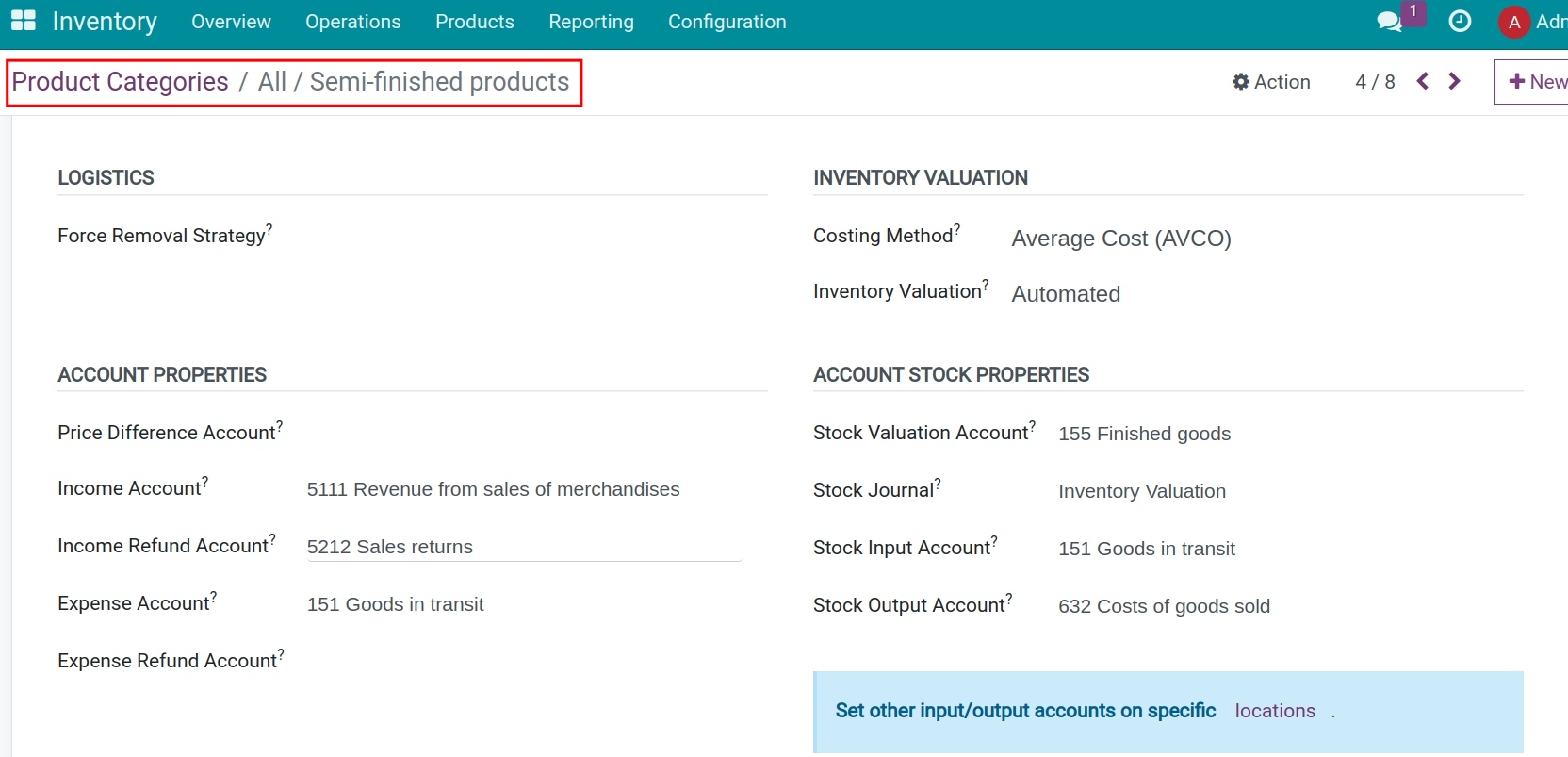
Finished products category:
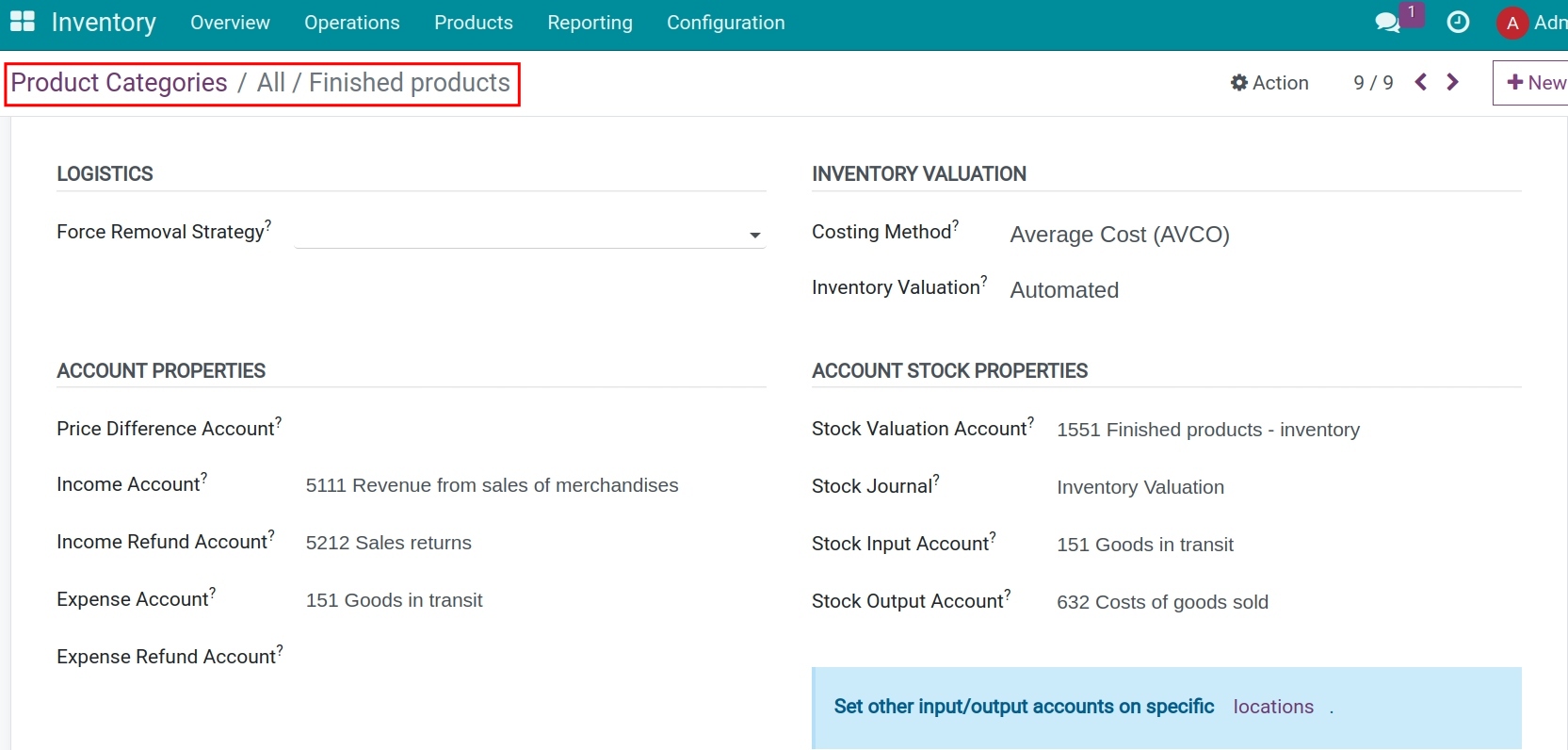
Configure accounting accounts on the production location¶
A production location is a place where semi-finished and finished products are produced from raw materials. The creation time of these production-related journal entries corresponds to the moment raw materials are transformed into semi-finished and finished products. You need to do the following steps:
Navigate to Inventory > Configuration > Location, turn off the default filters, select the location type as Production and fill in the accounting accounts in the Accounting Information section:
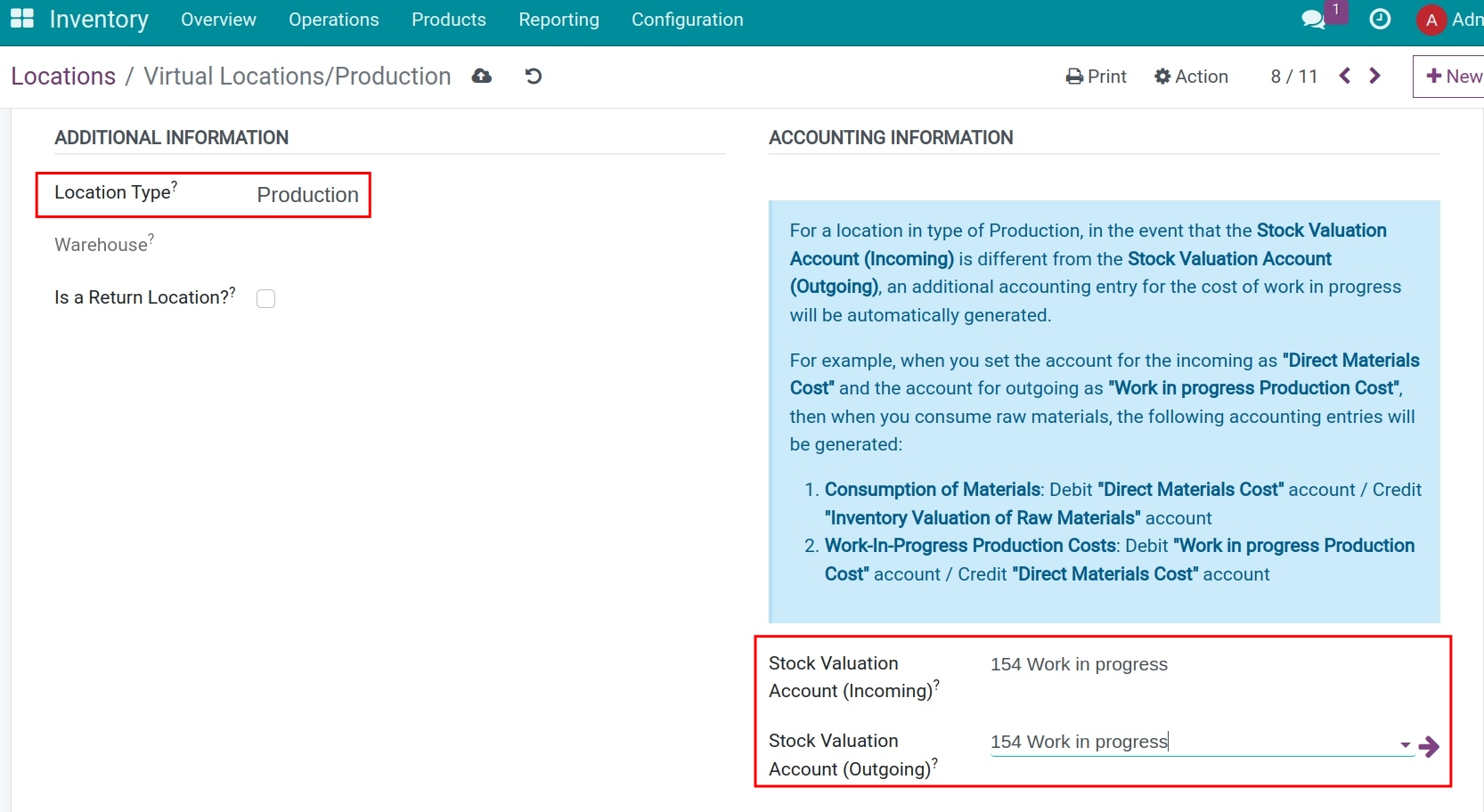
At this point, you can set up accounting accounts as desired as follows:
Method 1: Stock Valuation Account (Incoming) is the same as Stock Valuation Account (Outgoing)
This setting allows the system to automatically make journal entries to the Work in Progress account when:
Example:
Stock Valuation Account (Incoming): 154 - Work in progress
Stock Valuation Account (Outgoing): 154 - Work in progress
Journal Entry:
Transfer the materials to production locations. E.g: Debit (DR) Work in Progress account/Credit (CR) Raw materials account.
Record the semi-finished or finished products. E.g: DR Finished products account/CR Work in Progress account.
Method 2: Stock Valuation Account (Incoming) is different from iStock Valuation Account (Outgoing)
In this setup, the system will automatically create an accounting entry for the work-in-process cost account - 154:
Example:
Stock Valuation Account (Incoming): 621 - Direct raw material cost
Stock Valuation Account (Outgoing): 154 - Work in progress
Journal Entry:
Material consumption entry: Debit 621 / Credit 152;
Entry for recognizing Work in process cost: Debit 154 / Credit 621 (automatically generated);
Recognition of finished product or sale of finished product: Debit 155 / Credit 154.
Configure the cost information on the Work center¶
See details about the configuration of the cost information on the Work center.
See also
Related article
Optional module